Techniki pomiaru deformacji i falistości w celu uzyskania lepszych wyników
- Metale
- Urządzenia elektroniczne
- Tworzywa sztuczne
- Tłoczenie
- Formowanie tworzyw sztucznych
- Płytki drukowane
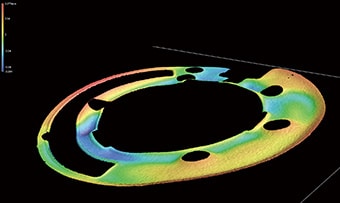
Przyrządy metrologiczne używane do pomiaru deformacji i falistości powierzchni obejmują czujniki zegarowe, profilometry powierzchni i współrzędnościowe maszyny pomiarowe (CMM). Ponieważ wypaczenie i falistość są cechami trójwymiarowymi, mogą być trudne do dokładnego zmierzenia za pomocą konwencjonalnych metod pomiarowych, które po prostu mierzą punkty i linie.
W zależności od kształtu lub rozmiaru elementu istnieje wiele sytuacji, w których konwencjonalne metody nie są w stanie dokładnie zmierzyć wypaczenia i falistości lub w ogóle nie pozwalają na ich fizyczny pomiar.
Wyjaśnimy tutaj podstawy falistości, wypaczenia i różne powszechnie stosowane metody pomiaru. Omówimy również problemy z konwencjonalnymi metodami pomiaru falistości oraz najnowsze rozwiązania w tym zakresie.
- Falistość i deformacja
- Równoległość i płaskość
- Znaczenie pomiaru wypaczenia/falistości i typowe problemy
- Rozwiązania typowych problemów dotyczących pomiaru wypaczenia i falistości
- Podsumowanie: znaczna poprawa i wyższa wydajność pomiarów wypaczenia/falistości
Falistość i deformacja
Falistość/wypaczenie to termin opisujący zjawisko skręcania i wyginania części. Ogólnie falistość/wypaczenie części odnosi się do stopniowo falującego kształtu na jej powierzchni.
Chociaż poniższa ilustracja przedstawia skrajny przykład, cała powierzchnia próbki może podlegać kombinacji skręcania i zginania (w górę i w dół) w środku lub na krawędziach części. W przypadkach, w których wymagana jest dokładność płaskości rzędu mikronów, ocena wizualna jest niemożliwa do przeprowadzenia.
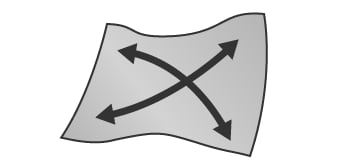
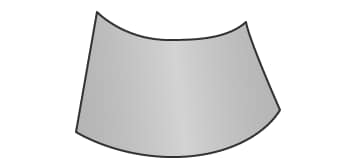
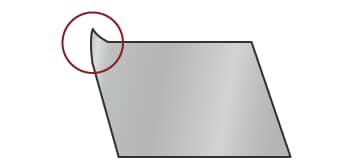
- A
- Skręcenie
- B
- Zginanie (w górę i w dół)
- C
- Wypaczenie krawędzi
Jedynym sposobem na skuteczną ocenę deformacji i falistości jest zmierzenie, czy falistość na całej powierzchni obiektu przekracza tolerancje płaskości i równoległości dla danej próbki. Płaskość i równoległość zostały szczegółowo wyjaśnione poniżej. Pomiar niewielkich falistości na całej powierzchni może być bardzo skomplikowany i powodować pewne trudności. W dalszej części przedstawimy metody pomiaru wypaczenia i falistości oraz typowe problemy, z którymi spotykają się operatorzy próbujący wykonać te pomiary, a także rozwiązania tych problemów.
Równoległość i płaskość
Wypaczenia/falistości składające się ze złożonych pofalowań można zdefiniować za pomocą pomiaru GD&T. Wielkość ta jest zazwyczaj definiowana przez tolerancję kształtu płaskości lub tolerancję orientacji równoległości. Równoległość, choć podobna pod pewnymi względami, w przeciwieństwie do płaskości wymaga punktu odniesienia (płaszczyzny lub linii odniesienia).
