Rozwiązanie problemów z pomiarem odkształceń po obróbce cieplnej
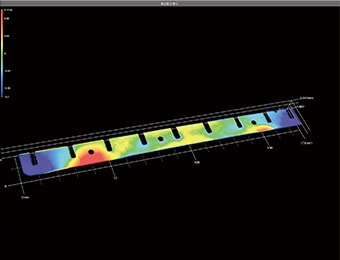
Ogólnie rzecz biorąc, obróbka cieplna to proces polegający na ogrzewaniu materiałów lub produktów. Obejmuje to obróbkę metali przez ogrzewanie oraz sterylizację cieplną żywności i innych produktów. W tej sekcji skupiono się na odkształceniu metalu wynikającemu z procesu obróbki cieplnej. Mimo że tego typu odkształcenie może być proste, takie jak ściśnięcie lub wypaczenie w przypadku kwadratowych belek i prętów, odkształcenie trójwymiarowe może wystąpić w przypadku produktów o złożonych kształtach. Wymaga to zaawansowanych technologii pomiaru tych kształtów.
Na tej stronie przedstawiono podstawowe informacje na temat odkształcenia spowodowanego przez obróbkę cieplną wykorzystywaną w przypadku materiałów z żeliwa i stali, aby kontrolować ich struktury i poprawić właściwości. Obejmuje to również problemy z pomiarem odkształcenia i niektóre potencjalne rozwiązania.
- Obróbka cieplna metalu
- Przykładowe odkształcenie spowodowane przez obróbkę cieplną (zmiana objętości z powodu przemiany fazowej)
- Środki zapobiegania problemom z odkształceniem spowodowanym przez obróbkę cieplną
- Problemy z konwencjonalnym pomiarem odkształcenia po obróbce cieplnej
- Rozwiązanie problemów z pomiarem odkształcenia po obróbce cieplnej
- Podsumowanie: znaczne usprawnienia pomiaru odkształcenia po obróbce cieplnej
Obróbka cieplna metalu
Obróbka cieplna metali to technika, w ramach której metal ogrzewa się i schładza w celu zmiany jego właściwości bez zmiany kształtu. Niektóre właściwości można modyfikować, w tym wytrzymałość, twardość, ciągliwość, odporność na uderzenia, odporność na zużycie, odporność na korozję, właściwości obróbki i urabialność na zimno.
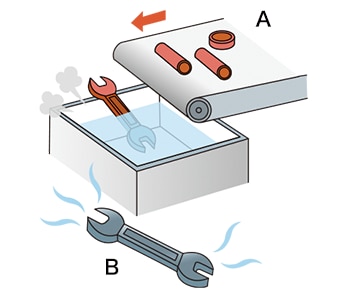
- A
- Ogrzewanie (aż metal stanie się czerwony)
- B
- Chłodzenie (aż ogrzewany metal stanie się czarny)
Przykładowe odkształcenie spowodowane przez obróbkę cieplną (zmiana objętości z powodu przemiany fazowej)
Istnieje wiele metod obróbki cieplnej, w tym hartowanie, odpuszczanie, wyżarzanie i normalizowanie. W trakcie tych procesów zachodzi zjawisko znane jako przemiana fazowa.
Przemiana fazowa to proces występujący podczas obróbki cieplnej, gdy metal zmienia stan skupienia ze stałego na płynny, a następnie z powrotem z płynnego na stały. Dzieje się tak, ponieważ bieżąca forma (struktura) metalu się zmienia, gdy jego sieć krystaliczna przechodzi przemianę na skutek działania temperatury. Gdy struktura zmienia się podczas przemiany fazowej, dochodzi również do zmiany objętości, co powoduje wystąpienie odkształcenia.
Na przykład gdy stal eutektoidalna, która jest stalą zawierającą około 0,8% węgla, ogrzewana jest od temperatury pokojowej, aby utworzyć strukturę austenityczną, a następnie schładzana, ulega ona odkształceniu ze względu na zmianę struktury. Struktura po przemianie fazowej różni się w zależności od metody chłodzenia, która wywiera również wpływ na zakres odkształcenia.
