Messung von Verformungen nach der Wärmebehandlung
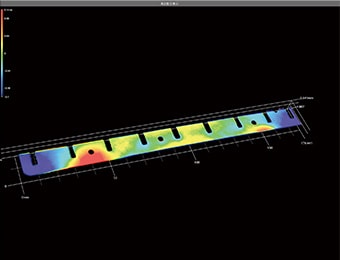
Im Allgemeinen ist die Wärmebehandlung ein Prozess, bei dem Materialien oder Produkte mit Wärme behandelt werden. Die Wärmebehandlung umfasst die Verarbeitung von metallischen Materialien durch Erhitzung sowie die Hitzesterilisation von Lebensmitteln und anderen Produkten. Dieser Abschnitt befasst sich mit der Verformung von Metall durch den Wärmebehandlungsprozess. Während die aus der Wärmebehandlung resultierende Verformung einfach sein kann, wie z. B. Kompression oder Verformung bei quadratischen Balken und Stäben, kann es bei Produkten mit komplexen Formen zu dreidimensionalen Verformungen kommen. Dies erfordert fortschrittliche Technologien zur Messung dieser Formen.
Auf dieser Seite werden grundlegende Kenntnisse über Verformungen durch Wärmebehandlungen erläutert, die bei Eisen oder Stahl zur Kontrolle ihrer Strukturen und zur Verbesserung ihrer Eigenschaften eingesetzt werden. Darüber hinaus werden Herausforderungen bei der Messung von Verformungen und einige mögliche Lösungen vorgestellt.
- Wärmebehandlung von Metall
- Beispiele für Verformungen durch Wärmebehandlung (Volumenänderung durch Phasenumwandlung)
- Maßnahmen zur Vermeidung von Verformungsproblemen durch Wärmebehandlung
- Herausforderungen bei gängigen Messungen von Verformungen nach der Wärmebehandlung
- Lösung für Herausforderungen bei der Messung von Verformungen nach der Wärmebehandlung
- Zusammenfassung: Erhebliche Verbesserungen bei der Messung von Verformungen nach der Wärmebehandlung
Wärmebehandlung von Metall
Die Wärmebehandlung von Metallen ist eine Verarbeitungstechnik, bei der ein Metall erhitzt und abgekühlt wird, um seine Eigenschaften zu verändern, ohne seine Form zu verändern. Zu den zu modifizierenden Eigenschaften gehören Festigkeit, Härte, Robustheit, Stoßfestigkeit, Verschleißfestigkeit, Korrosionsbeständigkeit, Bearbeitungseigenschaften und Kaltumformbarkeit.
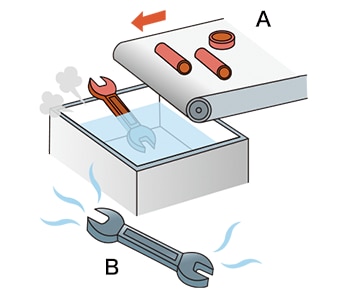
- A
- Erhitzen (bis das Metall rot wird)
- B
- Abkühlen (bis das erhitzte Metall schwarz wird)
Beispiele für Verformungen durch Wärmebehandlung (Volumenänderung durch Phasenumwandlung)
Es gibt mehrere Wärmebehandlungsmethoden, darunter Abschrecken, Anlassen, Glühen und Normalisieren. Während dieser Prozesse tritt ein Phänomen auf, das als Phasenumwandlung bekannt ist.
Die Phasenumwandlung tritt während der Wärmebehandlung auf, wenn sich ein Metall von einem festen in einen flüssigen Zustand und dann wieder von einem flüssigen in einen festen Zustand umwandelt. Dies geschieht, weil sich die aktuelle Form (Struktur) des Metalls ändert, wenn sich sein Kristallgitter aufgrund der Temperatur verändert. Wenn sich die Struktur während der Phasenumwandlung ändert, ändert sich auch das Volumen, was zu Verformungen führt.
Wenn zum Beispiel eutektoider Stahl, der etwa 0,8% Kohlenstoff enthält, von Raumtemperatur aus erhitzt wird, um eine Austenitstruktur zu erzeugen, und dann abgekühlt wird, verformt er sich aufgrund der Strukturänderung. Die Struktur nach der Phasenumwandlung variiert je nach Abkühlungsmethode, und daher beeinflusst die Abkühlungsmethode auch das Ausmaß der Verformung.
