A dőlésszög mérése
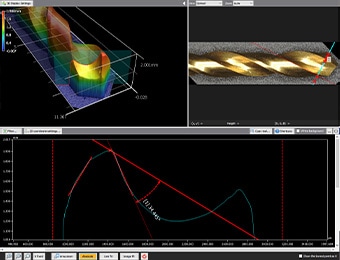
A dőlésszög a vágóeszköz feje és a forgács közötti szög. Ez nagy mértékben befolyásolja a vágási ellenállást, a forgácskibocsátást, a vágási hőt és az élettartamot. A vágószerszám dőlésének ellenőrzése és vezérlése alapvető fontosságú a megfelelő megmunkálás érdekében. Ezek alapján, dőlésszöget nehéz lehet hagyományos eszközökkel mérni. Ez a cikk a dőlésszöggel kapcsolatos alapvető ismereteket magyarázza el, és bemutatja a dőlésszög pontos mérésére használt legújabb technológiát.
- Dőlésszög
- Pozitív és negatív dőlésszög a szármarásban
- A vágószerszám szöge, a dőlésszög és a tehermentesítési szög közötti kapcsolat
- A hagyományos dőlésszög-mérés során felmerülő problémák
- A dőlésszög-mérési problémák megoldása
- Összegzés
Dőlésszög
A vágószerszám fejére szerelt hegynek van egy dőlésszöge, amely lehetővé teszi a forgács eltávozását a munkadarab vágása közben. A dőlésszög az a szög, amely a vágási célmunkadarab felülete (referenciafelület) és azon felület (dőlési felület) között alakul ki, amelyen a forgácsok eltávoznak, amikor a vágószerszám a célmunkadarabot koptatja.
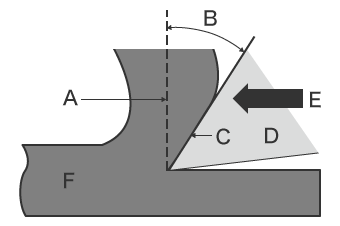
- A
- Referenciafelület (forgácsok)
- B
- Dőlésszög
- C
- Dőlési felület
- D
- Hegy (vágószerszám feje)
- E
- Vágási irány
- F
- Munkadarab
Referenciaként a szerszámfej élének szögét vágószerszám-szögnek nevezzük. A hegy (vágószerszám) dőlt felületével ellentétes oldalon (az ábrán az alsó oldalon) lévő felületet tehermentesítő nevezzük. Azt a szöget, amelyet a munkadarabbal bezár, tehermentesítő szögnek nevezzük. Ez az a szög, amely a szerszám és a munkadarab közötti interferencia elkerüléséhez szükséges.
Pozitív és negatív dőlésszög a szármarásban
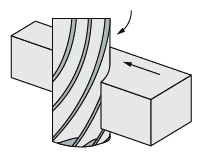
A szármarókat alakzatok és furatok kialakítására használják marás közben, és különféle anyagokat több irányban vághatnak. A szármarót általában pozitív vagy negatív alakzatként írják le, a szerszámfej dőlésszögének megfelelően.
A legtöbb esetben egy olyan pozitív alakzatot választanak, amely kisebb vágási ellenállással rendelkezik a szerszámfejjel szemben. Ezek alapján, negatív dőléssel rendelkező szármaró használható kemény munkadarabok, például nagy keménységű acél vágásához, ahol szilárd szerszámfejre van szükség. Tekintse meg alább a pozitív és negatív alakzat közötti különbségeket.
Pozitív alakzat
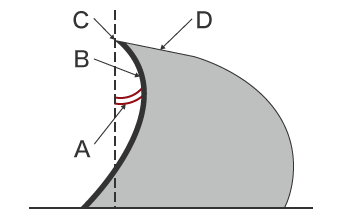
- A
- Dőlésszög = pozitív
- B
- Dőlt felület (a szerszámfej hátsó oldala)
- C
- Szerszámfej éle
- D
- Tehermentesítő felület
- A pozitív dőlésszög jellemzői
-
- A vágópenge éles és a vágási ellenállás kicsi.