Płaskość
Płaskość jest definiowana jako odchylenie między idealnie płaską powierzchnią a płaszczyzną pomiaru. Poniżej przedstawiono przykład sprawdzenia parametru płaskości na rysunku technicznym.
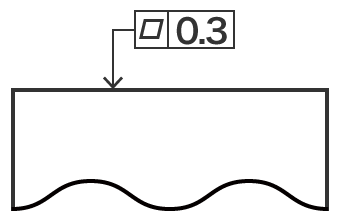
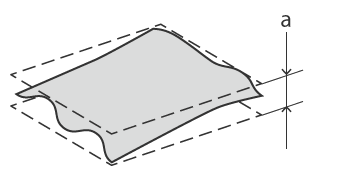
- a
- Odchylenie 0,3 mm lub mniej
Płaskość można obliczyć przez rzutowanie dwóch idealnie płaskich oraz równoległych płaszczyzn powyżej i poniżej powierzchni zainteresowania. Pierwsza rzutowana płaszczyzna może być umieszczona w najwyższym punkcie powierzchni pomiaru. Druga rzutowana płaszczyzna może być następnie umieszczona w najniższym punkcie powierzchni pomiaru. Prostopadła odległość między dwiema rzutowanymi płaszczyznami byłaby wówczas wynikowym pomiarem płaskości. Dlatego też, gdy tolerancja określa, jak płaska powinna być powierzchnia obiektu, odległość między rzutowaną płaszczyzną najwyższego punktu a rzutowaną płaszczyzną najniższego punktu musi być mniejsza niż wartość sprawdzenia płaskości, aby przejść kontrolę tolerancji. Na tej ilustracji zdefiniowana tolerancja to odległość 0,3 mm lub mniejsza.
Równoległość
Równoległość to parametr pomiaru GD&T, który mierzy stopień równoległości dwóch linii lub płaszczyzn względem siebie.
Główna różnica między płaskością a równoległością polega na tym, że równoległość wymaga punktu odniesienia (płaszczyzny lub linii odniesienia).
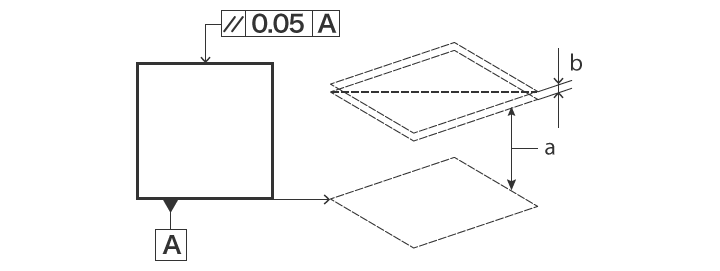
- a
- Rzut równoległy
- b
- Odchylenie 0,05 mm lub mniej
Płaszczyzna wskazana strzałką na ilustracji musi być równoległa do płaszczyzny odniesienia A (płaszczyzny, która jest zdefiniowana jako płaska, nawet jeśli na rzeczywistym obiekcie występuje wypaczenie/falistość) i musi znajdować się między dwiema rzutowanymi płaszczyznami oddalonymi od siebie o nie więcej niż 0,05 mm w kierunku wspomnianej strzałki.
W przypadku cienkich obiektów, takich jak arkusze blachy, arkusze z tworzywa sztucznego, folie, płytki PCB i szkło ochronne smartfonów, różnice w grubości mogą powodować wypaczenia/falistość i wpływać na równoległość.
Znaczenie pomiaru wypaczenia/falistości i typowe problemy
W wielu przypadkach falistość powstaje w wyniku działania wysokiej temperatury, naprężeń szczątkowych lub innych naprężeń podczas produkcji. Następujące procesy i naprężenia są typowymi przyczynami krzywizny.
