Metoda pomiaru kształtu odkształcenia
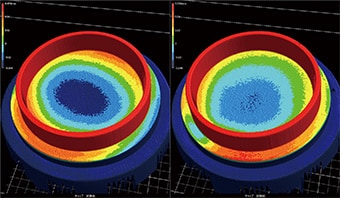
Rozciąganie, ściskanie, skręcanie i inne siły działające na próbkę są wyrażane za pomocą różnych pojęć. Stosunek deformacji generowanej przez przyłożenie tych sił jest określany jako „odkształcenie”. Istnieją trzy rodzaje odkształceń, sklasyfikowane zgodnie z kierunkiem i położeniem przyłożonej siły (obciążenia). Wynikające z tego odkształcenia obejmują wypaczenie, falistość, wydłużenie, ściśnięcie, rozszerzenie i skręcenie.
Przedstawimy zasady trzech rodzajów odkształceń, a także metody pomiaru deformacji spowodowanych odkształceniem. Opiszemy również problemy z konwencjonalnymi metodami pomiarowymi oraz przedstawimy rozwiązanie tych problemów.
- Odkształcenie
- Pomiar odkształceń za pomocą tensometru
- Problemy z konwencjonalnym pomiarem kształtu odkształcenia
- Rozwiązanie problemów z pomiarem kształtu odkształceń
- Podsumowanie: znaczna poprawa i większa wydajność w przypadku pomiaru trudniejszych odkształceń
Odkształcenie
Gdy obiekt jest ciągnięty, dociskany lub poddawany działaniu innej siły, odkształca się. Na przykład gdy obiekt jest ciągnięty, wydłuża się w kierunku, w którym jest ciągnięty. Gdy obiekt jest ściskany, ściska się w kierunku ściskania. Stosunek zdeformowanego kształtu do kształtu pierwotnego jest określany jako „odkształcenie”. Odkształcenie obejmuje odkształcenie wzdłużne, odkształcenie boczne i odkształcenie poprzeczne, każde z innym kierunkiem obciążenia.
Odkształcenie wzdłużne i poprzeczne
Odkształcenie wzdłużne to odkształcenie w kierunku obciążenia (ściskania) występujące, gdy obiekt jest ściskany. Odkształcenie poprzeczne to odkształcenie (rozszerzanie) w kierunku prostopadłym do obciążenia obiektu.
Odkształcenie występuje również, gdy obiekt jest ciągnięty. W tym przypadku odkształcenie wzdłużne to odkształcenie (wydłużanie) w kierunku przyłożonego obciążenia (rozciąganie). Odkształcenie poprzeczne to odkształcenie (skurczenie) w kierunku prostopadłym do obciążenia obiektu. Stosunek między odkształceniem wzdłużnym a odkształceniem poprzecznym jest nazywany „współczynnikiem Poissona”.
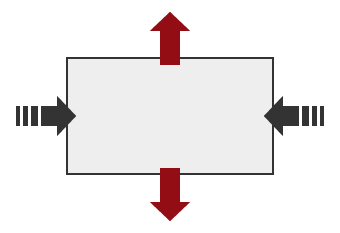
- Ściskanie
- Rozszerzanie
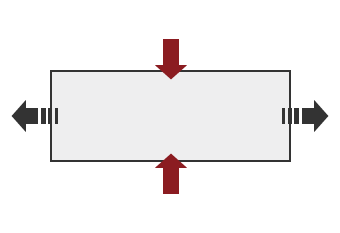
- Rozciąganie
- Kurczenie
Odkształcenie ścinające
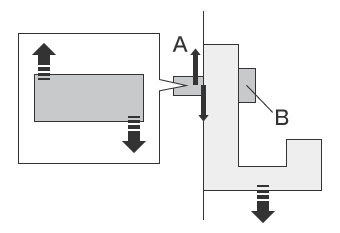
- A
- Siła ścinająca
- B
- Hak
Jest to odkształcenie, które występuje, gdy obiekt jest poddawany działaniu siły ścinającej. Można to łatwo zrozumieć, wyobrażając sobie siłę nożyczek tnących papier lub haka służącego do zawieszania obrazu na ścianie.
