Onmiddellijke en nauwkeurige meting van complexe 3D-vormen van lasrups
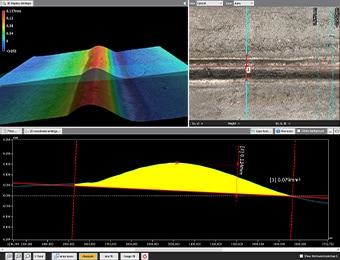
Lassen is een methode om twee materialen (onedele metalen) bij verbindingen met elkaar te verbinden door middel van energie zoals hitte of druk, met of zonder gebruik van een toevoegmetaal. Lasrupsen, die ontstaan bij het lassen, zijn uiterst belangrijke onderdelen die een groot effect hebben op de verbindingssterkte en de productkwaliteit. Aan de hand van de vorm van de lasrusp kan worden beoordeeld of de las goed is gemaakt en of er gebreken of defecten aanwezig zijn. Om een lasrusp correct te evalueren, is het noodzakelijk de complexe 3D-vorm kwantitatief te meten, en dit brengt een aantal problemen met zich mee.
Op deze pagina wordt de basiskennis over lasrupsen uitgelegd, alsook de nieuwste methode om eenvoudig en onmiddellijk nauwkeurige 3D-vormen van lasrupsen te meten.
- Lasrupsen
- Optimale afmetingen en vorm van lasruspen
- Defecten in de vorm van lasruspen
- Oplossingen voor het meten van lasruspvormen
- Samenvatting: Het VR-systeem zorgt voor een drastische verbetering bij het meten van lasruspvormen die voorheen moeilijk nauwkeurig te meten waren
Lasrupsen
Wanneer onedele metalen worden verbonden door middel van booglassen, laserlassen of soortgelijke middelen, zijn de lasruspen convexe, afgeronde delen die op het oppervlak bij de verbindingen worden gemaakt. Omdat lasruspen worden gevormd in de vorm van een koord, wordt het proces ook wel rijgen genoemd.
Bij het vervaardigen van metalen buizen voor verschillende doeleinden wordt de lasrusp gevormd door hoogfrequent lassen aan de verbinding van het onedel metaal na het walsen. Bij verschillende andere lasmethoden wordt de verbinding waar het metaal en het onedel metaal worden gesmolten nog steeds een lasrups genoemd, zelfs als er bijna geen stijgende vorm is.
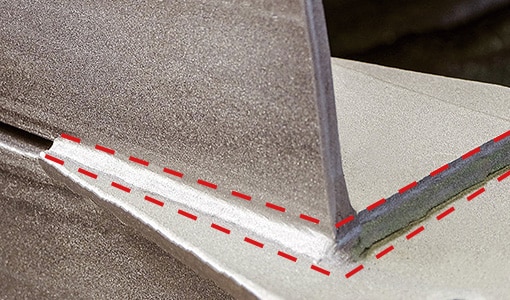
Optimale afmetingen en vorm van lasruspen
In dit gedeelte wordt de vorm van de lasrups uitgelegd voor de typische lasmethode booglassen.
De vorm van de lasrups is correct als deze voldoet aan de voorgeschreven afmetingen.
Voorgeschreven afmetingen en vorm van lasrupsen
De optimale afmetingen van de lasrups zijn gestandaardiseerd en het is belangrijk dat tijdens de ontwikkeling, het ontwerp, de processen en het productieproces aan de vereisten wordt voldaan.
Hieronder staan enkele veelvoorkomende voorgeschreven afmetingen:
- Keeldikte - De minimale dikte van de lasrups.
- Penetratiediepte - De afstand van de top van het gesmolten onedel metaal tot het oppervlak van het onedel metaal.
- Beenlengte - De minimale lengte van de lasrups aan de basis van de verbinding tot de teen van de lassnavel.
In de las in onderstaande afbeelding is de beoordelingsnorm voor optimale lasrups bijvoorbeeld of de beenlengte 80% of meer is van de dunnere dikte van het onedel metaal. Wanneer de dikte van het dunnere onedel metaal 20 mm is, is een beenlengte van ongeveer 16 mm vereist en dit bepaalt de lasrupsbreedte.
