A kopás pontos és egyszerű mérésének módszere
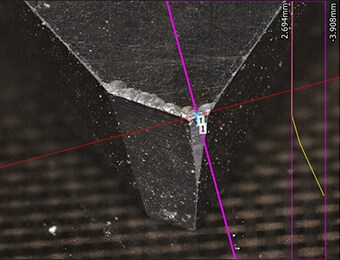
Kopás a szerszámfej-éleknél, a mechanikai alkatrészek csúszó részeinél következik be, és nagy hatással van a teljesítményre. A kopás megmunkálási hibákhoz (hő vagy vibráció miatt) és működési hibákhoz (lazulás miatt), sőt, legrosszabb esetben a gép meghibásodásához vagy károsodásához vezethet.
A kopás megelőzésére olaj vagy más kenőanyag használható. A kopást azonban nehéz teljesen megakadályozni, így továbbra is potenciális kockázati tényező marad. Ezért a kopás mérése elengedhetetlen a termékminőség fenntartásához, a berendezések karbantartásához és a biztonsághoz.
- Kopás
- A kopás típusai
- A kopásmérés szükségessége
- A hagyományos kopásmérés során felmerülő problémák
- A kopásmérés során felmerülő problémák megoldása
- Összegzés: Drasztikus javulás és nagyobb hatékonyság a nehéz kopásmérések során
Kopás
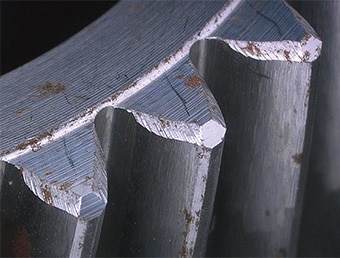
Kopás akkor következik be, amikor a szilárd felület anyaga a súrlódás következtében fokozatosan eltávolítódik. A súrlódást és a kopást külső tényezők (például terhelés, sebesség, hőmérséklet és légkör), valamint mérnöki tényezők (például geometriai forma, alakváltozás és a kapcsolódó felület állapota) befolyásolják.
Az erózió hasonló a kopáshoz, de a folyadék és a szilárd tárgy közötti súrlódás okozta kopást jelöli. Például erózió léphet fel a csőben lévő folyadék és a csőfalak között.
A kopás típusai
A kopás rendkívül nagyszámú, összetett módon egymással kölcsönhatásban lévő paraméter eredményeként következik be. Ez magában foglalja a súrlódás helyét, a súrlódó anyagok fizikai jellemzőit, a környezeti légkört, a hőt, a hőmérsékletet, valamint a fizikai és kémiai hatásokat. Ez a szakasz a kopás néhány jellegzetes típusát mutat be.
Tapadó kopás
Tapadó kopás akkor következik be, amikor két szilárd tárgy egymáshoz dörzsölődik, és összetapad (megtapad), majd eltörik és szétválik. Tapadó kopás a szilárd tárgyak közötti kémiai kötések eredményeként következik be. Emiatt nagyobb valószínűséggel fordul elő a következő típusú szilárd tárgyak között.
- Azonos típusú anyagok
- Olyan anyagok, amelyek azonos kristályszerkezettel és hasonló rácsállandókkal rendelkeznek
Csiszoló kopás
Csiszoló kopás két szilárd tárgy között lép fel, amikor a keményebb anyagon lévő kiemelkedések mechanikusan levágják a lágyabb anyagot. A jellemzők között megtaláljuk a viszonylag jó kenési feltételeket és az alacsony fokú tapadást, valamint azt, hogy a kopás jelentősebb, mint más kopási módok esetében.
Fáradási kopás
Fáradási kopás akkor lép fel, amikor a gördülési súrlódás nagyobb, mint a csúszási súrlódás, például egy csapágy gördülőfelületén vagy egy fogaskerék fogfelületén. A fáradási súrlódáshoz vezető folyamat az alábbiakban látható.
- (1) Ismétlődő feszültség hat a felületre, ahol fémrészek érintkeznek egymással.
- (2) Ez az ismétlődő feszültség a felület fokozatos megkeményedését okozza.
- (3) Finom repedések alakulnak ki, majd egyre nagyobb repedések keletkeznek.
- (4) A felületi réteg elkezd leválni.
A (3) esetében finom repedéseket okozó nyírófeszültség a felülettől kissé beljebb lévő pontban a legnagyobb. A fent leírtakkal megegyező folyamat eredményeként a gördülési fáradás következtében foltszerű gödröcskék keletkeznek a csapágyfelületen, valamint kipattogzás történik, aminek hatására jelentős nagyságú fémdarabok esnek le a fogfelületről az anyagfáradás következtében.
