Messung von Gussprodukten
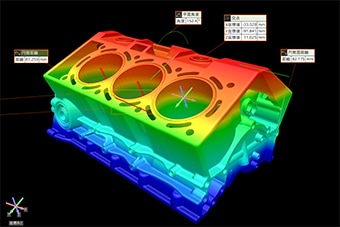
Das Gießen eignet sich für die Herstellung komplex geformter sowie großer Produkte, obwohl die Festigkeit geringer ist als bei Produkten, die durch Walzen oder Schmieden hergestellt werden. Das Gießen hat außerdem den Vorteil, dass es eine Massenproduktion zu geringen Kosten ermöglicht. Unter Ausnutzung dieser Vorteile wird der Guss zur Herstellung von Produkten in einer Vielzahl von Bereichen eingesetzt. Darunter fallen Automobile und andere Transportmaschinen, Industriemaschinen, elektrische Geräte, Kommunikationsgeräte und Produkte des täglichen Bedarfs.
Allerdings sind Gussprodukte leicht anfällig für innere und äußere Defekte aufgrund von Metallviskosität, Temperatur oder Verunreinigung während des Gießens.
In diesem Abschnitt werden die gängigsten Gießverfahren, die Messung von Prototypen in der Entwicklung und im Design sowie eine Messmethode erläutert, die Fehler in der Massenproduktion verhindern kann. Außerdem werden Herausforderungen bei bisher verwendeten Messungen und Lösungen dafür vorgestellt.
- Gießen
- Gussarten
- Defekte bei Gussprodukten
- Herausforderungen bei der Messung
- Lösungen zur Messung von Gussprodukten
- Zusammenfassung: Höhere Effizienz bei der Messung von Gussprodukten
Gießen
Gießen ist ein Metallbearbeitungsverfahren, bei dem geschmolzenes Metall in einen Hohlraum mit der gewünschten Form gegossen wird, wo es dann abkühlt und sich verfestigt. Ein solcher Hohlraum mit der gewünschten Form wird Gussform genannt, und ein durch Gießen hergestelltes Produkt wird als Gusserzeugnis oder Gussprodukt bezeichnet. Zu den Gussformen gehören Metallformen, sowie andere Formen aus Sand, Kunststoff oder Gips. Metall- und Sandformen sind die am häufigsten verwendeten Arten. Zu den Metallen, die beim Gießen verwendet werden, gehören Gusseisen, Gussstahl, Aluminium- und Magnesiumlegierungen, die je nach den Anforderungen des Endprodukts ausgewählt werden.
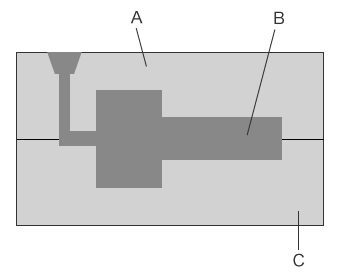
- A
- Gussform (obere Form)
- B
- Gussprodukt
- C
- Gussform (untere Form)
Gussarten
Gussarten können nach verschiedenen Aspekten eingeteilt werden, z. B. nach dem Material der Gussform, dem Verfahren zur Herstellung der Form und dem Modelltyp. Dieser Abschnitt konzentriert sich auf Kategorien, die auf dem Material der Gussform basieren, was die häufigste Art der Kategorisierung ist. Nachfolgend werden der Sandguss, das Kokillengießverfahren und das Wachsausschmelzverfahren erklärt.
Sandguss
Sandguss ist eine Methode, bei der geschmolzenes Metall in eine Sandform mit der gewünschten Form gegossen wird, wo es dann abkühlt und sich verfestigt. Der Sand, der zur Herstellung der Form verwendet wird, wird Formsand genannt und besteht aus Quarzsandkörnern, die mit einem Bindemittel oder Zusatzstoff wie Bentonit (Tonmineral), Wasserglas oder Kunststoff vermischt sind. Formen aus Sand werden als Sandformen bezeichnet.
Sandformen unterstützen komplexe Formen und können, wenn sie für die Fertigung kleiner Serien verwendet werden, kostengünstiger und schneller hergestellt werden als Formen, die im Kokillengießverfahren verwendet werden. Aufgrund der geringeren Abkühlungsgeschwindigkeiten während des Gießens haben Gussprodukte, die im Sandgussverfahren hergestellt werden, jedoch im Allgemeinen eine niedrigere Maßgenauigkeit und eine geringere Festigkeit im Vergleich zu Produkten, die mit anderen Verfahren hergestellt werden. Außerdem wird eine Sandform nach einmaligem Gebrauch zerstört, was bei der Massenproduktion zu höheren Betriebskosten führt.
