Natychmiastowy i dokładny pomiar kształtów spoin lutowniczych
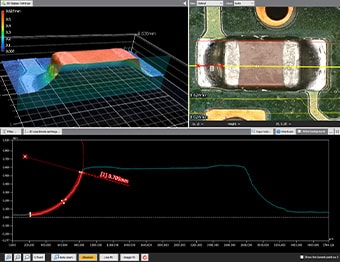
Wykorzystanie modułów telekomunikacji i sterowników elektronicznych w samochodach jest coraz większe. W wyniku rosnącej miniaturyzacji i zagęszczenia takich urządzeń jak smartfony, tablety, inteligentne zegarki i inne urządzenia ubieralne jakość montażu tych urządzeń i zapewnienie jakości są coraz bardziej zaawansowane, a ich znaczenie stale wzrasta.
Na tej stronie przedstawiono podstawowe informacje na temat spoin lutowniczych i procesów montażowych, które są ściśle związane z jakością montażu PCB. Przedstawiono również środki zaradcze w zakresie wad kształtu spoin i wad montażowych, problemy z pomiarem i oceną kształtu oraz rozwiązanie tych problemów.
- Spoiny lutownicze
- Technologia montażu powierzchniowego (SMT), kształt spoiny lutowniczej, wady montażowe i środki zaradcze
- Problemy z konwencjonalnym pomiarem kształtu spoin lutowniczych
- Rozwiązanie problemów z pomiarem kształtu spoin lutowniczych
- Podsumowanie
Spoiny lutownicze
Spoina lutownicza w montażu PCB dotyczy części, w której lut jest nakładany wokół komponentów montowanych na płytce drukowanej (PCB). Jakość lutowania jest oceniana na podstawie kształtu spoiny lutowniczej.
Prawidłowy kształt spoiny lutowniczej

- A
- Kąt: od 15° do 45°
- B
- Gładki, zakrzywiony wklęsły kształt z połyskiem (wypukły kształt jest nazywany zaciekiem lutowniczym i może powodować wady montażowe).
Ważne jest, aby sprawdzić i ocenić kształt stopionego i zestalonego lutowia (spoiny) w części, która łączy się z płytką. Kształt powinien być gładką wklęsłą krzywą, jak zbocza góry Fuji. Jak przedstawiono na poniższej ilustracji, mniejszy kąt kontaktu θ (większa zwilżalność) wskazuje na lepszy stan.
Jednak gdy ogrzewanie jest niewystarczające lub jest zbyt dużo lutu, zestala się on w wypukły kształt przypominający kroplę wody. Nazywa się to zaciekiem lutowniczym i może powodować zmniejszenie siły wiązania lub wadę połączenia.
Kąt kontaktu θ i zwilżalność
Zwilżalność jest wyrażana jako wartość kąta kontaktu θ między powierzchnią ciała stałego a cieczą (taką jak stopiony lut), która została na nią nałożona. Mniejszy kąt A na ilustracji (kąt kontaktu θ) oznacza większą zwilżalność i wskazuje, że ciecz została prawidłowo nałożona na powierzchnię ciała stałego. Większy kąt oznacza mniejszą zwilżalność, ponieważ powierzchnia ciała stałego odpycha ciecz.
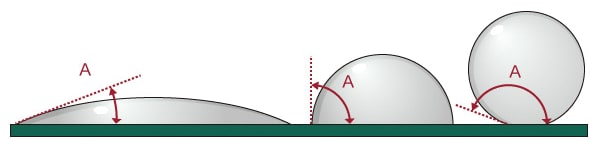
Technologia montażu powierzchniowego (SMT), kształt spoiny lutowniczej, wady montażowe i środki zaradcze
W tej sekcji wyjaśniono ogólny proces technologii montażu powierzchniowego (SMT), ilość lutu używanego do montażu powierzchniowego, kształt spoin i wady montażowe.
Przykład procesu montażu powierzchniowego (SMT)
Poniżej wymieniono ogólne procesy technologii montażu powierzchniowego (SMT) na potrzeby automatyki przemysłowej.
- • Proces nakładania pasty lutowniczej (kremu lutowniczego) w procesie drukowania
- Przy użyciu precyzyjnej metalowej maski (płytka lub maska sitowa) krem lutowniczy (pasta lutownicza) jest nakładany w procesie sitodruku za pomocą szpatułki, dzięki czemu pasta jest nakładana tylko w niezbędnych miejscach na PCB. Do prototypowania lub produkcji krótkoseryjnej można użyć drukarki atramentowej, która nie wymaga maski.