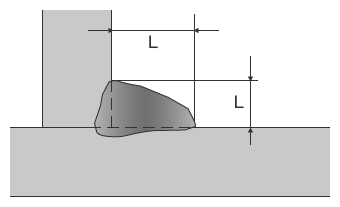
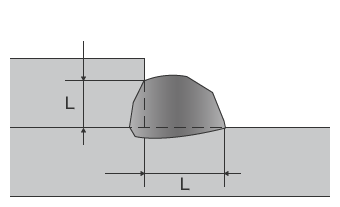
Afmetingen van lasrups en lasstroom
Bij booglassen is de lasstroom een factor die de afmetingen van de lasrups beïnvloedt. Een grotere stroom produceert grotere lasrupsen, terwijl een kleinere stroom kleinere lasrupsen produceert. Als de lasrups niet voldoet aan de vereiste afmetingen of vorm, is het noodzakelijk de lasomstandigheden, zoals de lasstroom of de bewegingssnelheid van de toorts, te corrigeren.
Defecten in de vorm van lasruspen
Naast afmetingen zijn er in de vorm van het lasrupsoppervlak een aantal defecten die aandacht vereisen. Hier zullen we aan de hand van illustraties enkele typische lasrupsdefecten en hun oorzaken toelichten.
Overlapping
- [Fenomeen]
- Overlapping verwijst naar omstandigheden waarin het gesmolten metaal dat op het oppervlak van het onedel metaal overstroomt, afkoelt en stolt als een lasrups zonder samen te smelten met het onedel metaal.
- [Oorzaak]
- Overlapping wordt veroorzaakt door een lage lassnelheid en overmatige toevoer van lasmetaal. Overlapping in hoeklassen wordt veroorzaakt door het druppelen van overtollig gesmolten metaal veroorzaakt door de zwaartekracht.
-
Te weinig vulling
- [Fenomeen]
- Er is sprake van te weinig vulling wanneer er niet genoeg vulmetaal in de las zit, waardoor de totale dikte van de las minder is dan de dikte van het onedel metaal.
- [Oorzaak]
- Te weinig vulling wordt veroorzaakt door onjuiste lasomstandigheden (lasstroom of snelheid).
-
Ondersnijding
- [Fenomeen]
- Ondersnijding is een groef die zich vormt bij de lasrups bij het lassen op onedel metaal of een eerdere las.
- [Oorzaak]
- Ondersnijding wordt meestal veroorzaakt door een te hoge lasstroom of lassnelheid.
-
Putten
- [Fenomeen]
- Putten zijn oppervlaktedefecten die ontstaan wanneer zich in het lasmetaal gasholten vormen, die stollen en een gat in het lasoppervlak veroorzaken wanneer het gas ontsnapt. Gasholtes die stollen in de lasrups zijn interne defecten die blaasgaten worden genoemd.
- [Oorzaak]
- De oorzaken van putten zijn problemen met het beschermgas; onvoldoende deoxidatiemiddel; olie, roest, plating of ander materiaal dat hecht aan het oppervlak van de groef van onedel metaal; en vocht in het materiaal.
-
- A
- Put
- B
- Blaasgaten
Scheuren (lasrusp en oppervlak van onedel metaal)
- [Soorten en verschijnselen]
- Scheuren verwijzen naar scheuren die zich direct na het lassen in een hete las vormen. Scheuren worden grofweg verdeeld in stollingsscheuren en vloeibaarheidsscheuren. Stollingsscheuren treden op wanneer de las stolt. Vloeibaarheidsscheuren treden op bij meerlagig lassen wanneer de vorige laslaag wordt gesmolten door daaropvolgend lassen. Afhankelijk van de locatie en vorm worden scheuren geclassificeerd als lengtescheuren, teenscheuren, dwarsscheuren of kraters.
-
- A
- Lengtescheur
- B
- Teenscheur
- C
- Dwarsscheur
- D
- Krater
Naast de defecten die kunnen worden geïdentificeerd aan de hand van de vorm en het uiterlijk, zijn er andere defecten die de verbindingssterkte beïnvloeden.
- Onvolledige penetratie - wanneer de laspenetratie niet de vereiste diepte bereikt vanwege onvoldoende verhitting
- Onvolledige fusie - wanneer het gesmolten metaal op een bepaalde locatie niet versmelt met het onedel metaal.