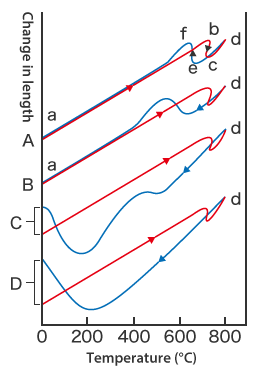
Wykres przedstawia różnice w zakresie odkształcenia wynikające z poszczególnych metod chłodzenia.
W przykładzie A metal rozszerza się na skutek ogrzewania (a → b) i zmienia wymiary ze względu na przemianę fazową, do której dochodzi przy temperaturze około 750°C podczas ogrzewania (b → c) i około 730°C podczas chłodzenia (e → f).
W przykładzie C (chłodzenie olejem) i D (chłodzenie wodą) można zaobserwować widoczną zmianę długości po chłodzeniu.
- A: chłodzenie w piecu (powolne chłodzenie)
- Metal jest przechowywany i chłodzony w piecu po zakończeniu ogrzewania. Metoda ta umożliwia chłodzenie metalu z szybkością około 30°C na godzinę. Po przemianie fazowej metal ma strukturę perlitu.
- B: chłodzenie powietrzem
- Metal zostaje wyjęty z pieca po ogrzewaniu i chłodzi się w temperaturze pokojowej. Po przemianie fazowej ma strukturę sorbitu.
- C: chłodzenie olejem
- Rozgrzany metal jest chłodzony w oleju. Zazwyczaj chłodzenie następuje w oleju o temperaturze 60–80°C. Po przemianie fazowej część struktury austenitycznej przekształca się w troostyt.
- D: chłodzenie wodą
- Metal chłodzony jest w wodzie o temperaturze około 40°C. Po przemianie fazowej ma strukturę martenzytu.
Środki zapobiegania problemom z odkształceniem spowodowanym przez obróbkę cieplną
Oprócz przemiany fazowej opisanej w poprzedniej sekcji inne przyczyny prowadzące do problemów z odkształceniem spowodowanym przez obróbkę cieplną obejmują nieprawidłowy lub nierówny kształt powierzchni lub ogrzewanie/chłodzenie. W tej sekcji przedstawiono te problemy z odkształceniem, ich przyczyny i środki zapobiegania ich wystąpieniu.
Pęknięcia spowodowane hartowaniem
W przypadku tego problemu dochodzi do pękania materiału. Może to nastąpić dzień po hartowaniu lub na późniejszym etapie po schłodzeniu materiału do temperatury około 200°C lub niższej.
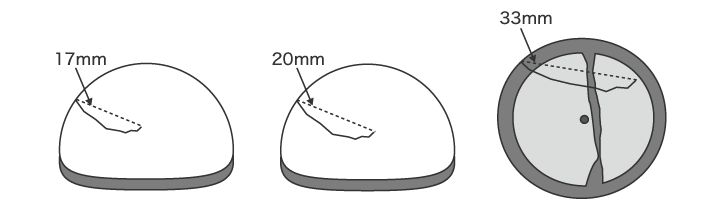
- Przyczyny:
- Możliwe przyczyny obejmują wady kształtu wskutek zwiększenia objętości ze względu na nierównomierne ogrzewanie lub chłodzenie, nieprawidłowe odpuszczanie natychmiast po hartowaniu oraz zbyt wysoką temperaturę hartowania.
- Środki zaradcze:
-
- Sprawdzenie kształtu produktu i warunków powierzchniowych.
- Nie schładzanie hartowanych materiałów do temperatury około 200°C lub niższej.
- Przeprowadzenie procedury odpuszczania materiałów natychmiast po hartowaniu.
- Zmniejszenie temperatury hartowania.
Pęknięcia spowodowane szlifowaniem
W przypadku tego problemu dochodzi do pękania stali podczas szlifowania po obróbce cieplnej. Istnieją dwa typy pęknięć: spowodowane szlifowaniem typu 1, które występują, gdy powierzchnia obrabiana w ramach cięcia, polerowania lub innej metody osiągnie temperaturę około 100°C, oraz spowodowane szlifowaniem typu 2, które występują, gdy powierzchnia obrabiana w ramach cięcia, polerowania lub innej metody osiągnie temperaturę około 300°C.
