A festékhibák, a festékvastagság, valamint a festékpigment-diszperzió mérése és ellenőrzése
A festékekkel és festési folyamatokkal szemben támasztott követelmények esztétikai, tartóssági, környezeti és gazdaságossági szempontból is sokat változtak az idők során.
A különböző területeken, például az építőiparban, a gépjárműiparban és más iparágakban mind más és más típusú festékeket és festési folyamatokat alkalmaznak. A gépjárművek karosszériájának fényezéséhez például több jellemző, így az esztétika, valamint az időjárásnak és a fakulásnak való ellenállás terén is a legmagasabb minőségre van szükség.
Ebben a részben példákon és képeken keresztül ismertetjük a festéssel, fényezéssel, bevonatokkal és a legújabb 4K-s digitális mikroszkópunkkal végzett megfigyeléssel és méréssel kapcsolatos alapvető tudnivalókat, valamint a felmerülő problémák megoldásait.
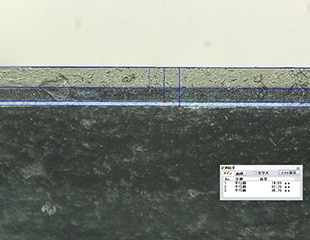
- Festékanyagok
- Festési technikák
- Bevonathibák és megoldások
- A festékvastagság ellenőrzése
- A festékek és bevonatok mérésének és vizsgálatának legújabb példái
- Gyakori eljárások a festékek és bevonatok méréséhez és elemzéséhez
Festékanyagok
A festékek többféle nyersanyagból álló vegyi termékek. A festék tulajdonságait a kötőanyag, azaz a festék filmképző komponense határozza meg, míg a pigment szerepe a rozsdásodás megelőzése és a szín biztosítása.
A kötőanyag adja a festék filmképző jellemzőit (száradási jellemzőit), fizikai tulajdonságait (pl. a film rugalmassága és tapadása) és kémiai funkcióit (pl. a film tartóssága és kémiai ellenálló képessége). A kötőanyag fő alkotóeleme a szintetikus gyanta. Azokat a festékeket, amelyeknél a kötőanyag vízben oldható vagy vízzel diszpergált, vízalapú festékeknek nevezzük. A por formájú és levegővel cseppfolyósított festékeket porfestéknek nevezzük.
A pigmentek apró, a fénynek ellenálló színező részecskék, amelyek nem oldhatók vízben és más oldószerekben. A pigmentek három kategóriába sorolhatók: színes pigmentek, rozsdásodást gátló pigmentek és töltőanyagok. A színes pigmentek adják a festék színét. Ilyen például a titánfehér, a szénfekete, az okkersárga, a karbonkék, a ciánzöld és a kinakridonvörös pigment. A rozsdásodást gátló pigmentek között az alumínium-foszfát, a cink-molibdát és a cinkpor említhető. A töltőanyagok határozzák meg a film tulajdonságait. Ide soroljuk például a megszáradt festék fényességét szabályozó mattító pigmenteket, a funkcionális pigmenteket, például az alumíniumport és a fluoreszkáló vagy foszforeszkáló pigmenteket, valamint az olyan speciális pigmenteket, mint például az infravörös fényvisszaverő anyagok és a rádióhullámokat elnyelő ferriteket.
Festési technikák
A festési folyamat során festék használatával egy réteget képeznek a felületeken. Az így felvitt festék vastagsága általában néhány mikrométertől több száz mikrométerig terjed. Mivel a festékbevonat speciális funkcióval rendelkezhet, a festési folyamat jelentős hatással lehet a költséghatékonyságra.
A festési folyamat három lépésből áll: előkezelés, felvitel és száradás. Többrétegű festékek esetén ez a folyamatot többször ismétlődik.*
Előkezelésként először is megtisztítják az anyag felületét. Általánosságban szólva nedves és száraz módszereket különböztethetünk meg: ezeknél általában nedves bevonatot, illetve homokfúvást használnak.
A festék felvitele folyadék formájában vagy permetezés útján gáz halmazállapotban is történhet. A folyékony festékek felviteléhez ecset, folyadékfüggöny (amelynek során a munkadarab a felső hornyokból áramló festék alatt halad el) vagy a munkadarabra a festéket egy gumis felvivőhenger segítségével felhordó görgős rendszer is használható. A permetezéssel végzett festéshez sűrített levegős spray, elektrosztatikus festékszórás (amelynek során a negatív töltetű festéket viszik fel a pozitív töltetű munkadarabra) és a felvitelhez elektrosztatikusan töltött porbevonat is használható.