Omdat dit interne defecten zijn, is inspectie met dwarsdoorsnedemonsters noodzakelijk.
Oplossingen voor het meten van lasruspvormen
Inspecties zijn essentieel om de kwaliteit van lasrupsen te waarborgen. Visuele vergelijkingen met behulp van goede productmonsters en meters vereisen een hoog niveau van vaardigheid en veel tijd, en het oordeel kan per persoon verschillen. Vanwege het systeem en de nauwkeurigheid zijn geautomatiseerde inline inspectiemachines in veel gevallen niet geschikt voor doeleinden zoals gebruik tijdens de R&D-fase, testen voor het bepalen van de lasomstandigheden, steekproefinspecties of 100% productinspectie van meerdere producten die in kleine hoeveelheden worden geproduceerd.
Om deze meetproblemen van lasrupsen op te lossen, heeft KEYENCE de 3D Optical Profilometer VR Series ontwikkeld.
De VR-serie legt nauwkeurig de 3D-vorm van het volledige oppervlak van het voorwerp vast zonder het aan te raken. Het meet ook de 3D-vorm door het object op het platform in amper één seconde met hoge nauwkeurigheid in 3D te scannen. Ze is in staat tot onmiddellijke en kwantitatieve metingen. In dit gedeelte worden enkele specifieke voordelen van de VR-serie geïntroduceerd.
Voordeel 1: Voltooi de meting in amper één seconde. De 3D-vorm van het volledige doeloppervlak kan nauwkeurig worden vastgelegd met één enkele meting.
De VR-serie verzamelt onmiddellijk oppervlaktegegevens (800.000 gegevenspunten met een enkele scan) in amper één seconde. Dit maakt een zeer nauwkeurige en onmiddellijke meting en kwantitatieve evaluatie van de 3D-vormen voor complexe lasrupsen mogelijk.
De maximale en minimale oppervlakte-onregelmatigheden kunnen op een begrijpelijke manier worden weergegeven in een kleurenkaart, waardoor het mogelijk is om de locaties van defecten te identificeren. Het is ook mogelijk gedetailleerde profielgegevens te verkrijgen door simpelweg elke gewenste locatie op het voorwerp te specificeren, zoals de locaties van defecten.
Zelfs na de meting kunnen profielgegevens voor andere gebieden worden verkregen uit eerdere 3D-scangegevens, zodat het voorwerp niet opnieuw hoeft te worden gescand. Bovendien kunnen meetgegevens van meerdere voorwerpen naast elkaar worden vergeleken en kunnen de gewenste omstandigheden op meerdere datasets tegelijk worden toegepast. Dit resulteert in een drastische vermindering van de manuren en een verbeterde werkefficiëntie.
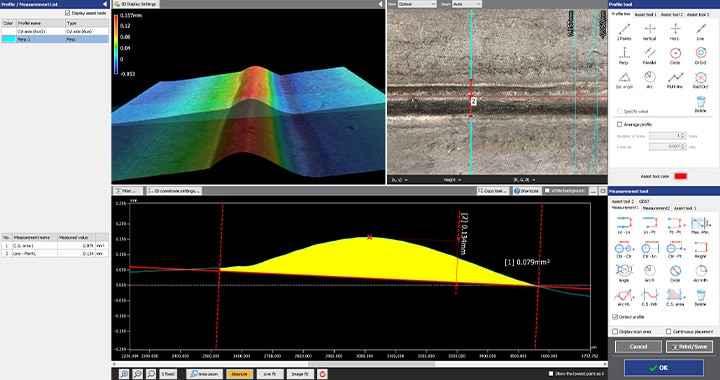
Voordeel 2: De bediening is eenvoudig en de meting kan door iedereen worden uitgevoerd zonder meetafwijkingen tussen operators.
3D-vormmeting kan eenvoudig worden uitgevoerd door het voorwerp op het platform te plaatsen en op een knop te drukken. Deze serie bevat de eerste Slimme Meetfunctie in de branche die automatisch het meetbereik configureert en het platform verplaatst in overeenstemming met de grootte van het voorwerp. Dit elimineert het werk dat nodig zou zijn om de meetlengte en het Z-bereik in te stellen.