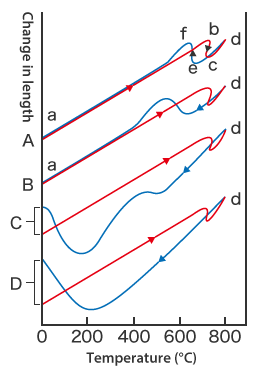
Diese Grafik zeigt die Unterschiede in der Verformung, die sich aus den verschiedenen Abkühlungsmethoden ergeben.
Im Fall von A dehnt sich das Metall beim Erhitzen aus (a → b) und Änderungen seiner Abmessungen aufgrund von Phasenumwandlungen sind bei etwa 750°C während des Erhitzens (b → c) und bei etwa 730°C während des Abkühlens (e → f) zu erkennen.
In C (Ölkühlung) und D (Wasserkühlung) gibt es eine deutliche Längenänderung nach der Kühlung.
- A: Ofenkühlung (langsame Kühlung)
- Das Metall bleibt nach dem Erhitzen im Ofen und kühlt ab, während es sich im Ofen befindet. Diese Methode kühlt das Metall mit einer Geschwindigkeit von etwa 30°C pro Stunde. Die Struktur nach der Phasenumwandlung ist Perlit.
- B: Luftkühlung
- Das Metall wird nach dem Erhitzen aus dem Ofen genommen und kühlt bei Raumtemperatur ab. Die Struktur nach der Phasenumwandlung ist Sorbit.
- C: Ölkühlung
- Das erhitzte Metall wird in Öl abgekühlt. Normalerweise wird das Metall in Öl bei etwa 60 bis 80°C abgekühlt. In der Struktur nach der Phasenumwandlung wird ein Teil der Austenitstruktur in Troostit umgewandelt.
- D: Wasserkühlung
- Das Metall wird in Wasser bei etwa 40°C abgekühlt. Die Struktur nach der Phasenumwandlung ist Martensit.
Maßnahmen zur Vermeidung von Verformungsproblemen durch Wärmebehandlung
Neben der im vorigen Abschnitt beschriebenen Phasenumwandlung gibt es weitere Gründe für Verformungsprobleme, die durch die Wärmebehandlung verursacht werden, wie z. B. eine falsche oder ungleichmäßige Oberflächenform oder die Erhitzung/Abkühlung. In diesem Abschnitt werden diese Verformungsprobleme, ihre Ursachen und Maßnahmen zu ihrer Vermeidung erläutert.
Risse nach dem Abschrecken
Dies ist eine Herausforderung, bei dem Materialrisse auftreten. Sie können am Tag nach dem Abschrecken auftreten oder später, nachdem das Material auf etwa 200°C oder darunter abgekühlt wurde.
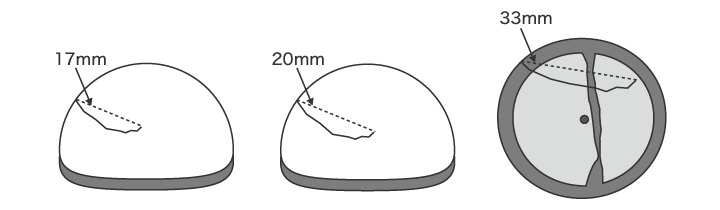
- Ursachen:
- Mögliche Ursachen sind Formfehler, die durch Volumenausdehnung aufgrund ungleichmäßiger Erhitzung oder Abkühlung, unsachgemäßes Anlassen unmittelbar nach dem Abschrecken und eine zu hohe Abschrecktemperatur verursacht werden.
- Gegenmaßnahmen:
-
- Überprüfen Sie die Produktform und die Oberflächenbeschaffenheit.
- Kühlen Sie abgeschreckte Materialien nicht auf etwa 200°C oder darunter ab.
- Führen Sie das Anlassen von Materialien unmittelbar nach dem Abschrecken durch.
- Senken Sie die Abschreckungstemperatur.
Schleifrisse
Dabei handelt es sich um eine Herausforderung, bei dem es zu Rissen im Stahlmaterial kommt, wenn es nach der Wärmebehandlung geschliffen wird. Es gibt zwei Arten von Schleifrissen: Schleifrisse vom Typ 1, die auftreten, wenn eine durch Schneiden, Polieren oder andere Verfahren bearbeitete Oberfläche etwa 100°C erreicht, und Schleifrisse vom Typ 2, die auftreten, wenn eine durch Schneiden, Polieren oder andere Verfahren bearbeitete Oberfläche etwa 300°C erreicht.