-
Pęknięcie spowodowane szlifowaniem typu 1
-
Pęknięcie spowodowane szlifowaniem typu 2
- Przyczyny:
- Rozszerzanie pozostałości austenitu, gdy przekształca się w martenzyt. Naprężenie spowodowane przez tego typu rozszerzanie prowadzi do pęknięcia materiału. Takie odkształcenie może również wystąpić, gdy powierzchnia obrabiana przez skrawanie, polerowanie lub inną metodę osiągnie temperaturę 650–850°C.
- Środki zaradcze:
-
- Przeprowadzenie procedury odpuszczania w prawidłowy sposób.
- Zmniejszenie ciepła generowanego przez tarcie podczas szlifowania.
Odkształcenie spowodowane przez hartowanie
Istnieją dwa typy odkształcenia stali spowodowanego przez obróbkę cieplną: odkształcenie termiczne wskutek rozszerzania lub kurczenia termicznego podczas hartowania lub odpuszczania oraz zmiana objętości spowodowana przez przemianę fazową.
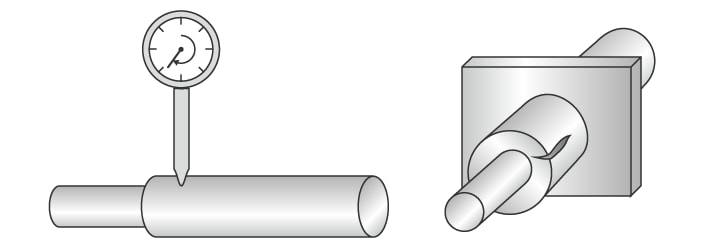
- Przyczyny:
- To odkształcenie występuje z powodu nierównomiernego ogrzewania lub chłodzenia, szybkiego ogrzewania lub chłodzenia lub części o nierównomiernej grubości. Gdy materiał ma złożony kształt, nierównomierny rozkład temperatury w materiale może również spowodować tego rodzaju odkształcenie.
- Środki zaradcze:
-
- Sprawdzenie kształtu, aby produkt mógł być równomiernie ogrzewany i chłodzony.
- Zmniejszenie szybkości ogrzewania i chłodzenia.
Problemy z konwencjonalnym pomiarem odkształcenia po obróbce cieplnej
Niezwykle ważne jest sprawdzenie, czy wymiary i kształty po obróbce cieplnej mieszczą się w granicach tolerancji. Produkty o złożonych kształtach w szczególności wymagają ilościowego pomiaru kształtu 3D z zachowaniem dużej dokładności.
Konwencjonalny pomiar odkształceń powstających po obróbce cieplnej opiera się na wykorzystaniu systemu pomiaru profilu lub współrzędnościowej maszyny pomiarowej. Niemniej jednak mogą wystąpić różne problemy z pomiarem za pomocą konwencjonalnej współrzędnościowej maszyny pomiarowej lub systemu pomiaru profilu. Obejmuje to uzyskiwanie dokładnych pomiarów z wysokim poziomem trudności, co skutkuje zmiennością mierzonych wartości.
Problemy z pomiarem odkształcenia za pomocą konturografu
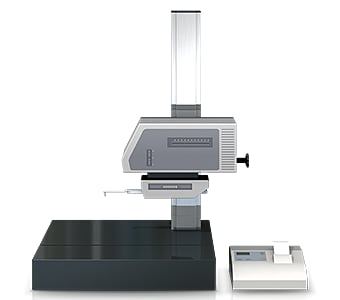
Konturograf mierzy i rejestruje profil obiektu przez śledzenie jego powierzchni za pomocą rysika. W ostatnich latach opracowano systemy pomiaru profilu wykorzystujące laser zamiast rysika, które umożliwiają pomiar złożonych kształtów przez bezkontaktowe śledzenie profilu. Niektóre modele są nawet w stanie wykonywać pomiar zarówno górnych, jak i dolnych powierzchni.
Niemniej jednak w przypadku systemu pomiaru profilu konieczne jest uzyskanie dokładnych linii pomiarowych dla punktów pomiarowych.
Wiąże się to z poniższymi problemami.
