Pomiar zapadnięć
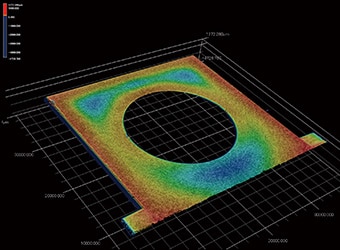
Zapadnięcia występują, gdy powierzchnia formowanego produktu kurczy się i tworzy niewielkie zagłębienia. Chociaż zapadnięcia nie wpływają na wytrzymałość lub funkcjonalność części, uważa się je za wadę jakościową. Istnieją również przypadki, w których występuje ubytek wewnątrz produktu. Jest on określany jako luka. Zarówno zapadnięcia, jak i luki powstają w wyniku nieprawidłowego kurczenia się podczas procesu chłodzenia i krzepnięcia stopionego tworzywa sztucznego.
Na tej stronie przedstawiono sposoby ograniczania i mierzenia zapadnięć za pomocą optycznego profilografu 3D ze sterowaniem jednym przyciskiem.
- Zapadnięcia
- Środki zaradcze w przypadku zapadnięć w projektowaniu form wtryskowych
- Pomiar zapadnięć
- Rozwiązanie problemów z pomiarem zapadnięć
- Podsumowanie
Zapadnięcia
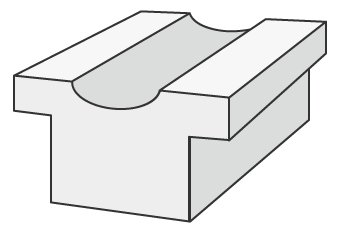
Zapadnięcia powstają głównie podczas procesu chłodzenia, gdy obszary gorącej ciekłej żywicy stygną i kurczą się w różnym tempie. Zapadnięcia najczęściej występują w grubszych sekcjach formowanych części, ponieważ takie sekcje zawierają więcej tworzywa, co wymaga dłuższego chłodzenia. Chociaż zależy to od okoliczności, zapadnięciom można zapobiec, gdy nie ma dużej różnicy w warunkach chłodzenia między wnętrzem a zewnętrzną częścią produktu. Poniżej przedstawiono 5 sposobów zapobiegania powstawaniu zapadnięć.
- Obniżenie temperatury materiału plastycznego.
- Obniżenie temperatury formy (lub zwiększenie temperatury, zależnie od okoliczności).
- Zmniejszenie różnic w grubości ścianek produktu (dodanie podcięć, aby produkt był cieńszy).
- Zwiększenie ciśnienia wtrysku.
- Zwiększenie ciśnienia i czasu docisku.
Należy pamiętać, że gdy sztywność powierzchni jest duża w porównaniu z siłą kurczenia, wewnątrz produktu mogą powstawać luki.
Środki zaradcze w przypadku zapadnięć w projektowaniu form wtryskowych
W poniższej sekcji przedstawiono trzy środki zaradcze w zakresie zapadnięć, które można zastosować na etapie projektowania formy.
Zmniejszenie grubości ścianek
Zasadniczo grubsze części stygną wolniej niż cieńsze. W takich częściach (zaznaczonych czerwonym kółkiem na poniższej ilustracji) istnieje większe prawdopodobieństwo wystąpienia zapadnięć. W tym przypadku możliwe jest wyeliminowanie zapadnięć przez zmianę grubości ścianki produktu formowanego z tworzywa sztucznego. Na przykład zmiana grubości B na ilustracji tak, aby była taka sama jak A (lub wynosiła 70% lub mniej) może zapobiec występowaniu zapadnięć.
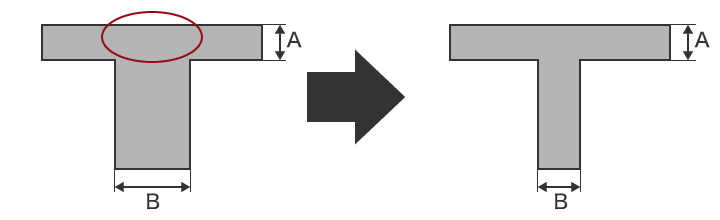
Zmiana kształtu w celu stopniowego zmniejszenia grubości ścianki
Jak wspomniano wcześniej, zapadnięciom można zapobiec przez zmniejszenie grubości. Jednak w niektórych przypadkach nie można zmienić grubości. Na przykład czasami nie można zmienić grubości, aby zachować wytrzymałość. W takich przypadkach warto zmienić kształt tak, aby grubość ścianki zmieniała się stopniowo. Na poniższym przykładzie można zobaczyć, w jaki sposób dodanie zaokrąglonych naroży skutkuje niewielkim zmniejszeniem grubości ścianki.
Oprócz zmiany kształtu można również dodać rurkę chłodzącą w miejscach, w których gromadzi się ciepło, lub użyć materiałów o wysokiej przewodności cieplnej.