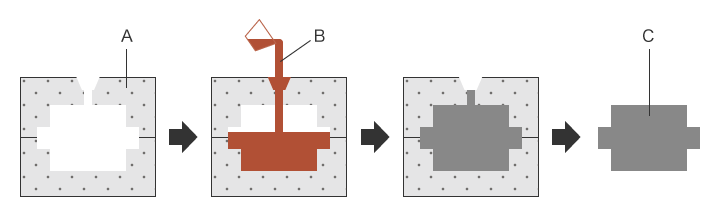
- A
- Sandform
- B
- Geschmolzenes Metall
- C
- Gussprodukt
Kokillengießverfahren
Der Kokillenguss ist ein Gießverfahren, bei dem geschmolzenes Metall in eine Metallform gegossen wird, wo es dann abkühlt und erstarrt.
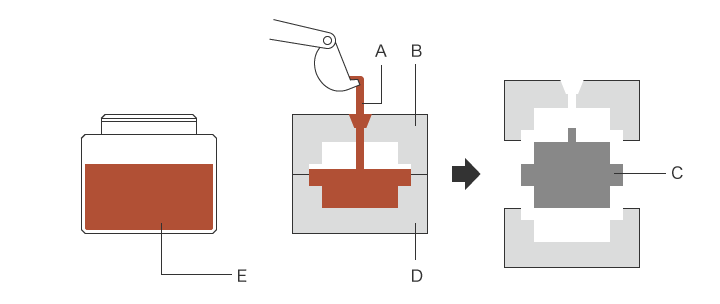
- A
- Geschmolzenes Metall
- B
- Gussform (obere Form)
- C
- Gussprodukt
- D
- Gussform (untere Form)
- E
- Geschmolzenes Metall
- Schwerkraftguss:
- Beim Schwerkraftgießverfahren wird die Schwerkraft genutzt, um die Form mit geschmolzenem Metall zu füllen. Die Schwerkraft wird auch beim Sandguss verwendet, aber die Formen, die bei dieser Methode verwendet werden, können wiederholt eingesetzt werden und eignen sich daher besser für die Massenproduktion. Da das geschmolzene Metall schnell abkühlt, können anhand des Schwerkraftgießverfahrens Gussprodukte mit hervorragenden mechanischen Eigenschaften erzeugt werden. Außerdem wird das geschmolzene Metall mit niedriger Geschwindigkeit gegossen, wodurch weniger Luft und Gase als beim Druckguss eingeschlossen werden. Da beim Füllen der Form kein Druck ausgeübt wird, ist es möglich, Teile zu verwenden, die als Kerne bezeichnet werden, um Gussprodukte mit komplexen Formen und hohlen Innenräumen herzustellen.
Aufgrund dieser Vorteile ist der Schwerkraftguss das am häufigsten verwendete Verfahren zur Herstellung einer breiten Palette von Gussprodukten. Allerdings hat diese Methode auch einige Nachteile. Da zum Beispiel kein Druck ausgeübt wird, muss die Form vollständig mit geschmolzenem Metall gefüllt werden, was die Produktionsquote verringert. Die niedrige Füllgeschwindigkeit erhöht auch die Zykluszeit. - Hochdruckguss:
- Beim Hochdruckguss wird die Form bei niedriger Geschwindigkeit mit geschmolzenem Metall gefüllt, beim Erstarren des Metalls wird dann von außen Druck ausgeübt. Da dies bei niedriger Geschwindigkeit geschieht, kommt es zu einem geringeren Einschluss von Luft und Gasen als beim Druckguss. Da der Druck höher ist als beim Schwerkraftguss, können mit dieser Methode mechanisch starke Gussprodukte mit feinen Metallstrukturen hergestellt werden.