- Tłoczenie (naprężenia szczątkowe spowodowane wykrawaniem lub tłoczeniem)
- Warunki podczas formowania wtryskowego tworzyw sztucznych (temperatura i ciśnienie stopionego tworzywa sztucznego oraz formy)
- Montaż komponentów na płytkach PCB (podgrzewanie podczas procesu rozpływowego)
W przypadku arkuszy o nierównej grubości temperatura przechowywania może powodować wypaczenia/falistość z powodu różnic szybkości rozszerzalności cieplnej.
Takie wypaczenie/falistość jest wadą kształtu, która będzie miała wpływ na proces produkcji i wydajność. Gdy na płytkach PCB występuje wypaczenie/falistość, może to powodować wady styków, takie jak unoszenie wyprowadzeń zamontowanych elementów elektronicznych. Aby zachować stabilność, ważne jest prawidłowe zmierzenie krzywizny materiału przed formowaniem i po nim.
Do pomiaru wypaczenia/falistości tradycyjnie stosuje się różne metody pomiarowe, w tym opisane poniżej.
- Mocowanie wysokościomierza do ramienia i odczytywanie zmieniających się pomiarów wysokości podczas śledzenia wysokościomierza wzdłuż powierzchni obiektu
- Użycie szklanego wzorca z płaską powierzchnią i umieszczenie płytki optycznej w kontakcie z powierzchnią pomiarową w celu zmierzenia liczby powstałych prążków (optyczny prążek interferencyjny: pierścienie Newtona).
- Pomiar za pomocą systemu pomiaru profilu lub współrzędnościowej maszyny pomiarowej
Pomiar wypaczenia/falistości za pomocą tych konwencjonalnych kontaktowych przyrządów pomiarowych może mieć pewne wady.
Typowe problemy dotyczące pomiaru wypaczenia i falistości za pomocą systemów pomiaru profilu
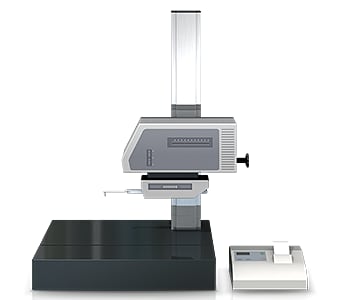
System pomiaru profilu mierzy i rejestruje profil obiektu przez śledzenie jego powierzchni za pomocą sondy nazywanej rysikiem.
W ostatnich latach opracowano systemy pomiaru profilu wykorzystujące laser zamiast rysika, które umożliwiają pomiar skomplikowanych kształtów przez bezkontaktowe śledzenie profilu. Niektóre modele są nawet w stanie wykonywać pomiar zarówno górnych, jak i dolnych powierzchni.
Podczas pomiaru wypaczenia/falistości za pomocą systemu pomiaru profilu zazwyczaj można napotkać opisane poniżej wyzwania.
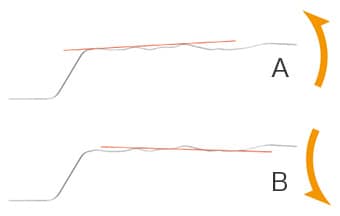
- A
- Nachylenie do góry
- B
- Nachylenie w dół
- Ponieważ obiekt jest mierzony przez śledzenie wzdłuż linii, trudno jest zidentyfikować trójwymiarową charakterystykę wypaczenia/falistości.
- Nie jest możliwe określenie warunków na całej powierzchni obiektu.
- Gdy na mierzonej powierzchni występują nieregularności (montażu układów scalonych), tak jak na PCB po zamontowaniu komponentów, trudno jest wykryć, czy na samej płytce PCB występuje wypaczenie lub falistość.
- Ustawienie płaszczyzny odniesienia za pomocą pojedynczych linii sprawia trudności i może skutkować błędem pomiaru (patrz ilustracja).