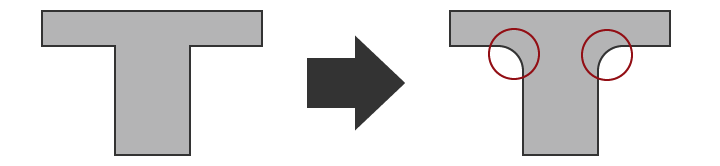
Dodanie podcięć i ożebrowania
Dodanie podcięć lub ożebrowania może pomóc w zmniejszeniu widoczności zapadnięć w przypadku złożonych części, które wymagają różnych poziomów grubości. Dodanie podcięć i przekrojów grubszych części w grubszych obszarach może pomóc obniżyć temperaturę, zapewniając bardziej równomierny proces chłodzenia. Ponadto dodanie poprzecznego wzoru ożebrowania wewnątrz podcięcia pozwala zapobiegać powstawaniu zapadnięć przy jednoczesnym zachowaniu wytrzymałości. Stopniowa zmiana grubości ścianki i fazowanie pomagają również skutecznie ograniczyć nagłe zmiany ciśnienia w formie.
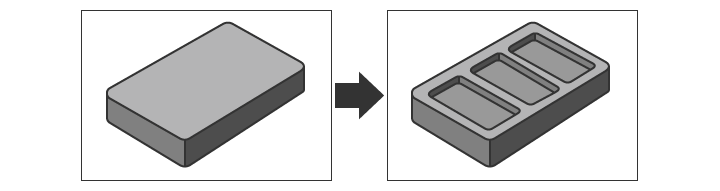
Pomiar zapadnięć
Zapadnięcia nie tylko są wadą kosmetyczną, ale też mogą mieć szkodliwy wpływ na integralność strukturalną elementu z tworzywa sztucznego, czyniąc go niezdatnym do użytku. Ważne jest, aby użyć odpowiedniego narzędzia pomiarowego do identyfikacji przyczyn wad, takich jak ciśnienie formowania, objętość wtryskiwanego materiału i temperatura. Konwencjonalne narzędzia pomiarowe, w tym wysokościomierze lub współrzędnościowe maszyny pomiarowe (CMM) są czasami trudne w użyciu, co skutkuje niedokładnymi pomiarami. Poniżej omówimy kilka problemów związanych z konwencjonalnymi systemami i przedstawimy nową technologię pomiarową, która może wyeliminować niektóre z tych problemów.
Problemy z pomiarem za pomocą wysokościomierza
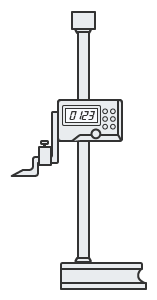
Wysokościomierz może być używany w połączeniu z czujnikiem zegarowym do pomiaru wysokości. Ponieważ pomiar jest ograniczony do punktów, nie można zidentyfikować całego kształtu, co uniemożliwia uzyskanie pełnego obrazu stanu ogólnego. Ponadto podczas pomiaru elastycznej części ciśnienie pomiarowe może spowodować wygięcie tej części, co skutkuje niedokładnymi pomiarami. Różnice w wynikach pomiarów między różnymi operatorami i błędy w samym przyrządzie pomiarowym również uniemożliwiają stabilny i dokładny pomiar.
Problemy z pomiarem za pomocą współrzędnościowej maszyny pomiarowej
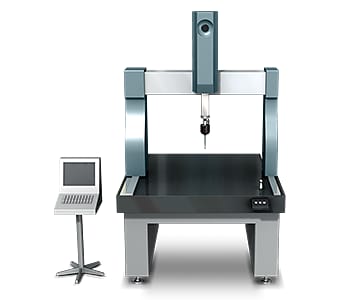
Podczas pomiaru niewielkiego zapadnięcia o wielkości 1 mm2 niezwykle trudno jest dokładnie zmierzyć kształt, celując w to miejsce sondą i tworząc wirtualną powierzchnię. Trudno jest również zidentyfikować dokładny kształt podczas pomiaru 3D małego obszaru ze względu na niewielką liczbę punktów pomiarowych. Pracochłonne są również powiązane zadania, takie jak tabelaryzacja danych pomiarowych i porównywanie wyników z rysunkami.
Rozwiązanie problemów z pomiarem zapadnięć
Do problemów związanych z zastosowaniem typowych przyrządów pomiarowych należy fakt, że pomiar trójwymiarowych obiektów i obszarów odbywa się za pomocą styku punktowego lub liniowego, oraz mała wiarygodność wartości pomiarowych. Aby rozwiązać te problemy pomiarowe, firma KEYENCE opracowała optyczny profilograf 3D ze sterowaniem jednym przyciskiem serii VR.