- Alacsony fordulatszámon történő megmunkálás esetén is kiváló vágófelületi érdesség érhető el.
- Alkalmas puha anyagokhoz vagy könnyen megmunkálható munkadarabokhoz (réz, alumínium, rozsdamentes acél, műanyag, nyersanyagok, hőkezelt acél).
Negatív alakzat
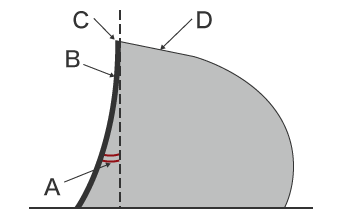
- A
- Dőlésszög = negatív
- B
- Dőlt felület (a szerszámfej hátsó oldala)
- C
- Szerszámfej éle
- D
- Tehermentesítő felület
- A negatív dőlésszög jellemzői
-
- Alacsony sebességű megmunkáláskor a vágási ellenállás nagy, de a vágófelület érdessége csökken.
- Nagy sebességű megmunkáláskor kiváló vágófelületi érdesség érhető el.
- Alkalmas olyan kemény anyagokhoz, ahol valószínű a forgácsolódás (nagy keménységű acél vagy öntöttvas).
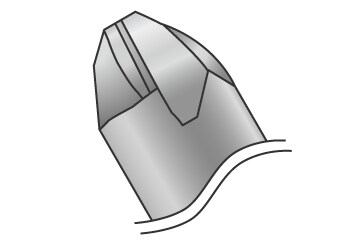
A félgömb alakú hegyű golyós maróval a szerszámfej magja vastagabbá tehető, ha negatív alakzatot használunk a szerszámfej spirálszögéhez. Ez nagyfokú merevség biztosítását teszi lehetővé.
A vágószerszám szöge, a dőlésszög és a tehermentesítési szög közötti kapcsolat
A vágási folyamat során a vágószerszám (általában keményfém szerszám) belemélyed a munkadarabba, hogy az anyagot elvágja, megformázza vagy eltávolítsa.
Nem csak a vágószerszám szögét kell figyelembe vennie, hanem azt is biztosítani kell, hogy a dőlési szög megfelelően legyen beállítva ahhoz, hogy a forgács a megfelelő irányba távozzon. Ezzel együtt a tehermentesítési szöget megfelelően be kell állítani, hogy a szerszám ne érintkezzen a kész felülettel a vágás után. Az egyes szögek közötti elsődleges kapcsolatokat az alábbiakban foglaljuk össze.
Vágószerszám szöge
Nagy keménységű anyagok vágásakor növelni kell a vágószerszám szögét. Ezek alapján, ha a vágószerszám szöge túl kicsi, akkor forgácsolódás vagy repedés léphet fel. Puha vagy kiváló hegesztési tulajdonságokkal rendelkező anyagok vágásakor csökkenteni kell a vágószerszám szögét a vágási teljesítmény javítása érdekében.
Dőlésszög
A dőlésszög határozza meg a forgácsvastagságot és az áramlási irányt.
Minél nagyobb a dőlésszög, annál kisebb a forgács nyírási szöge. A nyírási szög csökkenésével a forgács vékonyabbá válik. Ez csökkenti a vágási erőt és a vágási hőmérsékletet, ami végső soron csökkenti a szerszám kopását. Ezek alapján, ha a dőlésszög túl nagy, az csökkentheti a szerszám élének szilárdságát, ami a kemény anyagok megmunkálásakor megrepedhet.
Kemény anyagok vágásához olyan szerszámot kell használnia, amelynek a dőlésszöge negatív, amint azt a fenti példában is bemutattuk. A negatív dőlésszög miatt forgácsok eshetnek a munkadarab felületére, ami miatt a gép nem a kívánt helyeken fogja elvágni az anyagot. Ezeket a forgácsokat a dőlt felületen „holt fémnek” nevezik. Az ilyen típusú szerszámok használatakor óvatosan kell eljárni, mert az befolyásolhatja a forgácsgyártás körülményeit, a szerszám élettartamát és a kész felület érdességét.