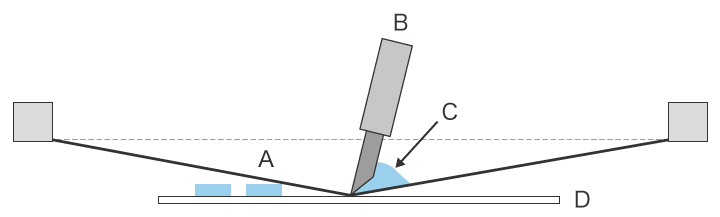
- A
- Metalowa maska
- B
- Szpatułka
- C
- Pasta lutownicza (krem lutowniczy)
- D
- Płytka drukowana
- • Proces łączenia układów scalonych
- W procesie tym wykorzystuje się łączenie (ang. bonding) do montażu komponentów układów scalonych na PCB. Jest ono głównie używane w procesie lutowania przepływowego do mocowania komponentów tak, aby nie odpadły podczas montażu. Zastosowanie klejów elektroprzewodzących umożliwia zamocowanie komponentów na miejscu, a także uzyskanie ciągłości.
- • Proces montażu układów scalonych
- Kaseta zawierająca elementy montażowe nawinięte na szpulę jest instalowana na głowicy mocującej. Głowica mocująca automatycznie umieszcza elementy montażowe w określonych pozycjach na dostarczonej płytce PCB zgodnie z programem.
- • Proces rozpływowy
- Po nałożeniu pasty lutowniczej lub spoiny układów scalonych i umieszczeniu elementów montażowych płytka PCB jest transportowana do pieca rozpływowego i podgrzewana. Proces ogrzewania topi pastę lutowniczą, która ulega zwilżeniu i rozprowadzeniu na zamontowanych komponentach i płytce montażowej PCB. Następnie odbywa się schładzanie i zestalanie, aby zakończyć lutowanie. Ogrzewanie jednocześnie utwardza łączenie układów scalonych w celu zamocowania klejonych elementów.
- Ponieważ temperatura topnienia lutu i temperatura utwardzania spoin układów scalonych są różne, temperatura nagrzewania i prędkość chłodzenia muszą być regulowane w ramach procesu. W procesie lutowania rozpływowego wymagana jest ostrożność ze względu na ryzyko zwichrowania płytki PCB w wyniku działania wysokiej temperatury.
Kształt spoiny lutowniczej, wady montażowe i środki zaradcze
W przypadku spoiny lutowniczej należy nałożyć odpowiednią ilość lutu w kształcie pokrywającym zacisk elektrody komponentu i płytkę montażową.
Na przykład podczas montażu powszechnie stosowanego wielowarstwowego kondensatora chipowego, gdy ilość lutu jest prawidłowa, spoina tworzy łagodnie zakrzywione do wewnątrz linie nachylenia na prawym i lewym zacisku elektrody. Gdy zostanie nałożona zbyt duża ilość lutu, tworzy się zaciek lutowniczy, jak wyjaśniono wcześniej. Gdy ilość lutu jest zbyt mała, nie jest możliwe utworzenie spoiny o wystarczającym kształcie i objętości. W obu przypadkach siła łączenia zostaje zmniejszona i mogą wystąpić wady montażowe lub wady połączenia.
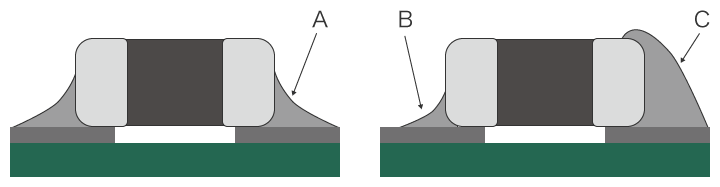
- A
- Prawidłowa ilość lutu i prawidłowy kształt spoiny (stany muszą być takie same na obu elektrodach).
- B
- Niewystarczająca ilość lutu i wada kształtu spoiny
- C
- Nadmierna ilość lutu i wada kształtu spoiny
Podczas procesu lutowania rozpływowego stopiony lut wytwarza napięcie powierzchniowe na zaciskach elektrod. W przypadku różnicy między ilością lutu na dwóch zaciskach lub gdy zmieni się temperatura nagrzewania, różnica w napięciu powierzchniowym występuje na dwóch zaciskach i powoduje problem znany jako „zjawisko Manhattanu”. Nazwa pochodzi od faktu, że komponent układu scalonego przypomina wysoki budynek. Jest również określany jako „zjawisko nagrobka”, ponieważ wyglądem przypomina nagrobek.
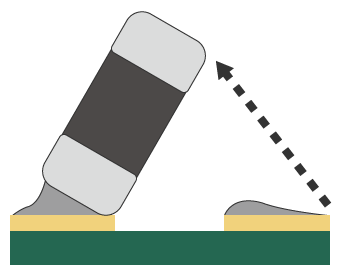
Podczas formułowania środków zaradczych, oprócz ilości i jakości lutu ważne jest, aby wziąć pod uwagę warunki procesu, w tym wstępne podgrzanie pieca rozpływowego i optymalizację profilu wzrostu temperatury.