-
Schleifriss Typ 1
-
Schleifriss Typ 2
- Ursachen:
- Restaustenit dehnt sich aus, wenn er sich in Martensit umwandelt. Die durch diese Ausdehnung verursachte Spannung führt zur Rissbildung im Material. Diese Verformung kann auch auftreten, wenn eine durch Schneiden, Polieren oder andere Verfahren bearbeitete Oberfläche etwa 650 bis 850°C erreicht.
- Gegenmaßnahmen:
-
- Führen Sie das Anlassen angemessen durch.
- Reduzieren Sie die durch die Schleifreibung erzeugte Hitze.
Verformungen nach dem Abschrecken
Es gibt zwei Arten von Stahlverformungen, die durch die Wärmebehandlung verursacht werden: thermische Verformung durch thermische Ausdehnung oder Kontraktion beim Abschrecken oder Anlassen und eine Volumenveränderung durch Phasenumwandlung.
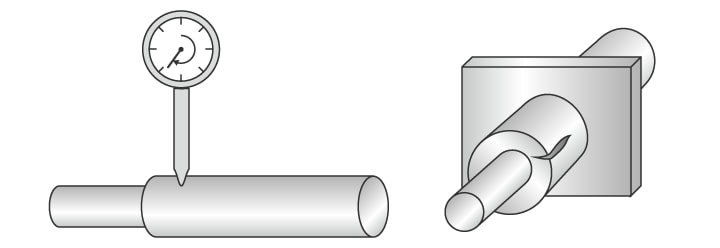
- Ursachen:
- Diese Verformung entsteht durch ungleichmäßige oder schnelle Erhitzung bzw. Kühlung oder durch Stellen mit ungleicher Dicke. Wenn ein Material eine komplexe Form hat, kann auch eine ungleichmäßige Temperaturverteilung im Material diese Verformung verursachen.
- Gegenmaßnahmen:
-
- Überprüfen Sie die Form, damit das Produkt gleichmäßig erhitzt und abgekühlt werden kann.
- Reduzieren Sie die Geschwindigkeit der Erhitzung und Kühlung.
Herausforderungen bei gängigen Messungen von Verformungen nach der Wärmebehandlung
Es ist sehr wichtig zu überprüfen, ob die Abmessungen und Formen nach der Wärmebehandlung innerhalb der Toleranzen liegen. Vor allem Produkte mit komplexen Formen erfordern eine hochpräzise, quantitative Messung der 3D-Form.
Bei gängigen Messungen von Verformungen nach der Wärmebehandlung werden Profilmesssysteme oder 3D-Koordinatenmessgeräte verwendet. Bei der Messung mit bisher verwendeten 3D-Koordinatenmessgeräten oder Profilmesssystemen gibt es jedoch verschiedene Herausforderungen. Dazu gehören die Expertise, die erforderlich ist, um genaue Messungen zu erhalten, und die Schwankungen der Messwerte.
Herausforderungen bei der Messung von Verformungen mit einem Profilmesssystem
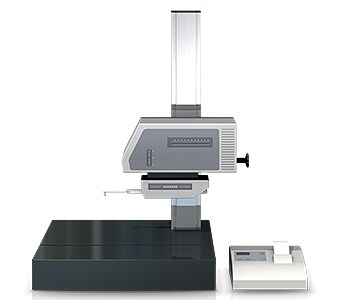
Ein Profilmesssystem oder Konturograph misst und erfasst das Profil eines Messobjekts, indem es dessen Oberfläche mit einem Taststift nachfährt. In den letzten Jahren wurden Profilmesssysteme entwickelt, die mit einem Laser anstelle eines Taststifts komplexe Formen messen, indem sie das Profil berührungslos verfolgen. Einige Modelle sind sogar in der Lage, Messungen sowohl der Ober- als auch der Unterseite durchzuführen.
Bei einem Profilmesssystem ist es jedoch erforderlich, präzise Messlinien für die Messpunkte zu erfassen.