Urządzenie serii VR dokładnie rejestruje kształt 3D całej powierzchni docelowej bez kontaktu z obiektem. Mierzy również trójwymiarowy kształt obiektu umieszczonego na stoliku urządzenia przez skanowanie 3D wykonywane z wysoką dokładnością w ciągu zaledwie sekundy. Umożliwia natychmiastowy i ilościowy pomiar bez błędów w wynikach pomiaru. W tej sekcji przedstawiono kilka konkretnych zalet serii VR.
Korzyść nr 1: zbieranie danych z 800 000 punktów pomiarowych.
Seria VR może również mierzyć szeroki obszar o wymiarach do 300 mm × 150 mm, rejestrując jednocześnie do 800 000 punktów danych na skan. Ponieważ można zidentyfikować cały kształt oraz zmierzyć wysokie i niskie części, nawet niewielkie zapadnięcia można identyfikować równie łatwo jak duże. Wszystkie dane pomiarowe są zapisywane i mogą być porównywane z innymi danymi lub trójwymiarowymi danymi projektowymi.
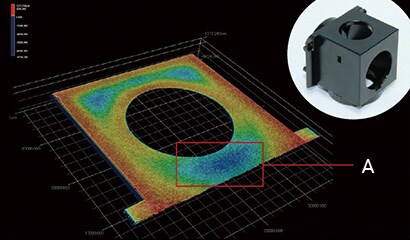
- A
- Niebieski obszar oznacza wklęsłość.
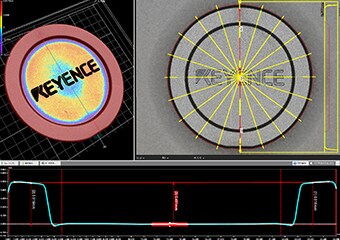
W przeciwieństwie do konwencjonalnych przyrządów pomiarowych seria VR jest w stanie z łatwością mierzyć zapadnięcia rozproszone na dużym obszarze. Ten rodzaj pomiaru wykonywany wcześniej za pomocą konwencjonalnych systemów był bardzo czaso- i pracochłonny. W zestawie znajdują się również narzędzia pomiarowe, które umożliwiają łatwe wykonywanie różnych pomiarów. Umożliwia to nawet początkującym użytkownikom wykonywanie dokładnych pomiarów, eliminując potrzebę przydzielania wyspecjalizowanego operatora do prac pomiarowych.
Korzyść nr 2: możliwość uzyskania danych wyjściowych w formatach Excel i CAD.
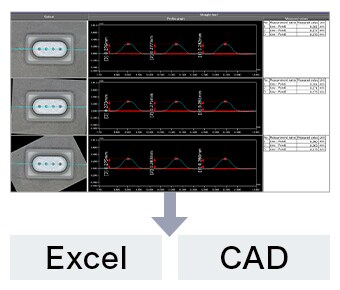
Dane mogą być przesyłane do programu Excel dokładnie w takiej postaci, w jakiej pojawiają się na ekranie. Takie funkcje jak możliwość sortowania każdej zmierzonej wartości lub ustawienia tabeli przestawnej do podsumowania danych umożliwiają płynne przeprowadzanie szczegółowych badań. Oprócz formatów STEP i ASCII obsługiwane są również dane wyjściowe CAD w formacie STL. Utworzone dane można wykorzystać na wiele sposobów.
Podsumowanie
Urządzenie serii VR umożliwia dokładny i natychmiastowy pomiar trójwymiarowych kształtów obiektu przez szybkie bezkontaktowe skanowanie 3D. Nawet trudne pomiary, takie jak wysokości i chropowatość zapadnięć, można wykonać w ciągu zaledwie sekundy. Seria VR rozwiązuje wszystkie problemy z konwencjonalnymi przyrządami pomiarowymi.
- Ponieważ mierzona jest cała powierzchnia, seria VR może z łatwością mierzyć zapadnięcia na dużym obszarze. Można również zmierzyć najwyższe i najniższe punkty.
- Eliminuje to zmienność wynikającą z czynnika ludzkiego, umożliwiając prawdziwy pomiar ilościowy.
- Pomiar można wykonać, po prostu umieszczając obiekt na stoliku urządzenia i naciskając przycisk. Nie ma potrzeby pozycjonowania ani wykonywania innych przygotowań. Eliminuje to konieczność przydzielania wyspecjalizowanego operatora do prac pomiarowych.
- Kształty 3D mogą być łatwo mierzone przy dużych prędkościach z wysoką dokładnością. Umożliwia to pomiar dużej liczby obiektów w krótkim czasie, pomagając poprawić jakość.
System ten umożliwia również porównywanie z wcześniejszymi danymi kształtu 3D i danymi CAD, a także zapewnia łatwą analizę danych, takich jak rozkład w granicach tolerancji. Może być skutecznie wykorzystywany do szerokiego zakresu celów, w tym rozwoju produktu, analizy trendów produkcyjnych i kontroli pobierania próbek.