Typowe problemy dotyczące pomiaru wypaczenia i falistości za pomocą współrzędnościowych maszyn pomiarowych
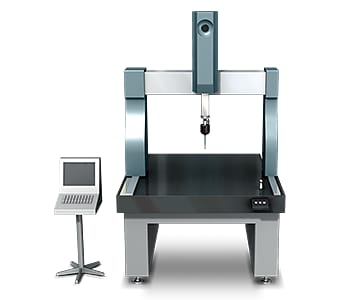
Zasadniczo podczas pomiaru wypaczenia lub falistości za pomocą współrzędnościowej maszyny pomiarowej sonda będzie stykać się z co najmniej czterema narożnikami na mierzonej powierzchni obiektu.
Na przykład w przypadku płyty zazwyczaj rejestrowanych jest od sześciu do ośmiu punktów. Gdy obszar pomiarowy jest duży, można zwiększyć dokładność pomiaru przez zwiększenie liczby punktów danych w celu zebrania większej ilości danych pomiarowych.
Podczas przeprowadzania pomiarów wypaczeń i falistości można jednak napotkać poniższe problemy.
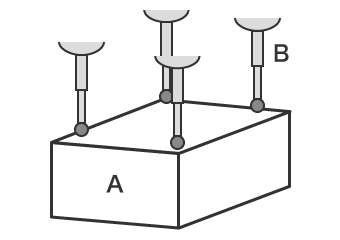
- A
- Obiekt
- B
- Sonda
- Ponieważ punkty danych są rejestrowane w wyniku kontaktu, trudno jest zidentyfikować cały kształt obiektu.
- Pomiar większej liczby punktów w celu uzyskania większej ilości danych pomiarowych może być czasochłonny, a mimo większej liczby punktów danych pełny pomiar obiektu w całości nie jest możliwy.
Rozwiązania typowych problemów dotyczących pomiaru wypaczenia i falistości
Ponieważ konwencjonalne kontaktowe przyrządy pomiarowe mierzą kształty tylko za pomocą linii lub punktów, nie są one w stanie zmierzyć całej powierzchni obiektu pomiaru. Nawet w przypadku pomiaru większej liczby punktów w celu uzyskania większej ilości danych pomiarowych potrzeba wielu roboczogodzin i nadal może nie być możliwe zidentyfikowanie wypaczeń lub falistości i innych cech złożonego kształtu dla całego obiektu. W wielu przypadkach pomiar wypaczeń lub falistości wymaga doświadczenia, wiedzy i umiejętności, których firmy mogą nie być w stanie zapewnić. Zapewnienie niezbędnego personelu pomiarowego również jest poważnym problemem, podobnie jak różnice w wynikach pomiarów między różnymi operatorami.
Aby rozwiązać te typowe trudności pomiarowe, firma KEYENCE opracowała optyczny profilograf 3D ze sterowaniem jednym przyciskiem serii VR.
Urządzenie serii VR dokładnie rejestruje kształt 3D całej powierzchni przez pomiar bezkontaktowy. Mierzy również ogólny trójwymiarowy kształt obiektu umieszczonego na stoliku urządzenia przez skanowanie 3D wykonywane z wysoką dokładnością w ciągu zaledwie sekundy. Umożliwia to natychmiastowe wykonywanie pomiarów ilościowych i kontroli bez odchyleń w wynikach pomiarów. W tej sekcji przedstawiono kilka konkretnych korzyści zapewnianych przez urządzenie serii VR.
Korzyść nr 1: skanowanie kształtu 3D powierzchni obiektu. Kształt całego obiektu można zidentyfikować w natychmiastowy sposób.
W przypadku części elastycznych, takich jak pierścienie O-ring, pomiar i kontrola wypaczenia, falistości lub krzywizny za pomocą kontaktowych przyrządów pomiarowych mogą być trudne, ponieważ nacisk sond lub innych narzędzi zmienia kształt części.