Dies beinhaltet die folgenden Herausforderungen:
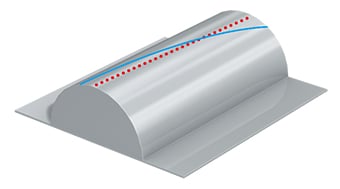
- Die Messung erfordert viel Zeit, einschließlich der Zeit für die Befestigung des Messobjekts auf der Vorrichtung und deren Nivellierung. Es sind zudem Kenntnisse und Fähigkeiten im Umgang mit Profilmesssystemen erforderlich, um ein Messobjekt genau zu nivellieren.
- Der Taststift eines Profilmesssystems bewegt sich in einem Bogen auf und ab, der auf dem Drehpunkt des Tastarmes zentriert ist, und auch die Tastspitze bewegt sich in Richtung der X-Achse. Dies führt zu Fehlern in den Daten auf der X-Achse.
- Das Nachzeichnen der gewünschten Linie mit dem Taststift ist eine äußerst schwierige Arbeit, und selbst eine leichte Verschiebung des Taststifts führt zu Fehlern in den Messungen.
- Es ist auch schwierig, die Anzahl der Messobjekte zu erhöhen, weil man bestimmte Positionen für die Messung festlegen muss.
- Es kann nur eine Stelle eines Messobjekts gemessen werden, und die Auswertung der gesamten Oberfläche ist nicht möglich.
Herausforderungen bei der Messung von Verformungen mit einem 3D-Koordinatenmessgerät
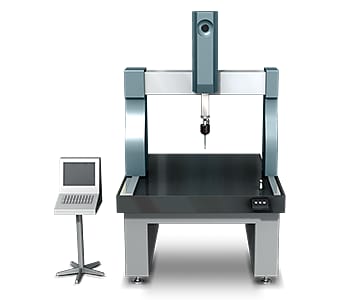
Handelsübliche 3D-Koordinatenmessgeräte verwenden einen Messtaster, der eine Oberfläche abtastet oder abfährt und mehrere Datenpunkte in einem bestimmten Abstand sammelt.
Diese Messung bringt folgende Herausforderungen mit sich:
- Die Sicherstellung, dass sich der Messtaster wie vorgesehen bewegt, ist eine äußerst schwierige Aufgabe, insbesondere bei Geraden entlang der Mitte eines Zylinders oder einer gekrümmten Oberfläche oder bei Linien, die durch den Mittelpunkt eines Kreises verlaufen. Wenn eine Hohlkehle oder Rundung einen weiten Mittelpunktswinkel hat, hat selbst ein kleiner Fehler in der Messung starke Auswirkungen, da der gesamte Kreis auf der Grundlage eines kurzen Kreissegments berechnet wird. Derartige Ungenauigkeiten bei den Messpunkten können zu unterschiedlichen Messwerten führen.
- Wenn eine kleine 3D-Form gemessen wird, kann es sein, dass der Messtaster die Messpunkte nicht berühren kann. Da sich die Genauigkeit der Messung proportional zur Anzahl der gemessenen Punkte oder Linien verhält, ist es notwendig, eine große Anzahl von Punkten oder Linien zu messen.
So ist die Messung mit einem 3D-Koordinatenmessgerät mit erheblichen Herausforderungen verbunden. Dazu gehören fehlende Fachkenntnisse der Anwender, das Vorhandensein von Messobjekten, die überhaupt nicht gemessen werden können, und begrenzte Standorte, an denen das System installiert werden kann.
Lösung für Herausforderungen bei der Messung von Verformungen nach der Wärmebehandlung
Diese Messsysteme können Herausforderungen mit der Positionierung eines Messobjekts oder einer Tastspitze haben und demnach Schwierigkeiten bei der Bereitstellung von Gesamtmessdaten einer 3D-Oberfläche verursachen, da lediglich nach Punkten oder Linien gemessen wird. Um diese Herausforderungen zu lösen, hat KEYENCE das 3D-Profilometer der Modellreihe VR entwickelt.
Die Modellreihe VR erfasst präzise die 3D-Form der gesamten Oberfläche in wenigen Sekunden, ohne das Messobjekt zu berühren. Das System ist in der Lage, eine gesamte 3D-Oberfläche sofort und präzise zu quantifizieren und dabei keine Messfehler zu verursachen. In diesem Abschnitt werden einige Vorteile der Modellreihe VR vorgestellt.