Skręcanie
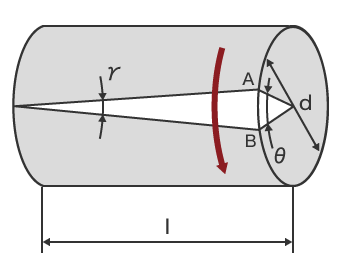
- θ
- Kąt skręcania:
- γ
- Odkształcenie ścinające
- l
- Długość osi
- d
- Średnica
- AB
- Maksymalna siła skręcania
Siła ścinająca jest generowana, gdy oś jest skręcana. W tym samym czasie siła rozciągająca i siła ściskająca równe sile ścinającej są generowane w dwóch kierunkach nachylonych pod kątem 45° względem osi. W rezultacie odkształcenie spowodowane skręcaniem nie jest pojedynczym odkształceniem, ale raczej połączonym odkształceniem składającym się z odkształcenia ścinającego, odkształcenia wzdłużnego i odkształcenia poprzecznego.
Pomiar odkształceń za pomocą tensometru
Tensometr mierzy wielkość odkształcenia, wykorzystując zmianę oporności wynikającą z rozszerzania i kurczenia się sprawdzianu. Przykładając sprawdzian do miejsca, w którym występuje odkształcenie, i mierząc wartości oporności przed odkształceniem i podczas odkształcania, można zidentyfikować proces odkształcania. Poniższe wyrażenie przedstawia zależność między pierwotną wartością oporności, wielkością zmiany oporności i wielkością odkształcenia.
⊿R / R = K × ε
- ⊿R
- Wielkość zmiany oporności (Ω)
- R
- Pierwotna wartość oporności (Ω)
- K
- Stała proporcjonalności*
- ε
- Wielkość odkształcenia
* Współczynnik K to „współczynnik sprawdzianu” będący stałą proporcjonalności, która jest określana na podstawie metalowego materiału użytego w tensometrze.
Tensometr jest przeznaczony do pomiaru wielkości odkształcenia w obiekcie i służy do pomiaru kształtu. Kształt odkształcenia jest mierzony za pomocą takich przyrządów jak konturograf wysokościomierz lub współrzędnościowa maszyna pomiarowa.
Problemy z konwencjonalnym pomiarem kształtu odkształcenia
Odkształcenie powstaje w wyniku złożonej deformacji niezależnie od kierunku obciążenia. Obiekt poddawany odkształceniom ma trójwymiarowy kształt, który jest konwencjonalnie mierzony za pomocą konturografu lub wysokościomierza. Pomiar za pomocą systemu pomiaru profilu lub wysokościomierza wiąże się jednak z następującymi problemami:
Problemy z pomiarem kształtu odkształcenia za pomocą konturografu
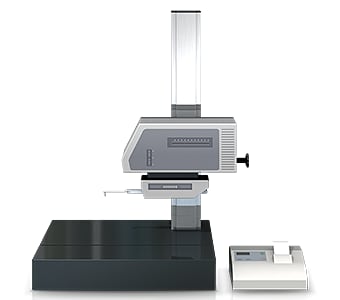
Mierzy i rejestruje profil obiektu przez śledzenie jego powierzchni za pomocą rysika. W ostatnich latach opracowano systemy pomiaru profilu wykorzystujące laser zamiast rysika, które umożliwiają pomiar złożonych kształtów przez bezkontaktowe śledzenie profilu. Niektóre modele są nawet w stanie wykonywać pomiar zarówno górnych, jak i dolnych powierzchni.
Podczas pomiaru trójwymiarowego obiektu przez system pomiaru profilu obiekt musi być wypoziomowany.
W przypadku tej metody pomiaru mogą wystąpić następujące problemy:
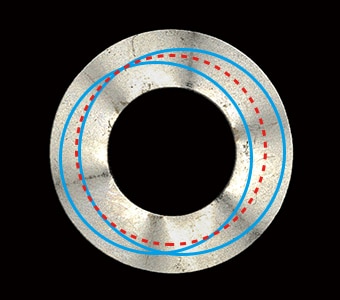
- Pomiar i mocowanie są czasochłonne. Wiedza i umiejętności związane z użytkowaniem konturografu wymagane są również do dokładnego wypoziomowania obiektu.
- Rysik systemu pomiaru profilu porusza się w górę i w dół po łuku wyśrodkowanym na punkcie podparcia ramienia, a jego końcówka porusza się również po osi X. Powoduje to błąd w danych osi X.
- Śledzenie oczekiwanej linii za pomocą rysika jest niezwykle trudnym zadaniem, a nawet niewielkie przesunięcie rysika powoduje błąd w mierzonych wartościach.