Tehermentesítési szög
A tehermentesítési szögre azért van szükség, hogy elkerüljük a szerszám és a munkadarab közötti interferenciát. A túl nagy tehermentesítési szög csökkenti a vágószerszám élének szilárdságát, így az érzékenyebbé válik a mechanikai ütésekre. Ezek alapján, a nagy tehermentesítési szög még a kopás előrehaladtával sem hoz létre táguló kopási szélességet a tehermentesítő felületen. Ennek az az előnye, hogy kevésbé valószínű a kopogó rezgés. Képlékeny anyagok (például alumíniumötvözetek) vágásakor a tehermentesítési szög növelése csökkenti annak valószínűségét, hogy forgácsok tapadjanak a tehermentesítő felülethez.
A szerszám egyes részeinek szöge szorosan összefügg a munkadarab megmunkálási hatékonyságával, pontosságával, felületének minőségével és a szerszám élettartamával. Mivel ezekben a szögekben a szerszámkopás miatt eltérések léphetnek fel, a szerszám alakjának mérése rendkívül fontos a megmunkálási minőség és hatékonyság fenntartása és javítása szempontjából.
A hagyományos dőlésszög-mérés során felmerülő problémák
A dőlésszög pontos mérése rendkívül fontos, mert a nem megfelelő dőlésszög a szerszám kopását, a holt fém tapadását, rossz felületi érdességet és a szerszám élettartamának csökkenését okozhatja.
A dőlésszög hagyományos mérésére profilmérő rendszert vagy mikroszkópot használnak. Ezek a módszerek azonban a következő problémákat vetik fel.
A profilmérő rendszerrel történő dőlésszög-mérés során felmerülő problémák
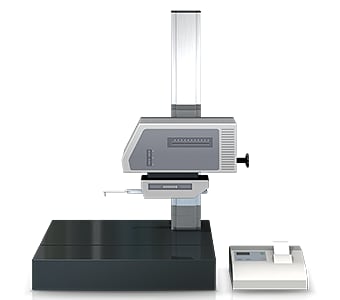
A céltárgy profilját egy profilmérő rendszer méri és rögzíti úgy, hogy a felületét egy érintőceruzával követi végig.
Az elmúlt években olyan profilmérő rendszereket fejlesztettek ki, amelyek érintőceruza helyett lézert használnak az összetett alakzatok mérésére a profil érintésmentes követésével. Egyes modellek képesek a felső és az alsó felület mérésére is.
A szerszám dőlésszögének profilmérő rendszerrel történő mérése a következő problémákat veti fel.
- Mivel a szög túl kicsi, előfordulhat, hogy az érintőceruza nem érintkezik a céllal, és nem lehet megmérni a helyes értéket.
- A dőlési felület újrapolírozása során nehéz megítélni, hogy a beállítások eredményesek voltak-e, ha a mérési kiértékeléseket egy vonalon végzik.
A dőlésszög-mérési problémák megoldása
A közönséges mérőgépek esetében sok időre lehet szükség ahhoz, hogy a céltárgyat egy ülék segítségével rögzítsék. Ezen túlmenően, mivel a mérés pont- vagy vonalérintéssel történik egy háromdimenziós célponton vagy területen, probléma merül fel a cél vagy a mérési pontok kiválasztásánál.
Ezen mérési problémák megoldására fejlesztette ki a KEYENCE a 3D optikai profilmérő VR sorozatát.
Ez az eszköz pontosan rögzíti a teljes célfelület 3D alakját anélkül, hogy érintkezne a céltárggyal. A 3D alakzatot is méri úgy, hogy a céltárgyat mindössze egy másodperc alatt, nagy pontossággal 3D-ben beszkenneli a tárgyasztalon. Képes azonnali és mennyiségi mérés elvégzésére, hiba nélkül a mérési eredményekben. Ez a szakasz a VR sorozat néhány specifikus előnyét mutatja be.
1. előny: Az érintésmentes 3D alakmérés kiváló szögjellemzőkkel lehetséges.