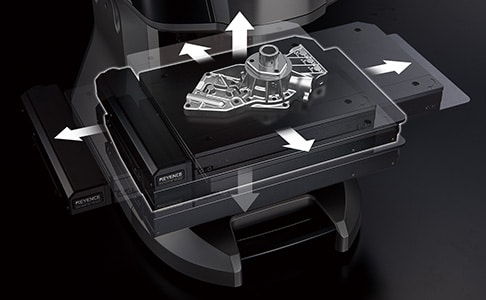
De grote verscheidenheid aan ondersteunende hulpmiddelen maakt een eenvoudige en intuïtieve configuratie van de gewenste meetomstandigheden mogelijk.
Naast de eenvoudige configuratie zorgen de ondersteunende hulpmiddelen ervoor dat het systeem gemakkelijk kan worden bediend, zelfs door beginners, waardoor het ook voor operators die niet met meten vertrouwd zijn mogelijk wordt in amper één seconde nauwkeurige metingen uit te voeren. Als gevolg hiervan kan het aantal monsters eenvoudig worden verhoogd, niet alleen voor R&D en testen om de voorwaarden te bepalen, maar ook voor het meten en inspecteren van producten tijdens commerciële productie.
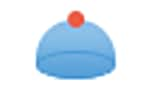
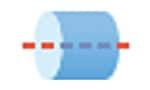
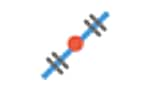
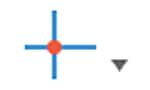
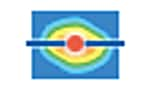
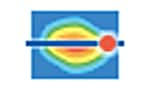
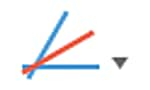
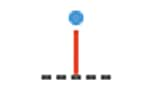
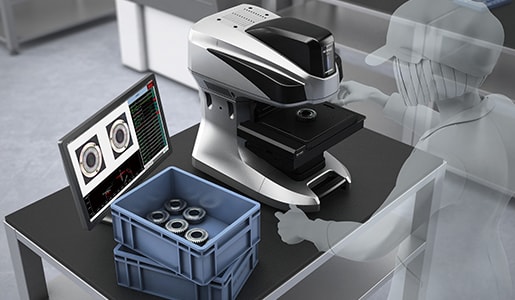
Samenvatting: Het VR-systeem zorgt voor een drastische verbetering bij het meten van lasruspvormen die voorheen moeilijk nauwkeurig te meten waren
De VR-serie kan 3D-vormen van het voorwerp nauwkeurig en onmiddellijk meten door met hoge snelheid in 3D te scannen zonder het voorwerp aan te raken. Moeilijke metingen, zoals het identificeren van complexe onregelmatigheden in 3D-lasrupsvormen en het identificeren van defecten, kunnen in amper één seconde worden voltooid. De VR-serie kan alle problemen met conventionele meetinstrumenten oplossen.
- Abnormale locaties op een lasrups kunnen worden gevisualiseerd in een kleurenkaart.
- Zodra een scan is voltooid, kan op elk moment een profielmeting van elk onderdeel en een vergelijking van meerdere datasets worden uitgevoerd.
- Zonder dat positionering of andere voorbereiding nodig is, kan de meting eenvoudig worden uitgevoerd door het voorwerp op het platform te plaatsen en op een knop te drukken. Hierdoor is het niet meer nodig een gespecialiseerde operator voor meetwerk aan te stellen.
- Doordat 3D-vormen eenvoudig tegen een hoge snelheid en met een hoge nauwkeurigheid kunnen worden gemeten, kunnen er in korte tijd een groot aantal monsters worden gemeten. Dit is handig voor kwaliteitsverbeteringen.
- Dit elimineert afwijkingen als gevolg van menselijke factoren, waardoor echte kwantitatieve metingen mogelijk worden.
Dit systeem maakt vergelijkingen met CAD-gegevens en eenvoudige gegevensanalyse mogelijk, zoals verdeling binnen toleranties. Het kan effectief worden gebruikt voor een breed scala aan doeleinden, waaronder onderzoek en ontwikkeling, bepaling van lasomstandigheden, monsterinspecties, 100% inspectie van producten in kleine partijen en analyse van productietrends.