Vorteil 1: Messung einer großen Anzahl von Punkten in nur einer Sekunde
Die Modellreihe VR erfasst die für die 3D-Form des Messobjekts erforderlichen Oberflächendaten in nur einer Sekunde, was die für die Messung einer großen Anzahl von Punkten erforderliche Zeit erheblich reduziert. Sie misst die maximalen und minimalen Unregelmäßigkeiten auf der gesamten Messobjektoberfläche und ermöglicht so eine schnelle Beurteilung aller Positionen auf der Grundlage der voreingestellten Toleranz.
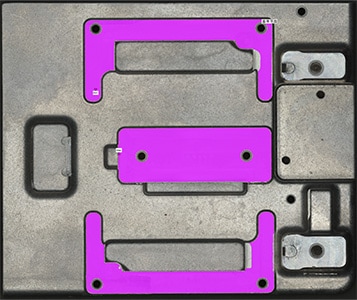
Sobald ein Werkstück gescannt wurde, kann sein Profil (Querschnitt) auch an anderen als den in der Vergangenheit gemessen Stellen gemessen werden. Dadurch muss dasselbe Messobjekt nicht mehr erneut eingestellt und gemessen werden.
Vorteil 2: Messdaten können mit Bezugsdaten verglichen werden
Die Modellreihe VR kann mehr als nur effizient Daten sammeln. Messdaten können in einer Liste angezeigt werden und derselbe Analyseinhalt kann auf alle Daten gleichzeitig angewendet werden.
Es ist möglich, die Unterschiede in den Daten, die durch die Messung mehrerer Messobjekte vor und nach der Wärmebehandlung gewonnen wurden, sowie die Höhe des Unterschieds bei mangelhaften Produkten im Vergleich zum Referenzprodukt schnell zu überprüfen. Dies ermöglicht eine einfache quantitative Analyse und Beurteilung der durch die Wärmebehandlung verursachten Verformung.
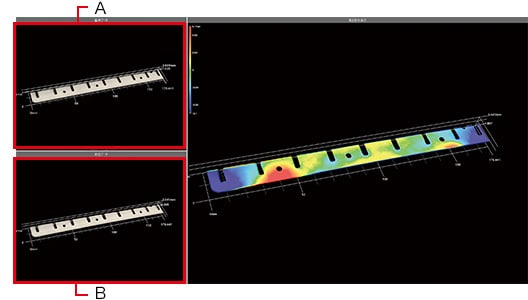
- A
- Referenzdaten
- B
- Messdaten
Die Modellreihe VR kann Messobjekte mit komplexen Formen schnell messen, was früher viel Zeit und Arbeit erforderte. Die Daten werden nicht nur schnell erfasst – alle Messergebnisse liegen in digitaler Form vor, was den Arbeitsaufwand für den Datenvergleich und die Analyse erheblich reduziert.
Zusammenfassung: Erhebliche Verbesserungen bei der Messung von Verformungen nach der Wärmebehandlung
Bisher nahm die Messung von durch Wärmebehandlung verursachten Verformungen viel Zeit in Anspruch, was die Anzahl der Proben, die gemessen werden konnten, begrenzte. In einigen Fällen war eine Messung aufgrund der komplexen Form des Messobjekts überhaupt nicht möglich. Die Modellreihe VR ist jedoch in der Lage, diese Verformungen schnell zu messen und zu quantifizieren. Dadurch kann die Modellreihe VR die Produktqualität mit einem höheren Maß an Genauigkeit und Effizienz beurteilen.
- Der Zeitaufwand für die Messung komplexer Formen kann erheblich reduziert werden, indem die gesamten Oberflächendaten gleichzeitig erfasst werden.
- Durch die Erfassung und den Vergleich mehrerer Messdatensätze können verschiedene Unterschiede in der Verformung leicht identifiziert und analysiert werden.
- Eine echte quantitative Messung ist möglich, was Abweichungen der Ergebnisse aufgrund menschlicher Fehler ausschließt.
- Legen Sie das Messobjekt einfach auf den Objekttisch und betätigen Sie eine Taste, um genaue Daten zu erfassen. Es sind keine speziellen Fachkenntnisse nötig, da keine Positionierung oder sonstige Vorbereitung durchzuführen ist.
- Dank der hohen Abtastgeschwindigkeit kann eine große Anzahl an Messobjekten in kürzester Zeit gemessen werden.
Die Modellreihe VR ist zudem in der Lage, Daten mit früheren Scans und CAD-Modellen zu vergleichen und die Rauheit zu analysieren.