Súrlódási kopás
A súrlódási kopás olyan kopás, amely olyan anyagok érintkezési felületén lép fel, amelyeket úgy terveztek, hogy azok felületén nem kellene, hogy csúszás történjen. A csavarokkal és anyákkal rögzített alkatrészek (vagy két alkatrész érintkezési felülete) ismételt igénybevétele esetén enyhe relatív csúszás (súrlódás) lép fel, ami kopást okoz. Azon a felületen, ahol súrlódási kopás jelentkezik, finom repedések keletkeznek. Mivel a külső terhelés és az ismétlődő feszültség befolyásolja a súrlódási kopás helyét, a fáradási szilárdság az eredeti szint felére vagy kevesebbre csökken (súrlódási fáradás), ami fáradási törést eredményez.
A kopásmérés szükségessége
A megmunkáló szerszámok kopása közvetlenül összefügg a megmunkálás minőségével, az alkatrészek kopása pedig a művelet pontosságával és biztonságával. Emiatt rendkívül fontos a kopási feltételek, például a kopás mértékének mérése. Ebben a szakaszban a kopásmérés fontosságát magyarázzuk el, példaként egy fékbetét és egy vágószerszám-fej segítségével.
Fékbetét kopásának mérése
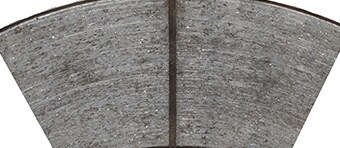
Egy új gépkocsi fékbetét körülbelül 10 mm vastag. Bár az időzítés a gyártótól függően változik, a fékbetétet általában akkor kell cserélni, ha az 1-3 mm-re kopott. A fékbetét tárcsafék esetén a féktárcsával való súrlódás, dobfék esetén a fékdobbal való súrlódás miatt kopik. A féktárcsa és a fékdob is elhasználódik. Mivel a kopási a fékbetét kopott felületén jelennek meg, a fékbetét térfogatának és kopás mértékének mérésével vagy megfigyelésével határozható meg a fékbetét tartóssága és a fékezés során fellépő kopás típusa.
Vágószerszám-fej kopásának mérése
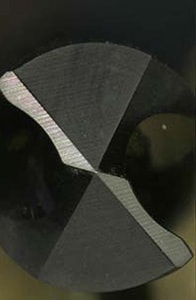
Egy szármaró vagy szerszámfej hegye a munkadarabbal való súrlódás és a vágóforgács miatt kopik el. A kopó alkatrészek az anyagtól függően eltérőek; a legtöbb esetben azonban a kopás a dőlt és a kidomborodó felületeken lép fel. A lehetséges ok az lehet, hogy túl nagy a vágási sebesség vagy nem megfelelő a szerszámfej anyaga. Mivel a szerszámfej terhelése megnő egy nehezen vágható anyag megmunkálásakor, a kopás mértéke nagyobb, mint a hagyományos anyagok megmunkálásánál. Óvatosnak kell lennie, mert a kidomborodó felület súrlódása növelheti a vágási erőt vagy megváltoztathatja a vágási mélységet.
Mindezek miatt a szerszámfej kopásának mérése rendkívül fontos a vágási sebesség értékeléséhez és a szerszámfej anyagának kiválasztásához.
A hagyományos kopásmérés során felmerülő problémák
A kopás mértékét jellemzően profilmérő rendszerekkel vagy koordináta mérőgépekkel mérik. Ezek a módszerek azonban az alábbi mérési problémákkal járnak, amikor nagy területen vagy kisméretű alkatrészeken mérik a kopást.
A profilmérő rendszerrel történő kopásmérés során felmerülő problémák
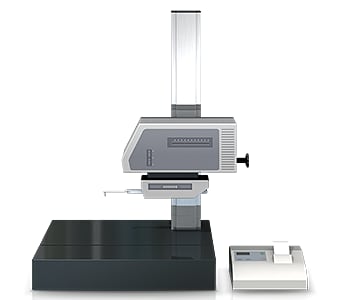
A céltárgy profilját egy profilmérő rendszer méri és rögzíti úgy, hogy a felületét egy érintőceruzával követi végig. Az elmúlt években olyan profilmérő rendszereket fejlesztettek ki, amelyek érintőceruza helyett lézert használnak az összetett alakzatok mérésére a profil érintésmentes követésével. Egyes modellek képesek a felső és az alsó felület mérésére is.