A felső és középső réteg esetén az előkezelési folyamat kihagyható.
Bevonathibák és megoldások
Az előkezelt felület állapotával kapcsolatos problémák, például a festési körülményekkel, a festékkel vagy a felhordási módszerrel kapcsolatos problémák a festékbevonatok hibáihoz vezethetnek. A megfelelő festék kiválasztásához, a felviteli mód javításához és a hiba ismételt előfordulásának megakadályozásához elengedhetetlen a hiba vizsgálata és a kiváltó okok azonosítása.
Mi most három gyakori festékhiba esetén magyarázzuk el a lehetséges okokat és azt, hogy miként előzhetők meg ezek a hibák.
Dudorok
Dudorok általában a száradó festékre kerülő idegen részecskék miatt alakulnak ki. Az idegen részecskék például az emberek vagy gépek mozgásának hatására felkavart szennyeződések vagy levegőben lévő részecskék lehetnek, amelyek a maszkolási vagy polírozási folyamat során tapadnak a munkadarabra. A gyantatermékek elektrosztatikus töltést kaphatnak, amikor formázás után eltávolítják azokat az öntőformákból. Ezek az öntőformák aztán magukhoz vonzzák a levegőben lévő idegen részecskéket, amelyek így a termékhez tapadnak.
A festőberendezések környezetének takarítása és a szállítószalagokra szerelt fedelek hatékonyan megakadályozhatják, hogy a levegőben lévő részecskék a festékbe ragadjanak. A statikusságot megszüntető berendezések szintén hasznosak lehetnek az elektrosztatikus idegen részecskék megtapadásának elkerülésében. Ha a festék megszilárdul, módosítani kell a hígító oldatot és/vagy ellenőrizni kell a keverési ciklust. A festék szűrése szintén hasznos módszer a megszilárdulás elkerüléséhez.
- Jelenség:
- Dudorok keletkeznek a festett felületen.
- Lehetséges okok:
- Idegen részecskék tapadtak a festett felületre.
A festékben megszilárdult festékdarabok vagy idegen részecskék vannak.
A festék száradása előtt levegőben lévő részecskék tapadtak a festett felületre.
- Művelet:
- Az előkezelés során tisztítsa meg az anyag felületét.
Szűrje meg a festéket az idegen részecskék eltávolítása érdekében.
Gondoskodjon portalanítási intézkedésekről.
Repedés
A repedések kialakulásának a festék anyagától és a munkadarab festési módjától függően számos lehetséges oka lehet.
Többrétegű bevonatok esetén például repedéseket okozhat, ha nem kompatibilis alap- és fedőrétegeket használ, illetve ha az alapréteg nem száradt meg teljesen. Ilyen esetben megoldás lehet, ha módosítja a festéktípust, vagy hosszabb száradási időt alkalmaz az alapréteghez.
Mivel repedések számos okból előfordulhatnak (például az anyag öregedése következtében), az okok azonosításakor a festékbevonat állapotának alapos vizsgálatára van szükség.
- Jelenség:
- Repedés alakul ki a festékbevonaton.
- Lehetséges okok:
- A felület repedt volt.
Túl vastag volt a bevonat.
Nem megfelelő keményítőszer-keveréket használt (kétkomponensű festékek esetén).
Nem megfelelő hígítót választatott (hígító használata esetén).
- Művelet:
- Szüntesse meg a munkadarab felületi repedéseit az előkezelés során.
Kerülje a vastag rétegeket, amelyek felületi száradást okozhatnak.*
Használat előtt alaposan keverje meg a festéket.
A megadott mennyiségű keményítőanyagot használja.
Felületi száradás: az az állapot, amikor a bevonat felülete már megszáradt, de maga a festékréteg még nem keményedett meg.
Lepattogzás
Lepattogzás többnyire akkor fordul elő, ha a felületet nem kezelték megfelelően, illetve ha a festék nem kompatibilis a szubsztrátummal, vagy az alapréteg nem kompatibilis a fedőréteggel.
Távolítson el minden rozsdát és festékmaradványt a munkadarab felületéről egy csiszolókorong használatával, és a festék felvitele előtt törölje le a felületről az idegen részecskéket és zsírmaradványokat. Azt a jelenséget, amikor a lepattogzást nem kompatibilis festék és szubsztrátum, illetve nem kompatibilis alap- és fedőréteg okozza, rétegek közötti lepattogzásnak nevezzük. E probléma megoldásához a festékkombinációk módosítására és/vagy másfajta felviteli mód alkalmazására van szükség.