- Ponieważ można ocenić tylko linie, nie można zwizualizować odkształcenia na całej powierzchni.
Problemy z pomiarem kształtu odkształcenia za pomocą wysokościomierza
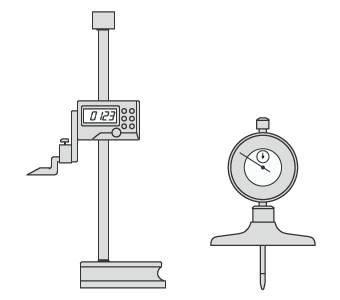
- Po lewej stronie
- Wysokościomierz
- Po prawej stronie
- Głębokościomierz
Wysokościomierz może być używany w połączeniu z czujnikiem zegarowym do pomiaru wysokości.
- Ponieważ możliwe jest sprawdzenie tylko pojedynczych punktów, konieczne jest wykonanie pomiarów w wielu różnych obszarach w celu zwiększenia dokładności. Jednak nawet po poświęceniu dużej ilości czasu i zmierzeniu wielu punktów nadal niemożliwe jest określenie warunków całej powierzchni.
- Gdy element jest mały lub ma złożony kształt, wykonanie pomiaru styku w bardzo małych elementach o wąskim przekroju może być trudne. Różnice w wynikach pomiarów między różnymi operatorami i błędy w samym przyrządzie pomiarowym również uniemożliwiają stabilny i dokładny pomiar.
Rozwiązanie problemów z pomiarem kształtu odkształceń
Przyrządy pomiarowe, które są zwykle używane, wiążą się z takimi problemami jak długi czas wymagany do pozycjonowania obiektu oraz fakt, że pomiar trójwymiarowych obiektów i obszarów odbywa się za pomocą styku punktowego lub liniowego. Aby rozwiązać te problemy pomiarowe, firma KEYENCE opracowała optyczny profilograf 3D ze sterowaniem jednym przyciskiem serii VR.
Urządzenie serii VR dokładnie rejestruje kształt 3D całej powierzchni docelowej bez kontaktu z obiektem. Mierzy również trójwymiarowy kształt obiektu umieszczonego na stoliku urządzenia przez skanowanie 3D wykonywane z wysoką dokładnością w ciągu zaledwie sekundy. Umożliwia natychmiastowy i ilościowy pomiar bez błędów w wynikach pomiaru. W tej sekcji przedstawiono kilka konkretnych zalet serii VR.
Korzyść nr 1: rejestrowanie całej powierzchni kształtu. Natychmiastowa wizualizacja odkształceń w szczegółowych elementach.
Firma KEYENCE dokonała pełnego przeglądu algorytmów pomiarowych i sprzętu, uzyskując pomiar na szerokim obszarze wynoszącym do 300mm x 150mm w ciągu zaledwie jednej sekundy. Umożliwia to swobodny pomiar punktu docelowego, w tym zlokalizowanego kształtu i odkształcenia, a także pomiar falistości i chropowatości w tym samym czasie, co pomiar odkształcenia. Ponadto wyniki pomiarów nie różnią się w zależności od operatora.
Dzięki imponującej szybkości pomiaru wynoszącej zaledwie sekundę seria VR umożliwia znaczne zwiększenie liczby mierzonych próbek i skrócenie czasu pracy. Prowadzi to do poprawy jakości pomiarów, pozwala na zmianę operatorów kontroli na operatorów produkcji i pomaga zwiększyć wielkość produkcji. Profilografy serii VR zwiększają również szybkość wszystkich zadań pomiarowych, takich jak ocena prototypów i kontrole dostaw.