A profilmérő rendszernek pontos mérési vonalat kell rajzolni a kopás mértékét illetően, ami maga a mérés célja.
Ez a következő problémákat veti fel.
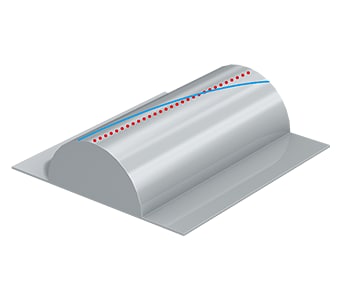
- A mérési munka sok időt igényel, ideértve a minta ülékre rögzítéséhez és vízszintbe állításához szükséges időt. Emellett a profilmérő rendszerek használatához kapcsolódó ismeretek és készségek is szükségesek a céltárgy pontos szintbe állításához.
- A profilmérő-rendszer érintőceruzája felfelé és lefelé egy íven mozog, melynek középpontja az érintőceruza karjának forgástengelye, az érintőceruza hegye pedig az X-tengely irányába mozog, ami az X-tengely adataiban hibát okoz.
- A kívánt vonal végigkövetése az érintőceruzával rendkívül nehéz munka, és már az érintőceruza enyhe elmozdulása is hibát okoz a mért értékekben.
- Nehéz továbbá a céltárgyak számának növelése, mert pontosan meg kell határozni a mérési helyeket.
- A céltárgynak csak egy része mérhető, a teljes felület értékelése nem lehetséges.
A koordináta mérőgéppel történő mérés során felmerülő problémák
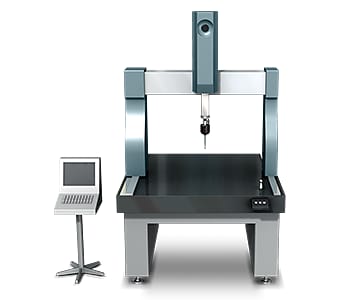
Ha a kopott rész területe kicsi, például 1 mm2, rendkívül nehéz pontosan megmérni az alakzatot úgy, hogy a felületet szondával pontos végigpásztázzuk és egy virtuális felületet hozunk létre. Kis terület mérésénél a pontos 3D alakzat azonosítása is nehézkes a kevés mérési pont miatt. A kapcsolódó feladatok is sok munkát jelentenek, mint például a mérési adatok táblázatba foglalása és az eredmények összehasonlítása a rajzokkal.
A kopásmérés során felmerülő problémák megoldása
A hagyományos mérőműszerek háromdimenziós egy céltárgyat vagy területet mérnek pontok és vonalak érintésével. Ez problémákat okoz, mivel a felhasználók nem tudják beazonosítani a teljes alakzatot, és a mért értékek megbízhatósága alacsony. Ezen mérési problémák megoldására fejlesztette ki a KEYENCE a 3D optikai profilmérő VR sorozatát.
A VR sorozat pontosan rögzíti a teljes célfelület 3D alakját anélkül, hogy érintkezne a céltárggyal. A 3D alakzatot is méri úgy, hogy a céltárgyat mindössze egy másodperc alatt, nagy pontossággal 3D-ben beszkenneli a tárgyasztalon. Képes azonnali és mennyiségi mérés elvégzésére, hiba nélkül a mérési eredményekben. Ez a szakasz a VR sorozat néhány specifikus előnyét mutatja be.
1. előny: Gyűjtse összes 800 000 mérési pont adatait akár egy másodperc alatt.
A VR sorozat a teljes felület alakját méri, és egy 800 000 pontból álló csoportból gyűjt adatokat. Mivel a mérés nem vonalak vagy pontok használatával történik, nincs szükség ismételt mérésre, ami csökkenti a mérési időt. A nehezen meghatározható tételek, például a kopás mértéke, a térfogat vagy a felület alapján értékelhető. A síklapúság kvantitatív értékelése is könnyen elvégezhető. A VR sorozat bizonyos helyeken profilokat is képes mérni. A 3D szkennelési adatokból még mérés után is lekérhetők a különböző alkatrészek profiljai anélkül, hogy a céltárgyat újra be kellene szkennelni.
A mérési adatok tárolásra kerülnek, és a tárolt adatok összehasonlíthatók más adatokkal vagy 3D tervadatokkal.