Druck kann direkt oder indirekt ausgeübt werden. Bei der direkten Druckanwendung wird ein Druckkolben, der so genannte Stempel, verwendet, um direkt Druck auf das geschmolzene Metall auszuüben. Bei der indirekten Druckanwendung wird der Druck beim Füllen des Formhohlraums mit geschmolzenem Metall mit Hilfe eines Kolbens ausgeübt. Im Allgemeinen wird die direkte Druckanwendung als geeigneter für die Herstellung von Gussprodukten mit einfachen Formen angesehen, während die indirekte Druckanwendung als geeigneter für die Herstellung von mittelgroßen oder großen Gussprodukten mit komplexen Formen angesehen wird. - Niederdruckguss:
- Beim Niederdruckguss wird die Form mit Hilfe von Druckluft oder Inertgasdruck mit geschmolzenem Metall gefüllt. Das geschmolzene Metall erreicht jeden Winkel des Formhohlraums und bleibt unter Druck, bis es abkühlt und sich verfestigt. Dadurch wird das Auftreten von Defekten wie Schrumpfungen und Lunkern reduziert. Die Druckausübung wird gestoppt, wenn das geschmolzene Metall am Anschnitt erstarrt ist, und das geschmolzene Metall, das nicht zur Herstellung des Gussprodukts benötigt wird, fließt in den Tiegel zurück. Dies führt zu einer höheren Produktionsquote als beim Sandguss und Schwerkraftguss. Kerne können auch wie beim Schwerkraftgießen verwendet werden, wodurch es möglich ist, Gussprodukte mit komplexen Formen und hohlen Innenräumen herzustellen. Gleichzeitig hat die lange Abkühlzeit bei dieser Methode den Nachteil einer geringeren Produktivität aufgrund der langen Zykluszeit.
- Schleuderguss:
- Beim Schleuderguss wird das geschmolzene Metall in eine zylindrische Form gegossen, die sich mit hoher Geschwindigkeit dreht. Die Zentrifugalkraft bewirkt, dass sich das geschmolzene Metall an der Innenwand der Form ausbreitet und zu einem zylindrischen Gussprodukt geformt wird. Die Zylinder können vertikal oder horizontal sein. Vertikale Gussformen werden zur Herstellung von kurzen Gussprodukten verwendet. Horizontale Gussformen werden zur Herstellung von langen Gussprodukten verwendet. Mit dem Schleuderguss können hohle Gussprodukte ohne die Verwendung von Kernen hergestellt werden. Weitere Vorteile sind, dass kein Anschnitt oder Druck erforderlich ist und dass die Metalldichte des Gussprodukts durch die Steuerung der Drehgeschwindigkeit verändert werden kann. Mit einer kurzen Abkühlzeit eignet sich das Schleudergussverfahren für das Gießen schnell erstarrender Materialien und die Herstellung dünner Rohre. Es können auch Gussprodukte mit komplexen Formen hergestellt werden. Daher wird der Schleuderguss zur Herstellung von Gussprodukten wie Wasserrohren, Gasrohren, Lagermetall und silbernen Zahnkronen verwendet. Der Schleuderguss hat auch Nachteile, wie z. B. das Auftreten von Entmischung, die durch die Zentrifugalkraft verursacht wird, sowie Rissbildung, die unmittelbar nach dem Abkühlen auftreten kann.
- Druckguss:
- Beim Druckguss wird geschmolzenes Metall unter hohem Druck und mit hoher Geschwindigkeit in eine Form gespritzt, die dann in kurzer Zeit abkühlt. Der Druckguss ermöglicht das Gießen komplizierter Formen mit hochpräzisen Abmessungen, und aufgrund der kurzen Zykluszeit ist er für die Massenproduktion geeignet. Druckguss wird hauptsächlich für das Gießen von Metallen mit niedrigem Schmelzpunkt verwendet, wie z. B. Aluminium-, Zink- und Magnesiumlegierungen. Es gibt zwei Arten von Druckgussmaschinen, die Warmkammer- und die Kaltkammermaschinen.
Bei einer Warmkammermaschine ist die Gießmaschine in einen Ofen integriert, der das geschmolzene Metall enthält. Diese Art von Maschine wird hauptsächlich für den Guss von Zinklegierungen verwendet. Bei einer Kaltkammermaschine sind die Gießmaschine und der Ofen, der das geschmolzene Metall enthält, getrennt. Das geschmolzene Metall wird mit einer Pfanne in die Einspritzöffnung gegossen.
Kaltkammermaschinen werden hauptsächlich für den Guss von Aluminiumlegierungen verwendet. Der Druckguss ermöglicht das Gießen komplizierter Formen mit hochpräzisen Abmessungen. Ein Nachteil ist jedoch, dass durch das Einspritzen des geschmolzenen Metalls in die Druckgussform mit hoher Geschwindigkeit Luft, Formtrennmittel und andere Stoffe in das Gussprodukt gelangen können. Aus diesem Grund können im Druckguss hergestellte Gusserzeugnisse nicht als Teile verwendet werden, die eine hohe Festigkeit erfordern.