W przypadku urządzenia serii VR wystarczy zeskanować obiekt, umieszczając go wcześniej na stoliku. Kształt 3D obiektu można zarejestrować bezkontaktowo, bez konieczności stosowania jakiegokolwiek mocowania. System pozwala na łatwe wykonywanie kolorowych map wysokości i szybkich pomiarów profilu, umożliwiając wizualizację i identyfikację miejsc oraz dokładnych wartości liczbowych wad kształtu. Umożliwia to prostą identyfikację i korygowanie wad spowodowanych przez formy, matryce i warunki formowania. Ponieważ dane dotyczące kształtu są mierzone ilościowo, możliwe jest łatwe zarządzanie wypaczeniami i falistością w oparciu o tolerancje numeryczne lub wykorzystanie pomiarów do analizy trendów.
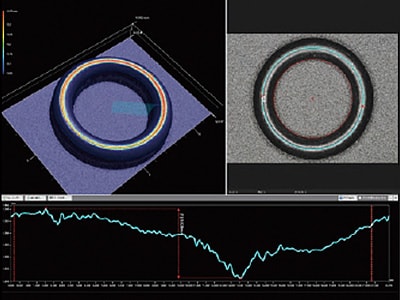
Korzyść nr 2: wizualizacja wypaczeń i falistości na mapie kolorów. Problemy można przedstawić za pomocą danych w formie wizualnej.
Podczas tłoczenia mogą wystąpić nieoczekiwane odkształcenia materiałów z powodu naprężeń mechanicznych. Należy zachować ostrożność, aby zapobiec wypaczeniom, falistości i innym deformacjom kształtu. Jednak w przypadku konwencjonalnych kontaktowych przyrządów pomiarowych pomiar wypaczeń i falistości całego elementu może być trudny, szczególnie w przypadku małych elementów metalowych.
Nawet w przypadku małych i cienkich elementów metalowych profilograf serii VR może wykonać bezkontaktowe skanowanie całego kształtu w ciągu zaledwie sekundy — wystarczy umieścić element na stoliku. Umożliwia to natychmiastową rejestrację wypaczenia lub falistości całego obiektu i wyprowadzenie danych w postaci mapy kolorów. Dzięki udostępnianiu danych, które są łatwe do zrozumienia i interpretacji wizualnej, można zidentyfikować miejsca wad i potencjalne przyczyny, co pozwala na szybkie wdrożenie środków zaradczych i konserwacji zapobiegawczej.
W przypadku profilografów serii VR nie jest wymagane ścisłe pozycjonowanie obiektu. Orientacja elementu umieszczonego na stoliku jest automatycznie korygowana, co umożliwia łatwy pomiar ilościowy i kontrolę.
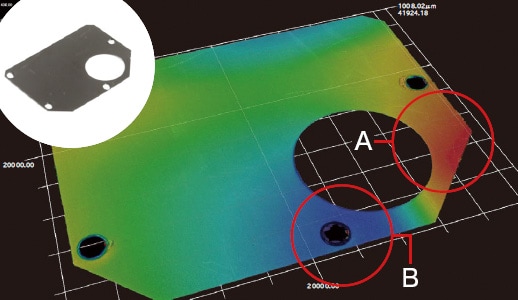
- A
- Wysokie
- B
- Niskie
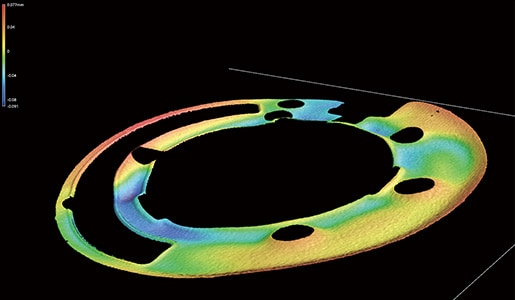
Korzyść nr 3: jednoczesna analiza wielu zestawów danych dzięki różnym opcjom wyświetlania danych.