Ezek a műveletek a lepattogzás megakadályozását célzó előkezelési műveletek. Ezekből a műveletekből tisztán látszik, hogy a tökéletes festékbevonat eléréséhez milyen fontos a megfelelő előkezelés.
- Jelenség:
- A bevonat elveszíti tapadóképességét és lepattogzik.
- Lehetséges okok:
- Nem volt megfelelő a felület előkezelése, például rozsdamentesítése.
Nem csiszolták le vagy tisztították meg megfelelően a felületet.
Nem megfelelő az alapréteg és a fedőréteg közötti tapadás.
- Művelet:
- Távolítson el a felületről minden rozsdát, zsírt, szennyeződést és port.
Végezzen az adott anyagnak megfelelő előkezelést.
Korábban már festett felület festésekor az új festékréteg felvitele előtt távolítsa el maradéktalanul a régi bevonatot.
Állítsa be megfelelően a festékformulát.
A megadott vastagságban vigye fel a festéket.
A festékvastagság ellenőrzése
A festékvastagság mérése az egyik mód annak ellenőrzéséhez, hogy a festék megfelelő bevonatot képez-e.
A bevonat célja, hogy az anyag korrodálásának elkerülése érdekében megakadályozza, hogy nedvesség és oxigén kerüljön az anyagba. Ezért a bevonat vastagsága jelentős hatással van annak funkcionalitására. Ez nem azt jelenti, hogy a vastag festékréteg mindig jobb – a festékvastagságnak éppen megfelelőnek kell lennie ahhoz, hogy a bevonat tökéletesen ellássa a célját.
A festékvastagság mérése bevonatvastagság-mérő rendszer használatával történik. Léteznek olyan roncsolásmentes bevonatvastagság-mérő rendszerek, amelyek mágnesességet és fluxusvariációt használnak a méréshez, míg más típusok infravörös és ultrahangos módszerekre épülnek.
- Elektromágneses bevonatvastagság-mérő:
- A bevonatvastagság méréséhez egy állandó mágnessel ellátott szondát érintenek a felülethez. A generált mágneses fluxus sűrűsége a mágnes húzóerejének megfelelően változik. Ez a mérőműszer az elektromágnesen áthaladó áram változásait használja a festékvastagság méréséhez. Ezzel a módszerrel mágneses fémanyagokra felvitt bevonatok vagy borítások (nem mágneses fémréteg, szervetlen réteg vagy szerves réteg) vastagsága mérhető. A mérési elv a szonda hegyébe ágyazott mágnes húzóerejére és az alaprétegtől való távolságra épül. Az elektromágneses bevonatvastagság-mérővel azonban nem mérhető pontosan a mágnesesen töltött festékrétegek vastagsága.
- Örvényáramú bevonatvastagság-mérő:
- A bevonatvastagság egy vasmagos tekercsen áthaladó elektromos áram által generált örvényárammal is mérhető. A mérési elv a fémfelületen generált örvényáramérték és a távolság arányán alapul. Az örvényáramú bevonatvastagság-mérők két típusát különböztethetjük meg: az érintkezéses típusú mérőműszerek az örvényáram amplitúdója alapján, míg a nem érintkezéses típusú mérőműszerek az örvényáram fáziskülönbségei alapján mérik a bevonat vastagságát. Ez a mérőműszer vezetőképes, nem mágneses fémekhez (pl. alumínium, réz és ausztenites rozsdamentes acél) és műanyagból, gyantából, gumiból vagy más szigetelőanyagból készült bevonatokhoz használható.
- Infravörös bevonatvastagság-mérő:
- Ez a mérőműszer a bevonatra vetített infravörös fénnyel kapott spektrum használatával, illetve az áteresztett vagy visszavert fény szétszórásával méri a festékvastagságot. Amikor a bevonatra infravöröst fényt vetítenek, a bevonat az adott anyagtól és a bevonat vastagságától függően meghatározott hullámhosszú fényeket nyel el. A célfelület festékvastagsága a fényelnyelési sebesség és a bevonathoz használt anyag vastagsága közötti kapcsolat alapján számítható ki.