Wachsausschmelzverfahren
Das Wachsausschmelzverfahren, auch bekannt als Feinguss, ist ein Präzisionsgussverfahren. Ein Modell wird aus einer Mischung von Materialien mit niedrigem Schmelzpunkt, wie Paraffin, Kunststoff und Füllstoff, hergestellt. Das Modell wird dann mit einem feuerfesten Material wie Keramik überzogen. Anschließend wird es geschmolzen und fließt aus, um die Form zu erzeugen. Ein Vorteil des Wachsausschmelzverfahrens besteht darin, dass die Formen nicht geöffnet werden müssen. Dadurch kann Metall in komplexen Formen gegossen werden, die beim Sandguss oder anderen Kokillengießverfahren nicht möglich sind. Da die Formen aus einem feuerfesten Material wie Keramik bestehen, kann diese Methode auch zum Gießen von Metallen mit hohem Schmelzpunkt wie Kohlenstoffstahl und Edelstahl verwendet werden. Ein Nachteil des Wachsausschmelzverfahrens ist, dass die Gussformen nach einmaligem Gebrauch entsorgt werden müssen, was dieses Verfahren für die Massenproduktion ungeeignet macht.
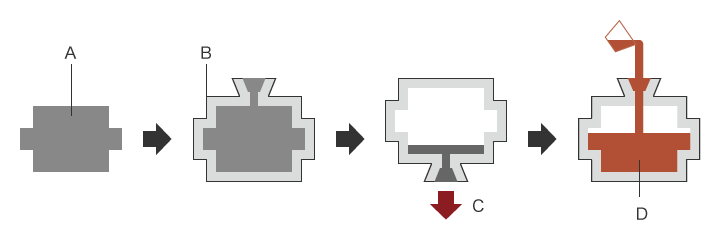
- A
- Modell
- B
- Feuerfestes Material (Form)
- C
- Wachsentfernung
- D
- Geschmolzenes Metall
Defekte bei Gussprodukten
Beim Gießen können Defekte durch verschiedene Ursachen auftreten. Es ist notwendig, die Ursache sofort zu identifizieren und Gegenmaßnahmen zu ergreifen, da Defekte die Produktionsquote verringern und auch die Rücksendung oder den Rückruf von Produkten verursachen können. In diesem Abschnitt werden einige typische Arten von Defekten vorgestellt, die beim Gießen auftreten.
Lunker (Hohlräume)
Das geschmolzene Metall, das die Form füllt, schrumpft, wenn es abkühlt. Wenn das abgekühlte Metall zu erstarren beginnt, schrumpft es weiter. Die Schrumpfungsmenge muss mit geschmolzenem Metall aus einem noch nicht erstarrten Teil aufgefüllt werden. Da das geschmolzene Metall jedoch nicht mehr nachgefüllt werden kann, nachdem das Produkt erstarrt ist, bilden sich Hohlräume oder Vertiefungen an Stellen, an denen die Menge des geschmolzenen Metalls nicht ausreichend war. Diese Hohlräume und Vertiefungen werden als Lunker bezeichnet.
Lunker treten an der Innen- und Außenseite von Gussprodukten auf. Externe Lunker werden auch als offene Lunker bezeichnet und sind Vertiefungen, die auf einem Teil der Oberfläche eines Gussprodukts auftreten. Interne Lunker sind Hohlräume, die sich im Inneren eines Gussprodukts bilden. Die Oberfläche des Lunkers ist rau und hat eine bläulich-violette oder schwarz-braune Farbe. Beide Arten von Lunkern treten an den Teilen auf, die zuletzt erstarren, wie sich überschneidende Teile, Ecken, Kanten und Anschnitte.
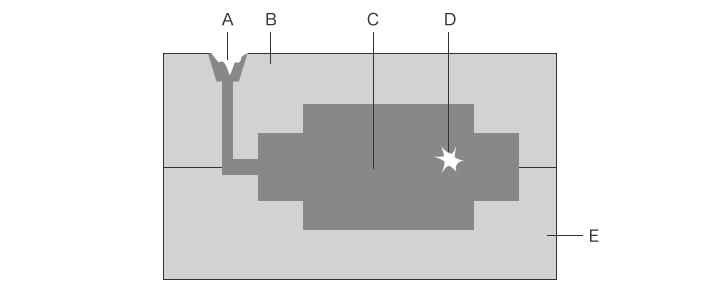
- A
- Externer Lunker
- B
- Gussform (obere Form)
- C
- Gussprodukt
- D
- Interner Lunker
- E
- Gussform (untere Form)
Blaslunker, Nadelloch
Blaslunker und Nadellöcher sind Defekte, die runde Hohlräume im Inneren eines Gussprodukts bilden. Diese Defekte treten auf, wenn Gas oder Luft in das geschmolzene Metall gelangt, das in die Form gegeben wird. Der Name wird durch die Größe des Hohlraums bestimmt. Ein Hohlraum mit einem Durchmesser von 2 mm oder mehr wird als Blaslunker bezeichnet, während ein Hohlraum mit einem Durchmesser von weniger als 2 mm als Nadelloch bezeichnet wird.