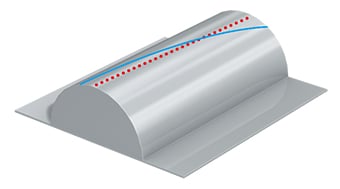
- Prace pomiarowe wymagają dużo czasu, w tym na przymocowanie próbki do jigu i wypoziomowanie. Wiedza i umiejętności związane z użytkowaniem systemów pomiaru profilu wymagane są również do dokładnego wypoziomowania obiektu.
- Rysik systemu pomiaru profilu porusza się w górę i w dół po łuku wyśrodkowanym na punkcie podparcia ramienia, a jego końcówka porusza się również po osi X. Powoduje to błąd w danych osi X.
- Śledzenie oczekiwanej linii za pomocą rysika jest niezwykle trudnym zadaniem, a nawet niewielkie przesunięcie rysika powoduje błąd w mierzonych wartościach.
- Trudno jest również zwiększyć liczbę obiektów docelowych ze względu na potrzebę wskazania konkretnych miejsc do pomiaru.
- Można zmierzyć tylko część obiektu, a ocena całej powierzchni jest niemożliwa.
Problemy z pomiarem odkształcenia za pomocą współrzędnościowej maszyny pomiarowej
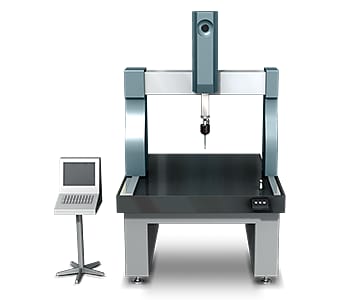
Standardowe współrzędnościowe maszyny pomiarowe wykorzystują sondę do skanowania lub śledzenia wzdłuż powierzchni, gromadząc wiele punktów danych przy określonym rozstawie.
Ta metoda pomiaru wiąże się z poniższymi problemami.
- Upewnienie się, że sonda porusza się zgodnie z przeznaczeniem stanowi niezwykle trudne zadanie, w szczególności w przypadku linii prostej w środku walca lub zakrzywionej powierzchni albo linii przechodzących przez środek okręgu. Jeśli zaokrąglenie wewnętrzne lub zewnętrzne ma szeroki kąt środkowy, ze względu na obliczanie całego okręgu na podstawie krótkiego łuku nawet niewielki błąd pomiaru zostanie znacznie powiększony. Takie odchylenia w punktach pomiarowych mogą powodować nieznaczne różnice w mierzonych wartościach.
- Podczas pomiaru kształtu 3D o małym rozmiarze sonda może nie być w stanie zetknąć się z pozycjami pomiarowymi. W związku z tym, że dokładność pomiaru jest proporcjonalna do liczby mierzonych punktów lub linii, konieczne jest zmierzenie dużej ich liczby.
Tak więc pomiar za pomocą współrzędnościowej maszyny pomiarowej wiąże się z istotnymi problemami, w tym z faktem, że nie wszyscy operatorzy w miejscu pracy mogą dokładnie mierzyć kształty, istnieniem części, których w ogóle nie można zmierzyć, a także z ograniczonymi miejscami, w których można zainstalować maszynę.
Rozwiązanie problemów z pomiarem odkształcenia po obróbce cieplnej
Podczas użytkowania tych przyrządów pomiarowych można napotkać trudności związane z pozycjonowaniem obiektu lub końcówki sondy oraz z uzyskaniem ogólnych danych pomiarowych powierzchni 3D, ponieważ wykonują one pomiary tylko z wykorzystaniem punktów lub linii. Aby rozwiązać te problemy, firma KEYENCE opracowała optyczny profilograf 3D ze sterowaniem jednym przyciskiem serii VR.
Urządzenie serii VR dokładnie rejestruje kształt 3D całej powierzchni docelowej w zaledwie sekundę bez kontaktu z obiektem. Umożliwia natychmiastową i dokładną kwantyfikację całej powierzchni 3D bez błędów pomiarowych. W tej sekcji przedstawiono kilka konkretnych zalet serii VR.
Korzyść nr 1: pomiar dużej liczby punktów w zaledwie sekundę.