Profilograf serii VR może zmierzyć kształt 3D całej części przez zeskanowanie powierzchni obiektu w ciągu zaledwie sekundy. Umożliwia to uzyskanie pomiarów ilościowych na dużej liczbie części w krótszym czasie w porównaniu z konwencjonalnymi metodami. Wiele zestawów efektywnie zebranych danych pomiarowych może być wyświetlanych na listach, a ta sama seria pomiarów może być zastosowana jednocześnie do wszystkich zestawów danych.
Umożliwia to pomiar płaskości jednocześnie na wielu częściach oraz identyfikację wszelkich odchyleń w krótkim czasie. Pozwala to na łatwą analizę ilościową zakresu wszelkich wypaczeń lub falistości podczas porównywania części prawidłowych i części nieprawidłowych.
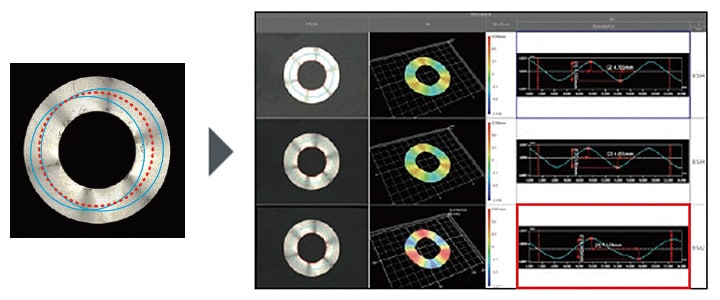
- Po lewej stronie
- W przypadku konwencjonalnego przyrządu dokładne porównanie jest trudne ze względu na różnice w miejscach pomiaru i zmienność mierzonych wartości.
- Po prawej stronie
- W przypadku profilografów serii VR pomiar jest wykonywany natychmiastowo, bez konieczności mocowania. Można łatwo przeprowadzić porównanie ilościowe i analizę wielu zestawów wyników pomiarów, wyświetlając je obok siebie i stosując jednocześnie tę samą serię pomiarów do wszystkich zestawów danych.
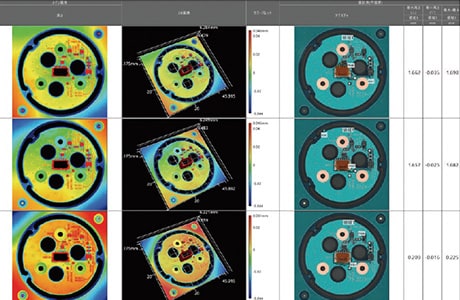
Podsumowanie: znaczna poprawa i wyższa wydajność pomiarów wypaczenia/falistości
Profilograf serii VR umożliwia natychmiastowy pomiar wypaczeń, falistości i innych deformacji 3D za pomocą szybkiego i bezkontaktowego skanowania 3D.
- Ponieważ mierzona jest cała powierzchnia, możliwe jest zidentyfikowanie wszystkich miejsc wypaczeń i falistości na części oraz wykonanie pomiarów profilu w dowolnym miejscu.
- Bezkontaktowy pomiar kształtu o wysokiej dokładności możliwy jest nawet w przypadku miękkich obiektów, takich jak guma i elastyczne tworzywa sztuczne.
- Nie jest wymagane mocowanie. Aby wykonać pomiar, wystarczy umieścić część na stoliku urządzenia i nacisnąć przycisk.
- Kształty 3D można analizować na mapie kolorów. Udostępnianie danych, które są łatwe do zrozumienia i wizualizacji, ułatwia formułowanie i wdrażanie środków zaradczych.
- Można łatwo i ilościowo porównywać i analizować wiele zestawów danych pomiarowych.
Umożliwia to konfigurację parametrów, takich jak tolerancje płaskości, jednocześnie dla wielu zestawów danych pomiarowych. Możliwa jest identyfikacja produktów prawidłowych/nieprawidłowych oraz udostępnianie danych, co pozwala na szybką analizę i rozwiązywanie problemów z wadliwymi częściami. Urządzenie serii VR może zapewnić znaczną poprawę wydajności prac w zakresie pomiarów, analizy wad i wdrażania środków zapobiegawczych.