Die Gase, die diese Defekte verursachen, werden durch chemische Reaktionen zwischen dem geschmolzenen Metall und Fremdstoffen oder durch Feuchtigkeit erzeugt. Beim Druckguss und anderen Gussverfahren, bei denen geschmolzenes Metall mit hoher Geschwindigkeit eingespritzt wird, können Blaslunker und Nadellöcher entstehen, wenn Luft in das geschmolzene Metall eingeschlossen wird.
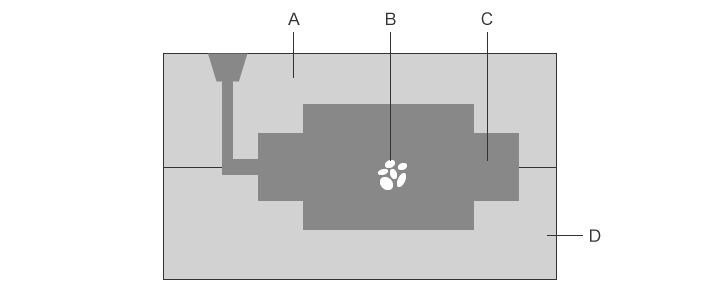
- A
- Gussform (obere Form)
- B
- Blaslunker/Nadellöcher
- C
- Gussprodukt
- D
- Gussform (untere Form)
Rissbildung
Rissbildung ist ein Defekt, bei dem Risse im Gussprodukt auftreten. Risse, die bei hohen Temperaturen auftreten, unterscheiden sich von Rissen, die bei niedrigen Temperaturen auftreten. Risse, die bei hohen Temperaturen auftreten, werden als Heißrisse bezeichnet, wobei die Risse in dem Teil auftreten, der zuletzt erstarrt. Risse, die bei niedrigen Temperaturen auftreten, werden als Kaltrisse bezeichnet, wobei die Risse während oder nach dem Abkühlen auftreten. Risse, die entstehen, wenn ein erstarrtes Teil während des Erstarrungsprozesses an einem nicht erstarrten Teil zieht, werden als Schwindungsrisse oder Erstarrungsrisse bezeichnet. Risse, die aufgrund von mechanischer Spannung durch ungleichmäßige Dicke oder Spannung durch Schwinden entstehen, werden als Spannungsrisse bezeichnet.
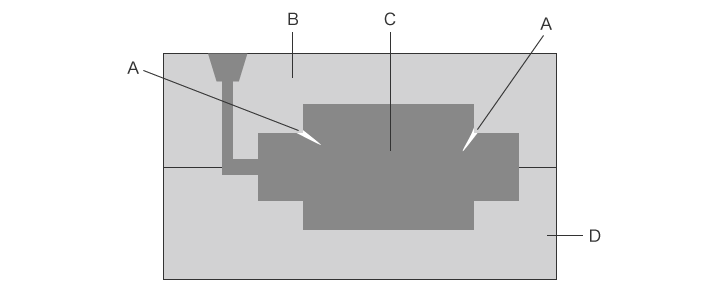
- A
- Rissbildung
- B
- Gussform (obere Form)
- C
- Gussprodukt
- D
- Gussform (untere Form)
Fehlguss
Ein Fehlguss ist ein Defekt, bei dem der Formhohlraum nicht vollständig mit geschmolzenem Metall gefüllt wird, was zu einer unzureichenden Befüllung des Gussprodukts führt. Fehlgüsse treten an dünnen oder schmalen Stellen auf, wodurch eine Form mit abgerundeten Kanten entsteht. Dieser Defekt tritt auf, wenn das geschmolzene Metall den Formhohlraum nicht vollständig ausfüllt. Er kann durch zu enge Formhohlräume, eine niedrige Füllgeschwindigkeit des geschmolzenen Metalls, eine niedrige Formtemperatur oder eine unzureichende Entgasung des Formhohlraums verursacht werden. Andere Defekte, die als Folge einer unsachgemäßen Befüllung mit geschmolzenem Metall auftreten können, sind Kaltverschlüsse, die eine Begrenzungslinie auf der Oberfläche des Gussprodukts bilden, und Fließlinien, die unregelmäßige Falten auf der Oberfläche des Gussprodukts zur Folge haben.