- Ultrahangos bevonatvastagság-mérő:
- Amikor a szonda a bevonat felületéhez ér, az érzékelő ultrahanghullámot továbbít az alapréteg felé, ahonnan aztán a hullám visszaverődik a felületre. A bevonatvastagság az ultrahanghullám visszaverődési ideje alapján számítható ki. Ultrahangos bevonatvastagság-mérővel az alábbiak szerint számítható ki a bevonat vastagsága:
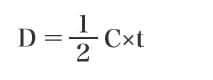
D: Festékvastagság
C: Hangsebesség a bevonatban* (m/s)
t: Mért körbehaladási idő (s)
* Hangsebesség a bevonatban: az egyes anyagokhoz meghatározott körülbelüli érték. Még ha az anyag azonos is, a különböző típusokra más és más hangsebesség jellemző. Emiatt az ultrahangos bevonatvastagság-mérő használata előtt az adott bevonatnak megfelelő beállításokra (kalibrálásra) van szükség.
A festékek és bevonatok mérésének és vizsgálatának legújabb példái
A KEYENCE VHX sorozatú ultranagy felbontású 4K-s digitális mikroszkópja jelentően javítja számos feladat hatékonyságát, és a nagy felbontású képek révén a festékek és bevonatok kifinomult megfigyelését és értékelését teszi lehetővé.
Többrétegű festék vastagságának mérése nagy felbontású optikai képek használatával
A KEYENCE legújabb 4K-s digitális mikroszkópja optikai képek alapján méri a festékvastagságot. A mikroszkópot nem befolyásolják az áttetsző rétegek, ami éles fókuszbeállítást tesz lehetővé. A kristálytiszta képek sokkal részletesebb információkat biztosítanak a bevonatról.
A mikroszkóp a bevonat tényleges állapotát rögzíti, így a fókuszálási problémák miatt korábban nem mérhető festékvastagságok esetén is pontos megfigyelést tesz lehetővé.
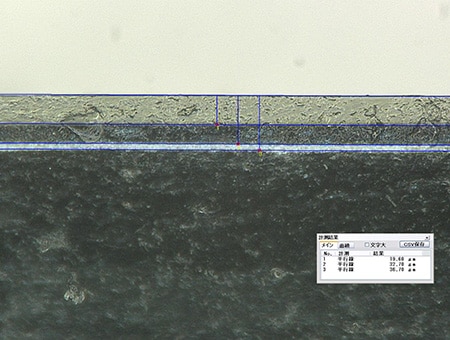
Átlátszó rétegek 3D-s vizsgálata fejlett fókusz és többszörös megvilágítás használatával
A jelentősen nagyobb képkockasebességű kamerának köszönhetően amint a megfigyelési pontra viszi a tárgyasztalt, a VHX automatikusan végigpásztázza a minta teljes fókusztartományát és azonnal tökéletesen éles képet alkot.
A mélységkompozíció és többszörös megvilágítás funkciót kombináló digitális mikroszkóppal a felhasználók tökéletesen éles képet rögzíthetnek, és szabadon kiválaszthatják az adott képhez használni kívánt világítási mintát.
Emellett a nagy felbontású objektívet, 4K-s CMOS-érzékelőt és kiegészítő világítást használó optikai árnyékhatás üzemmód segítségével színadatokat vetíthetnek a képre, így egy időben jeleníthetik meg az egyenetlen felszín adatait és a színadatokat. Ez lehetővé teszi a dudorok és egyéb festékhibák profilmérését, kvantitatív elemzéshez is elérhetővé téve az információkat.
Az egyetlen egységben 2D-s és 3D-s mérések elvégzését is lehetővé tevő 4K-s digitális mikroszkópok új, a nagyított nézetű megfigyeléssel kapcsolatos univerzális igényeknek megfelelő megközelítést kínálnak a vizsgálatokhoz.

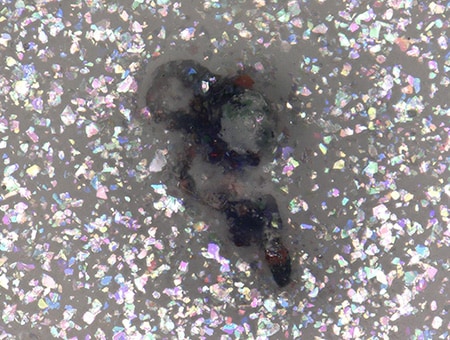
kristálytiszta képen jeleníthetők meg a többszörös
megvilágítás és mélységkompozíció funkció használatával.