A hagyományos mérőműszerek pontok vagy vonalak rögzítésére korlátozódnak, érintőceruzás szondával. Ez megnehezíti az éles szögű, kicsi vagy összetett alakzatú céltárgyak mérését.
A VR sorozattal az alkatrész teljes felülete azonnal beolvasható, lehetővé téve az érintésmentes 3D alakmérést. Ez lehetővé teszi a célszögjellemzők kiváló megjelenítését azáltal, hogy azonnal képes rögzíteni a teljes 3D alakzat pontos profiladatait. Ezen túlmenően, a VR használata számos előnnyel jár olyan szerszámok mérésénél, mint például a szármaró, ahol az alakzatok és a szögjellemzők finomak és összetettek.
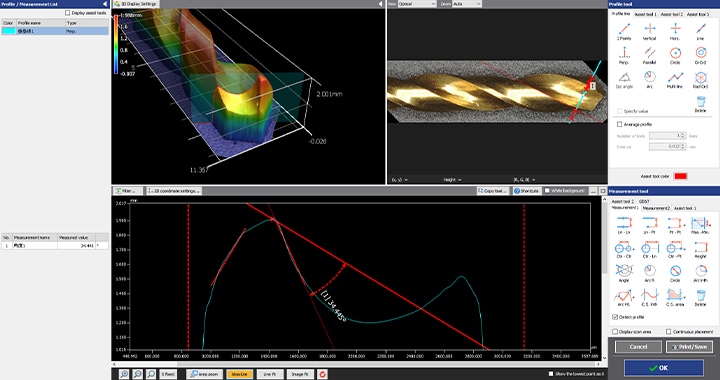
2. előny: A mérések nyomonkövethetők a nemzeti szabványok szerint.
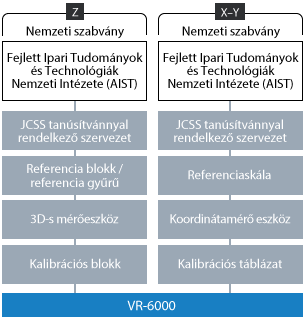
A VR sorozat azonnal és pontosan beolvassa a céltárgy alakját, hogy megmérje azt.
A mérési eredmények egy nemzeti szabványhoz kapcsolódó nyomonkövethetőségi rendszeren alapulnak.
Az XYZ nyomonkövethetőségnek megfelelő mérőeszköz egy JCSS-tanúsítvánnyal rendelkező laboratórium szabványos skálájához kapcsolódik, bármikor lehetővé téve a pontos helyszíni kalibrálást. Ez biztosítja a szabványnak megfelelő, nagy megbízhatóságú mérést.
Összegzés
A VR sorozattal a céltárgy 3D alakzata azonnali, érintésmentes szkenneléssel mérhető. A megfelelő megmunkáláshoz szükséges szerszám dőlésszöge egyszerűen és pontosan mérhető a szerszám tárgyasztalra helyezésével és egyetlen gomb megnyomásával. A VR sorozat használatának előnyei az alábbiak.
- A hagyományos érintéses típusú mérőrendszerekkel ellentétben a VR sorozat a céltárgy alakjától vagy méretétől, illetve a mért hely szögjellemzőitől függetlenül képes pontos mérést végezni.
- A mérési eredmények nemzeti szabványokra vezethetők vissza, így biztosíthatók a megbízható alakmérések. Ez digitális mikroszkóppal lehetetlennek tűnik. Ezzel együtt a rendszer bármikor könnyen kalibrálható.
Összességében a VR sorozat azonnal és pontosan meg tudja mérni a szerszám alakját, beleértve a dőlésszöget is, ami javítja a megmunkálás minőségét, hatékonyságát és a szerszám élettartamát.
A szerszámok mellett a megmunkált munkadarabok pontos 3D alakját is képes mérni. A VR sorozat olyan eszközként írható le, amely a megmunkáló munkaállomáson drasztikusan javítja az összes kapcsolódó munkafolyamat hatékonyságát, valamint a minőséget és a termelékenységet.