Urządzenie serii VR pozyskuje dane powierzchniowe (800 000 punktów) trójwymiarowego kształtu obiektu w ciągu zaledwie sekundy, znacznie skracając czas wymagany do pomiaru dużej liczby punktów. Urządzenie dokładnie i natychmiastowo mierzy maksymalne i minimalne nierówności na całej powierzchni docelowej, umożliwiając szybką ocenę wszystkich miejsc na obiekcie z uwzględnieniem ustawionych tolerancji.
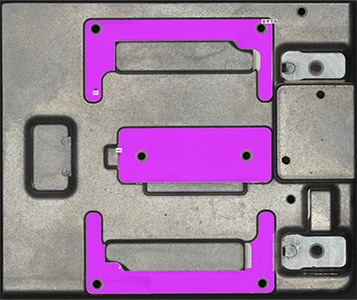
Po zeskanowaniu obrabianego przedmiotu jego profil (przekrój poprzeczny) może być również mierzony w miejscach innych niż użyte w poprzednim pomiarze. Eliminuje to konieczność ponownego ustawiania i mierzenia tego samego obiektu.
Korzyść 2: możliwość porównania danych pomiarowych z danymi referencyjnymi
Możliwości urządzenia serii VR wykraczają poza skuteczne gromadzenie danych. Dane pomiarowe mogą zostać wyświetlone na liście, a taką samą analizę zawartości można przeprowadzić dla wszystkich danych jednocześnie.
Istnieje możliwość szybkiego sprawdzenia różnic w danych pozyskanych przez pomiar wielu kształtów obiektów przed i po obróbce cieplnej, a także zakresu różnic między wadliwymi produktami i produktem referencyjnym. Umożliwia to analizę kwantyfikacyjną i ocenę odkształcenia spowodowanego przez obróbkę cieplną.
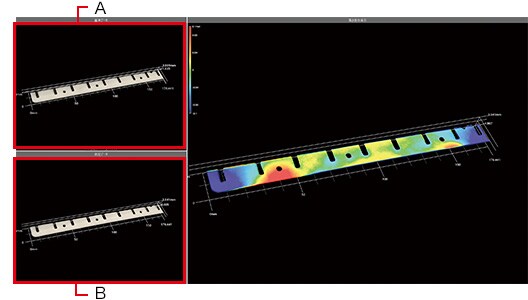
- A
- Dane referencyjne
- B
- Dane pomiarowe
Urządzenie serii VR może szybko mierzyć obiekty o złożonych kształtach, co wcześniej było czasochłonne i wymagało dużo pracy. Dane są nie tylko szybko rejestrowane, lecz wszystkie wyniki pomiarów są również digitalizowane, co znacznie ogranicza zakres pracy wymaganej do porównania i analizy danych.
Podsumowanie: znaczne usprawnienia pomiaru odkształcenia po obróbce cieplnej
Wcześniej pomiar odkształcenia spowodowanego przez obróbkę cieplną były czasochłonne, ograniczając liczbę próbek, które można było zmierzyć. W niektórych przypadkach pomiar był zupełnie niemożliwy ze względu na złożony kształt części. Urządzenie serii VR jest natomiast w stanie szybko mierzyć i kwantyfikować odkształcenie w przypadku takich kształtów. W rezultacie może ocenić jakość produktu z wyższą dokładnością i skutecznością.
- Znacznie ograniczenie ilości czasu poświęcanego na pomiar złożonych kształtów przez jednoczesne rejestrowanie wszystkich danych powierzchni.
- Poszczególne różnice w zakresie odkształcenia można łatwo zidentyfikować i przeanalizować przez rejestrowanie i porównywanie wielu zestawów danych pomiarowych.
- Możliwy jest prawdziwy pomiar ilościowy, co eliminuje zmienność wyników wynikającą z błędu człowieka.
- Aby zarejestrować dokładne dane, wystarczy umieścić obiekt na stoliku i kliknąć przycisk. Eliminuje to zapotrzebowanie na wykwalifikowanych operatorów, gdyż nie ma potrzeby przeprowadzania pozycjonowania ani innych prac przygotowawczych.
- Dokładny pomiar wielu obiektów w krótkim czasie dzięki skanowaniu o wysokiej szybkości.
Urządzenie serii VR umożliwia również porównywanie danych z poprzednimi skanami i modelami CAD oraz analizę chropowatości.