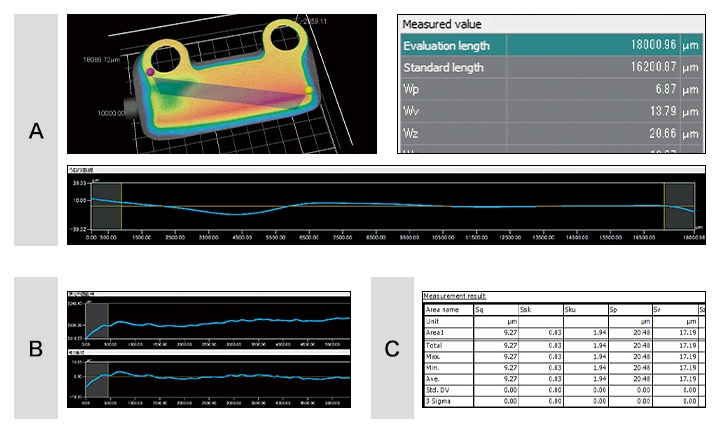
- A
- Pomiar falistości i odkształcenia
- B
- Pomiar profilu chropowatości
- C
- Pomiar chropowatości powierzchni
W przeciwieństwie do systemów pomiaru profilu lub wysokościomierzy profilograf serii VR wyodrębnia charakterystykę obiektu na stoliku i automatycznie koryguje jego położenie. Nie jest już konieczne ścisłe pozycjonowanie, co wcześniej było czasochłonne i wymagało wiele wysiłku. Dzięki temu nawet operator, który nie jest zaznajomiony z pomiarem, może go wykonać w łatwy i natychmiastowy sposób. Eliminuje to konieczność przydzielania wyspecjalizowanego operatora do prac pomiarowych.
Korzystając z profilografów serii VR, można dokładnie zmierzyć równoległość obiektów nawet o złożonym kształcie — wystarczy umieścić obiekt na stoliku urządzenia i nacisnąć przycisk.
Korzyść nr 2: wizualna identyfikacja zmian odkształcenia.
Nieoczekiwane deformacje elementów mogą wystąpić z powodu naprężeń mechanicznych, w tym przypadków odkształceń skrętnych, w których zmiany kształtu są złożone, a pomiar jest utrudniony. Gdy takie obiekty są mierzone za pomocą linii lub punktów, nie tylko nie można uzyskać dokładnych danych o kształcie, ale także trudna jest identyfikacja samego kształtu.
W przypadku profilografów serii VR wystarczy zeskanować obiekt, umieszczając go najpierw na stoliku. Nie jest wymagane pozycjonowanie obiektu, aby zarejestrować jego kształt 3D.
Ponieważ wysokość obiektu może być wyświetlana w kolorach, a pomiar profilu jest możliwy w dowolnej części obiektu, możliwa jest wizualizacja i identyfikacja lokalizacji oraz dokładnych wartości liczbowych wad kształtu. Umożliwia to sprawną identyfikację i korygowanie przyczyn wad spowodowanych przez formy, matryce i warunki formowania.
Ponieważ dane kształtu są mierzone ilościowo, możliwe jest łatwe zarządzanie odkształceniami w oparciu o tolerancje numeryczne lub wykorzystanie pomiarów do analizy trendów.
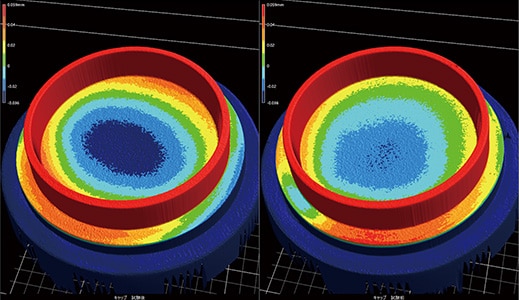
Podsumowanie: znaczna poprawa i większa wydajność w przypadku pomiaru trudniejszych odkształceń
Profilograf serii VR umożliwia dokładny i natychmiastowy pomiar odkształcenia i innych kształtów trójwymiarowego obiektu przez szybkie i bezkontaktowe skanowanie 3D.
- Ponieważ mierzona jest cała powierzchnia, możliwe jest zidentyfikowanie wszystkich miejsc odkształceń na obiekcie oraz wykonanie pomiaru profilu w dowolnej żądanej części.
- Nie jest wymagane pozycjonowanie. Aby wykonać pomiar, wystarczy umieścić obiekt na stoliku urządzenia i nacisnąć przycisk.
- Kształty 3D mogą być łatwo mierzone przy dużych prędkościach z wysoką dokładnością. Umożliwia to pomiar dużej liczby obiektów w krótkim czasie.
- Można łatwo i ilościowo porównywać i analizować wiele zestawów danych pomiarowych.
Ponadto ustawienie tolerancji dla płaskości umożliwia łatwe ocenianie produktów prawidłowych/nieprawidłowych oraz analizowanie produktów nieprawidłowych na podstawie danych. Umożliwia to pomiar odkształceń i wizualizację elementów drobnych lub o złożonych kształtach, których nie można zmierzyć konwencjonalnymi metodami. Profilograf serii VR zapewnia szybki i dokładny pomiar oraz bezproblemową analizę danych przy radykalnej poprawie wydajności pracy.