Na poprzednim etapie projektowania PCB należy również wziąć pod uwagę takie czynniki jak kształt powierzchni i środki przeciwdziałające nagrzewaniu, które pozwolą na łatwe utworzenie prawidłowej spoiny. W niektórych przypadkach ulepszenie metalowej maski używanej podczas drukowania pastą lutowniczą (kremem lutowniczym) może pomóc zwiększyć dokładność lutowania.
Problemy z konwencjonalnym pomiarem kształtu spoin lutowniczych
Poniżej wyjaśniamy problemy z pomiarem i oceną spoin za pomocą konwencjonalnych systemów pomiaru profilu.
Problemy z pomiarem kształtu spoiny lutowniczej za pomocą kontaktowych systemów pomiaru profilu
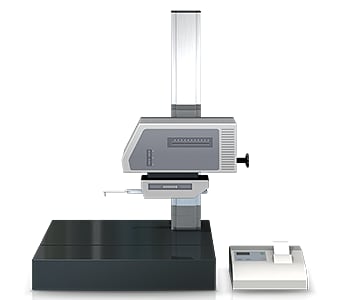
System pomiaru profilu mierzy i rejestruje profil obiektu przez śledzenie jego powierzchni za pomocą rysika.
Pozycjonowanie i poziomowanie oraz inne przygotowania próbki mają kluczowe znaczenie dla wydajności pomiaru, wymagając obecności wyspecjalizowanego operatora do wykonania wstępnej konfiguracji i prac pomiarowych. Wymaga to wiele czasu i pracy.
Ponieważ pomiar 3D jest wykonywany za pomocą linii, nie jest możliwe zidentyfikowanie całego kształtu, a pomiar spoin na płytce PCB o niewielkich rozmiarach i dużej gęstości może być trudny.
Rozwiązanie problemów z pomiarem kształtu spoin lutowniczych
Do tej pory wyjaśniliśmy kształt spoiny za pomocą figur dwuwymiarowych, jednak rzeczywista spoina ma kształt trójwymiarowy. Podczas montażu wsuwanego i montażu powierzchniowego mogą wystąpić różne wady kształtu spoiny.
Z tego powodu podczas pomiaru kształtu spoiny i sprawdzania jej wyglądu dokładna ocena spoiny jest możliwa tylko za pomocą precyzyjnego narzędzia pomiarowego, które może zmierzyć kształt 3D (w tym powierzchnię, wysokość, objętość i nachylenie). Ponieważ konwencjonalne narzędzia pomiarowe ograniczają się do linii pomiarowych, trudno jest dokładnie określić kształt spoiny.
Aby rozwiązać te problemy pomiarowe, firma KEYENCE opracowała optyczny profilograf 3D ze sterowaniem jednym przyciskiem serii VR. To narzędzie dokładnie rejestruje kształt 3D całej powierzchni obiektu bez kontaktu z nim.
W tym systemie nie jest wymagane pozycjonowanie obiektu. Użytkownicy mogą wykonywać dokładne i powtarzalne pomiary w ciągu zaledwie 1 sekundy, po prostu umieszczając próbkę na stoliku i klikając jeden przycisk. Pozwala to dokładnie zmierzyć profile 3D i kształty przekrojów 2D oraz umożliwia każdemu użytkownikowi szybkie i łatwe wykonywanie pomiarów ilościowych i oceny bez odchyleń w wynikach pomiarów. W tej sekcji przedstawiono kilka konkretnych zalet serii VR.
Korzyść nr 1: możliwość uchwycenia kształtu 3D całej powierzchni w zaledwie sekundę.
Ponieważ miernik spoiny mierzy warunki dopasowania kształtu na linii, a system pomiaru profilu mierzy powierzchnię spoiny przez kontakt rysika pomiarowego na linii, trudno jest dokładnie zmierzyć cały kształt spoiny.
Dzięki profilografowi serii VR użytkownik może zeskanować kształt powierzchni 3D obiektu w celu natychmiastowego wykonania bezkontaktowego pomiaru w ciągu zaledwie sekundy.
Ponieważ możliwe jest przełączanie między małym i dużym powiększeniem, można wykonać bardzo dokładny pomiar nie tylko całej płytki montażowej PCB, ale także szczegółowego kształtu spoiny lutowniczej na określonych komponentach.
Kolorowa mapa wysokości umożliwia wizualizację kształtu spoiny lub komponentu elektronicznego, pozwalając na szybką identyfikację nieprawidłowych lokalizacji i ich szczegółowych wartości.