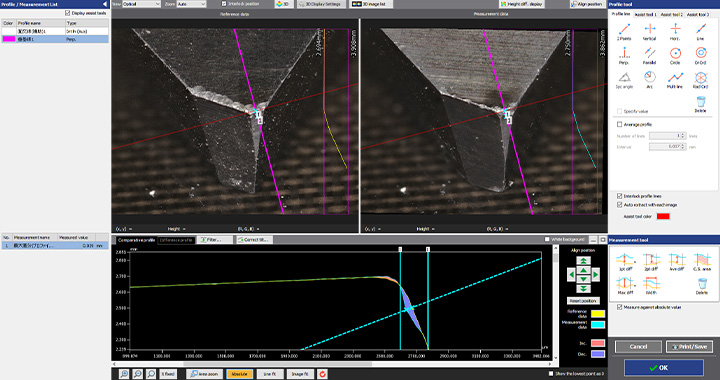
2. előny: Akár 300 mm x 150 mm széles terület mérésére is alkalmas.
A mérés egyszerűen elvégezhető a céltárgy tárgyasztalra helyezésével és egy gomb megnyomásával. Szigorú pozicionálás vagy egyéb előkészítés nem szükséges. Ez lehetővé teszi nagy pontosságú mérések elvégzését olyan operátorok számára, akik nem rendelkeznek a mérőműszerekkel kapcsolatos tudással vagy tapasztalattal.
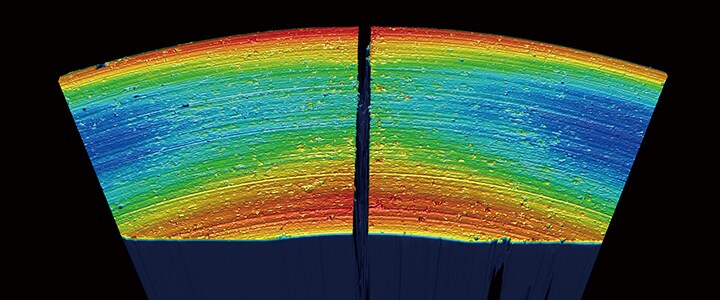
Mivel a VR sorozat kinyeri a tárgyasztalra helyezett céltárgy jellemzőit, és automatikusan korrigálja a helyzetét, nincs szükség szigorú, sok időt és erőfeszítést igénylő pozicionálásra. A VR sorozat akár 300 mm x 150 mm széles területet is képes mérni, több mérési kép összefűzésével. Ez még egy tapasztalatlan operátor számára is lehetővé teszi, hogy egyszerűen és azonnal végezzen méréseket, és nincs szükség arra, hogy speciális operátort rendeljenek a mérési munkákhoz.
A VR sorozattal nagy felületet, például nagy fékbetétet lehet pontosan mérni, mindössze a céltárgy tárgyasztalra helyezésével és egyetlen gomb megnyomásával.
Összegzés: Drasztikus javulás és nagyobb hatékonyság a nehéz kopásmérések során
A VR sorozat pontos és azonnali 3D céltárgy mérést tesz lehetővé, nagysebességű 3D szkenneléssel anélkül, hogy érintkezne a céltárggyal. Megoldja a hagyományos mérőműszerekkel kapcsolatos összes problémát azáltal, hogy lehetővé teszi a kopófelület legmagasabb és legalacsonyabb pontjainak mérését, valamint a térfogat, a keresztmetszeti terület, valamint a felület és a keresztmetszeti terület arányának mérését.
- Képes egyszerre pontosan mérni a legmagasabb pontot, a legalacsonyabb pontot, a területet, a térfogatot és a felületet.
- Ez kiküszöböli az emberi tényezőkből adódó eltéréseket, lehetővé téve a valódi mennyiségi mérést.
- A mérés egyszerűen elvégezhető a céltárgy tárgyasztalra helyezésével és egyetlen gomb megnyomásával, pozicionálás vagy egyéb előkészítés nélkül. Így nincs szükség speciális operátor kijelölésére a mérési munkákhoz.
- A 3D alakzatok könnyen, nagy sebességgel, nagy pontossággal mérhetők. Ez lehetővé teszi nagyszámú céltárgy rövid idő alatt történő mérését, elősegítve a minőség javítását.
Ez a rendszer lehetővé teszi a korábbi 3D alakzatadatokkal és CAD-adatokkal való összehasonlítást, valamint az egyszerű adatelemzést, például a tűréshatárokon belüli eloszlást. Hatékonyan használható számos célra, beleértve a termékfejlesztést, a gyártási trendelemzést és a mintavételi ellenőrzéseket.