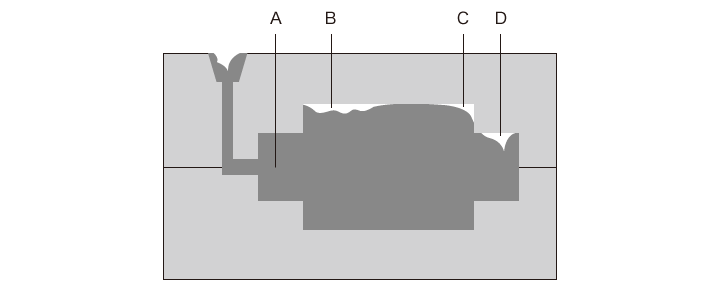
- A
- Gussprodukt
- B
- Fließlinie
- C
- Fehlguss
- D
- Überlappung
Verformungen (Wölbung, Welligkeit)
Zu den Verformungen, die bei Gussprodukten auftreten, gehören Wölbung und Welligkeit, die durch ein Problem während des Gießverfahrens verursacht werden. Beim Gießen, bei dem das bei hoher Temperatur geschmolzene Metall eine Form bildet, variiert die Abkühlgeschwindigkeit bei verschiedenen Dicken und an verschiedenen Stellen. Dünne Teile kühlen schneller ab, während dicke Teile und die zuletzt gefüllten Teile mehr Zeit zum Abkühlen benötigen. Wenn ein Innenteil, das Zeit zum Abkühlen benötigt, an einem Teil zieht, das bereits abgekühlt ist, entstehen Eigenspannungen, die eine Ursache für Verformungen sind.
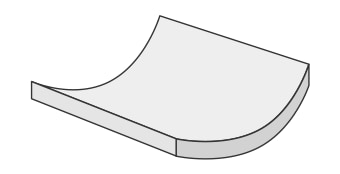
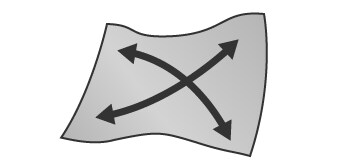
Herausforderungen bei der Messung
Es ist sehr wichtig, sich zu vergewissern, dass die Abmessungen und die Form eines Gussprodukts wie vorgesehen (innerhalb der Toleranzen) sind. Eine hochpräzise und quantitative 3D-Formmessung ist erforderlich, insbesondere für Gussprodukte, die als Präzisionsteile oder mit komplexen Formen verwendet werden, da diese Erzeugnisse die Festigkeit und Leistung beeinflussen können.
Einige gängige Messgeräte, wie z. B. 3D-Koordinatenmessgeräte und vereinfachte 3D-Scanner, können bestimmte Stellen auf einem Produkt nicht messen und deshalb eine geringe Messgenauigkeit aufweisen. Viele Fehlerursachen können durch eine Analyse, die auf den mit diesen Messgeräten erfassten Messdaten basiert, nicht identifiziert werden. Außerdem ist die Messung mit diesen Instrumenten sehr zeitaufwändig.
Herausforderungen bei der Messung – 3D-Koordinatenmessgerät
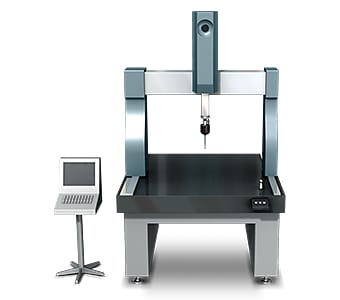
Wenn Sie zum Beispiel mit einem 3D-Koordinatenmessgerät Gussfehler wie Lunker, Risse und Fehlgüsse in einem kleinen Bereich messen, müssen Sie mit einem Messtaster eine virtuelle Oberfläche dieses Bereichs erstellen. Allerdings ist es sehr schwierig, mit dieser Methode eine genaue Messung durchzuführen. Auch bei der Messung einer kleinen Fläche ist es aufgrund der geringen Anzahl von Messpunkten schwierig, die genaue 3D-Form zu ermitteln.