Po zeskanowaniu elementu dane pomiarowe są zapisywane, a pomiar profilu przekroju na dowolnej linii można wykonać w dowolnym momencie przy użyciu wcześniejszych danych. Dane te mogą być łatwo udostępniane, umożliwiając sprawne wykonywanie takich zadań jak identyfikacja przyczyny wady, formułowanie środków zaradczych w celu zapobiegania ponownemu wystąpieniu usterki oraz przeprowadzanie porównań i analizy trendów.
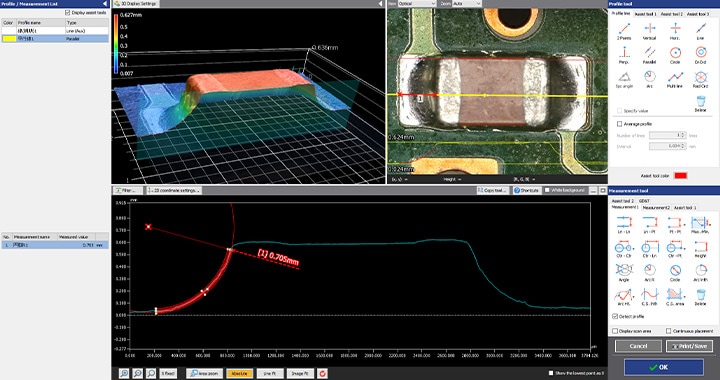
Korzyść nr 2: kształty spoin można mierzyć natychmiastowo, bez konieczności wcześniejszego ustawiania lub pozycjonowania.
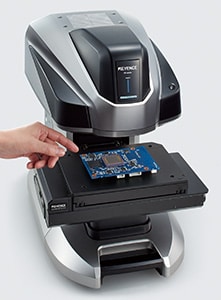
Profilograf serii VR pozwala na natychmiastowe rozpoczęcie pomiaru, eliminując konieczność mocowania obiektu do jigu, wykonywania ścisłego pozycjonowania czy innych trudnych wstępnych ustawień lub obsługi systemu pomiarowego.
Pomiar kształtu 3D można łatwo wykonać, po prostu umieszczając obiekt na stoliku pomiarowym i naciskając przycisk. W związku z tym, że automatyczna regulacja pozycji jest możliwa w oparciu o charakterystyczne dane obiektu, nie jest wymagane ścisłe pozycjonowanie. Umożliwia to pomiar ilościowy bez zmienności spowodowanej czynnikami ludzkimi. Każdy użytkownik, niezależnie od poziomu doświadczenia, może wykonywać dokładne i powtarzalne pomiary, zwiększając liczbę próbek, które można zmierzyć w danym czasie.
Ponadto profilografy tej serii są wyposażone w pierwszą w branży funkcję inteligentnego pomiaru, która automatycznie konfiguruje zakres pomiarowy i przesuwa stolik. Eliminuje to konieczność ustawiania długości pomiaru, zakresu Z i innych zaawansowanych ustawień.
Podsumowanie
Oprócz kształtów spoin lutowniczych profilograf serii VR może natychmiastowo i dokładnie zmierzyć pełną powierzchnię 3D próbki, umożliwiając użytkownikom wizualizację warunków montażu na całej płytce PCB za pomocą bezkontaktowego, szybkiego skanowania 3D.
- Pomiar można wykonać w ciągu zaledwie sekundy. Spoinę lutowniczą (wysokość) powierzchni można zidentyfikować na mapie kolorów, a szczegółowe dane można uzyskać poprzez pomiar profilu żądanego przekroju.
- Przełączając powiększenie, możliwy jest bardzo dokładny i bezkontaktowy pomiar całego kształtu lub szczegółowych części małych i delikatnych zamontowanych elementów.
- Nie jest wymagane pozycjonowanie. Nie są wymagane doświadczenie ani wiedza. Aby wykonać pomiar, wystarczy umieścić obiekt na stoliku urządzenia i nacisnąć przycisk.
- Obiekt może być przedstawiany w dowolny sposób przy użyciu kombinacji obrazu mapy kolorów kształtu 3D, obrazu obiektu i danych profilu. Możliwość udostępniania danych, które są wizualnie łatwe do zrozumienia, pozwala na płynną koordynację pracy i podejmowanie działań zaradczych w poszczególnych procesach.
- W krótkim czasie można wykonać pomiary większej liczby próbek. Możliwe jest również łatwe przeprowadzanie porównań i analiz ilościowych wielu zestawów danych pomiarowych.
Pozwala to na równoległe porównywanie wielu zestawów danych pomiarowych i przeprowadzanie analizy danych poprzez jednoczesne zastosowanie ustawień do wszystkich zestawów danych. Udostępniając dane kształtu 3D uzyskane za pomocą profilografu serii VR, można znacznie skrócić wymagany czas i poprawić wydajność całego procesu, począwszy od pomiaru, analizy wad i środków zaradczych zapobiegających powstawaniu wad.