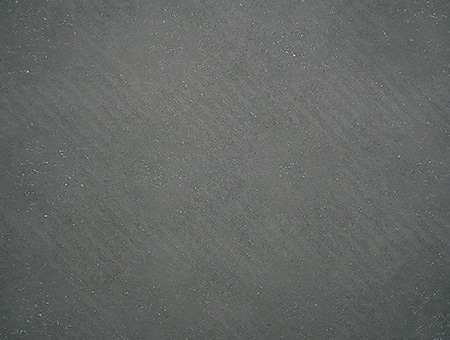
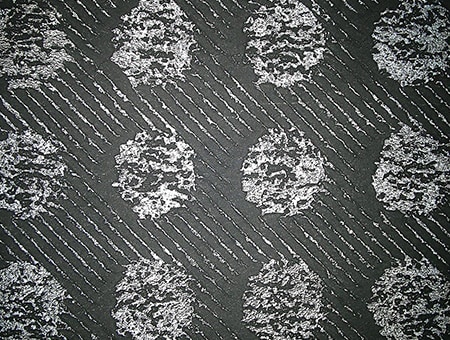
árnyékhatás üzemmóddal készült képpel
A pigmentdiszperzió pontos mérése
A festék funkcionalitását meghatározó egyik legfontosabb elemet a pigmentek jelentik. A VHX sorozat használatával hatékonyan megfigyelhető és számszerűsítheti a pigmentek eloszlása. A pigmentek apró, a fénynek ellenálló színező részecskék, amelyek nem oldhatók vízben és más oldószerekben. A bevonat anyagához megfelelő pigmenteket keverve meghatározott funkció adható a bevonatnak.
Egy 4K-s digitális mikroszkóp segítségével egyszerűen elvégezhető az adott tartományba eső célterületek mérése és számlálása. A felesleges célterületek kizárhatók, az átfedésben lévő célterületek pedig elkülöníthetők. A mérési eredmények hisztogram formájában exportálhatók.
Ez a műveletsorozat rendkívül egyszerű, ám megbízható, kivételesen pontos méréseket eredményez. A mikroszkóp segítségével bármilyen speciális tudás vagy tapasztalat nélkül is magas szintű elemzések végezhetők.
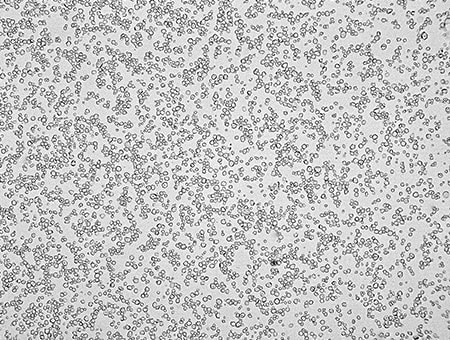
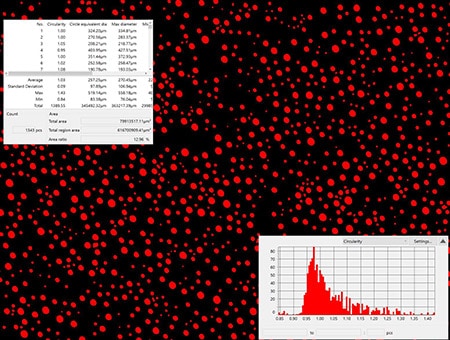
Gyakori eljárások a festékek és bevonatok méréséhez és elemzéséhez
A VHX sorozatú, nagy felbontású 4K-s digitális mikroszkóp kivételes hatékonyságot biztosít, és az emberi hibák kiküszöbölése révén pontos mérést és elemzést tesz lehetővé.
A modern optikai képfeldolgozási és automatizálási technológiákkal generált nagy felbontású 4K-s képek a bevonatok, festékdudorok és diszperziós részetek pontos megfigyelését teszik lehetővé. Mivel a mikroszkóp használatához nincs szükség bonyolult műveletekre, még a digitális mikroszkópok terén nem jártas felhasználók is pillanatok alatt elvégezhetik a különböző speciális elemzéseket.
A jelentési funkció használatával a rögzített vagy mért adatok egyszerűen fix formátumú jelentés formájában exportálhatók. Ezen adatok intranet kiszolgálón keresztül történő megosztása a minőségbiztosítási folyamat és az iparági szabványoknak való megfelelés támogatása mellett a festékhibák okainak feltárásához és a folyamatok javításához is hasznos lehet.
A számos egyéb fejlett funkcióval ellátott VHX sorozat hatékony támogatást biztosít a fényezések és bevonatok minőségének és megbízhatóságának biztosításához.
A részletekért kattintson az alábbi gombra, és töltse le a katalógust. Kérdés esetén kattintson az alább látható másik gombra, és vegye fel a kapcsolatot a KEYENCE-szel.