Herausforderungen bei der Messung – 3D-Scanner
Mit einem 3D-Scanner ist die Messung der Form relativ einfach, da das System Licht auf das Messobjekt richtet und dessen Form anhand des vom Messobjekt reflektierten Lichts misst. Bisher verwendete 3D-Scanner leiden jedoch unter der geringen Bildauflösung, der hohen Verarbeitungszeit und der geringen Genauigkeit bei der Messung komplexer Oberflächen. 3D-Scanner sind unter Umständen auch nicht in der Lage, Formen je nach Position und Ausrichtung des Messobjekts korrekt zu messen, und das Fehlen von Messfunktionen macht es unmöglich, genaue Prüfungen durchzuführen.
Lösungen zur Messung von Gussprodukten
Eine Formanalyse ist unerlässlich, um die Qualität von Gussprodukten zu gewährleisten. Allerdings erfordern 3D-Koordinatenmessgeräte ein hohes Maß an Fachkenntnis, und die Datenerfassung kann zeitaufwändig sein. Darüber hinaus sind viele vereinfachte 3D-Scanner nicht mit den Systemen und der Genauigkeit ausgestattet, die für den Einsatz während der Forschungs- und Entwicklungsphase, der Prüfung zur Bestimmung der Schweißbedingungen, der Fehlerursachenanalyse und der schnellen Fehlerbehebung erforderlich sind.
Daher hat KEYENCE die optischen 3D-Koordinatenmessgeräte der Modellreihe VL entwickelt.
Die Modellreihe VL erfasst präzise die 3D-Form der gesamten Oberfläche, ohne das Messobjekt zu berühren. Ein 3D-Scan des Messobjekts auf dem Objekttisch kann in kürzester Zeit abgeschlossen werden, wodurch eine hochpräzise Messung der 3D-Form möglich ist. Das System ist in der Lage, sofortige und quantitative Messungen durchzuführen, ohne dass die Messergebnisse variieren, selbst wenn es von ungeübten Anwendern bedient wird. In diesem Abschnitt werden einige Vorteile der Modellreihe VL vorgestellt.
Vorteil 1: Die 3D-Form der gesamten Messobjektoberfläche kann mit einer einzigen Messung erfasst werden.
Mit einem einzigen Klick kann die Modellreihe VL mittels der hochauflösenden 9 Megapixel Kamera das Objekt erfassen und ermöglicht so die genaue Messung komplexer Gussprodukte.
Die maximalen und minimalen Unregelmäßigkeiten der Oberfläche können in einer leicht verständlichen Farbkarte angezeigt werden, womit Sie die Stellen, an denen Defekte aufgetreten sind, leicht identifizieren können. Anhand des 3D-Messvergleichs können auch Querschnitte gemessen werden.
Darüber hinaus können Messdaten von mehreren Messobjekten nebeneinander verglichen werden, und die gewünschten Bedingungen können auf mehrere Datensätze gleichzeitig angewendet werden.
Diese Funktionen reduzieren den Zeitaufwand für die Analyse der Gussprodukte erheblich.
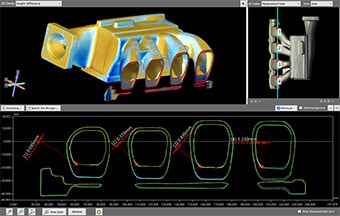
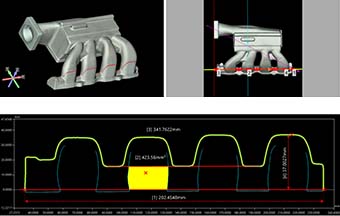
Vorteil 2: Die Bedienung ist einfach und die Messung kann auch von ungeübten Anwendern durchgeführt werden, ohne dass es zu Abweichungen bei den Messwerten kommt.
Die Messung von 3D-Formen kann ganz einfach durchgeführt werden, indem Sie das Messobjekt auf den Objekttisch legen und mittels eines Klicks den Scanvorgang starten. Da eine automatische Positionskorrektur anhand von Messobjektdaten möglich ist, ist eine genaue Nivellierung oder Positionierung nicht erforderlich. Die Modellreihe VL umfasst die neue „Smart Stage“-Funktion, die den Messbereich entsprechend der Größe des Messobjekts automatisch konfiguriert. Damit entfällt die Arbeit, die bislang für die Einstellung der Messlänge und des Z-Bereichs erforderlich war.
Insgesamt stehen diverse Messwerkzeuge zur Messung von Form-, Lage- und Ausrichtungstoleranzen anhand der erfassten 3D-Daten zur Verfügung. Während die Messung der Ebenheit normalerweise viel Zeit in Anspruch nimmt, weil viele einzelne Punkte gemessen werden müssen, kann die Modellreihe VL die Messung innerhalb kürzester Zeit durchführen, indem sie die Oberfläche optisch erfasst. Die hochpräzise Analyse kann für die gesamte Form oder einen Teil davon durchgeführt werden, was eine schnelle und genaue Fehlerbehebung ermöglicht.
Die Modellreihe VL ist nicht nur einfach einzurichten, sondern ermöglicht durch ihre einfache Bedienung auch Anwendern ohne Messerfahrung Objekte und Formen präzise zu messen. Dadurch kann die Anzahl der Proben nicht nur in der Forschungs- und Entwicklungsphase und für Tests zum Festlegen der Bedingungen, sondern auch für die Messung und Prüfung von Produkten bei der Serienfertigung problemlos erhöht werden.
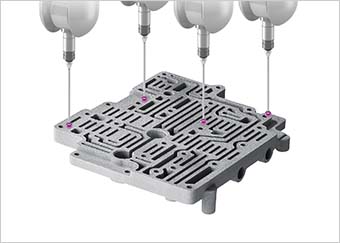
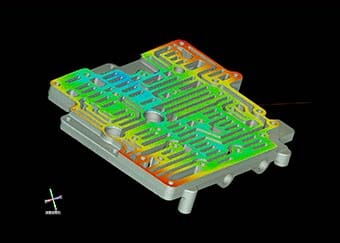
![[Formtoleranz] Ebenheit, Zylindrizität, Geradheit, Rundheit [Ausrichtungstoleranz] Parallelität, Rechtwinkligkeit, Winkligkeit [Lagetoleranz] Position, Konzentrizität, Koaxialität, Symmetrie](/dede/Images/ss_measurement-solutions_casting_017_2012816.png)
Vorteil 3: Unterschiede zu CAD-Daten können in Farbe visualisiert werden.
Durch den Vergleich der CAD-Daten eines Produkts mit den erfassten Messdaten können Unterschiede zwischen dem Ist-Zustand des Produktes und den Sollwerten visualisiert werden. Bei Objekten, die mit bisher verwendeten Systemen schwer zu messen waren, können durch den Vergleich der Messergebnisse mit den CAD-Daten bisher unentdeckte Defekte identifiziert werden. Dadurch wird der Zeitaufwand für die Analyse bei der Untersuchung von Gussfehlern, der Identifizierung der Ursache und anderen damit verbundenen Aktivitäten erheblich reduziert.
Da eine breite Palette von Maßhaltigkeitsprüfungen unterstützt wird, ermöglicht die präzise Messung der Maße an den betreffenden Stellen eine detaillierte Problemanalyse.
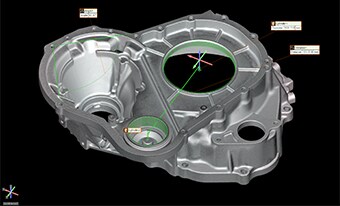

Zusammenfassung: Höhere Effizienz bei der Messung von Gussprodukten
Die Modellreihe VL kann die 3D-Formen von Gussprodukten durch 3D-Scans mit hoher Geschwindigkeit genau und sofort messen, ohne das Messobjekt zu berühren, und bietet die folgenden Vorteile:
- Da die gesamte Oberfläche gemessen wird, ist es möglich, alle Fehlerstellen auf dem Messobjekt zu identifizieren und die Profilmessung an jedem gewünschten Bereich durchzuführen.
- Berührungslose, hochpräzise Messungen sind selbst bei Messobjekten mit komplexen Formen möglich.
- Es ist keine Positionierung erforderlich. Legen Sie für die Messung das Messobjekt einfach auf den Objekttisch und klicken auf eine Schaltfläche.
- Unterschiede zwischen Scan- und CAD-Daten können farblich dargestellt werden. Die visuell leicht verständlichen Daten ermöglichen eine direkte Umsetzung von Gegenmaßnahmen bei Gussdefekten.
- Mehrere Sätze von Messdaten können einfach und quantitativ verglichen und analysiert werden.
- OK/n.i.O.-Produktbeurteilungen sind möglich. Die Daten können zur schnellen Analyse von n.i.O.-Produkten gemeinsam genutzt werden.
Die Modellreihe VL ermöglicht erhebliche Effizienzsteigerungen bei Messungen, Fehleranalysen und der Durchführung von Gegenmaßnahmen.