Messung und Analyse der 3D-Form von verzogenen Leiterplatten
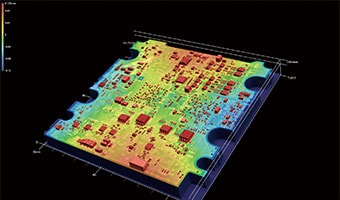
Bei der Montage von elektronischen Komponenten und Systemen werden die Leiterplatten durch das Bonding und die Erhitzung während des Reflow-Prozesses belastet. Durch den Reflow-Prozess wird eine effiziente Komponentenbestückung ermöglicht, allerdings kann die Belastung durch die Erhitzung zu einer Verformung der Leiterplatte führen, wie z. B. Wölbung, Welligkeit oder Dehnung. Wenn eine Leiterplatte verformt wird, kann sich die Festigkeit der Verbindung von Komponenten oder die Einpassung in das Gehäuse verschlechtern, was zu einer ernsthaften Beeinträchtigung der Produktionsquote führt.
In diesem Abschnitt werden grundlegende Kenntnisse über die Verformung von Leiterplatten, Herausforderungen bei der Messung von Verformungen und die neuesten Messmethoden erläutert.
- Verformung von Leiterplatten
- Simulationsanalyse und Beurteilung von verformten Leiterplatten
- Schwierigkeiten bei der Messung und Beurteilung von verformten Leiterplatten
- Lösungen zur Messung von verformten Leiterplatten
- Zusammenfassung: Erhebliche Verbesserung und höhere Effizienz bei der Messung von verformten Leiterplatten
Verformung von Leiterplatten
Die Oberfläche einer Leiterplatte sollte eben sein, damit die Komponenten korrekt montiert werden können. Es kann jedoch zu Verformungen wie Wölbung oder Krümmung aufgrund übermäßiger, durch Hitze verursachter Belastung kommen. Die Gründe, warum die Verformung von Leiterplatten zunehmend zu einer Herausforderung geworden ist und die Auswirkungen der Verformung werden im Folgenden erläutert.
Verformung der Leiterplatte durch Hitze
Aufgrund der mehrschichtigen und immer kompakteren Bauweisen von Leiterplatten, auf denen elektronische Komponenten montiert werden, sowie der Fortschritte bei der dichten Montage hat sich der Reflow-Prozess als gängigste Methode für die Komponentenbestückung durchgesetzt. Beim Reflow-Prozess wird Lötpaste auf die gewünschten Stellen gedruckt und Klebemittel zur Fixierung der Komponenten aufgetragen. Anschließend werden die elektronischen Komponenten vom Bestückungsautomat auf die Leiterplatte gesetzt. Die Leiterplatte wird dann in einem Ofen erhitzt, um das Lot oder Klebemittel zu härten, was eine effiziente Komponentenbestückung ermöglicht.
Durch die Einführung von bleifreiem Weichlot aus Umweltschutzgründen sind jetzt höhere Temperaturen als bisher für das Schmelzen des Lots im Reflow-Prozess erforderlich. Die höheren Temperaturen im Reflow-Ofen erhöhen die hitzebedingte Belastung der Leiterplatten. Dies hat zu vermehrten Herausforderungen wie Wölbung oder Krümmung der Leiterplatten im Hochtemperaturofen geführt.
Auswirkungen der Verformung von Leiterplatten
Die Verformung von Leiterplatten kann zu Herausforderungen führen, wie z. B. fehlerhaftem Weichlöten aufgrund von Positionsabweichungen oder Verbindungsfehlern aufgrund von Spannungen an gelöteten Stellen. Wenn die Verformung groß ist, kann die Passgenauigkeit beim Einsetzen der Leiterplatte in das Gehäuse beeinträchtigt werden. Diese Mängel können die Produktionsquote erheblich verringern.
Wenn eine Stelle der Leiterplatte oder die gesamte Leiterplatte leicht verformt ist und in das Gehäuse eingebaut und versandt wurde, kann es später zu Fehlfunktionen des Produkts aufgrund von Verbindungsfehlern der elektronischen Komponenten kommen, die zu Beschwerden der Anwender führen. Insbesondere Steuerplatinen, die in Automobilen oder Flugzeugen verwendet werden, erfordern eine hochpräzise Qualitätskontrolle, da jede Fehlfunktion schwerwiegende Folgen haben kann. Daher ist die Form der Leiterplatte ein wichtiger Prüfpunkt, ebenso wie die Anhebung von Anschlussstiften und Lötkegelformen.
Simulationsanalyse und Beurteilung von verformten Leiterplatten
Um eine Verformung der Leiterplatten zu vermeiden, müssen die Erhitzungsbedingungen in jeder Phase berücksichtigt, überprüft und beurteilt werden. Dies muss sowohl bei der Konstruktion als auch bei der Beurteilung der Erhitzung selbst geschehen.
Simulationsanalyse der Verformung mit Software
In der Konstruktionsphase der Leiterplatte kann eine Simulationsanalyse mit CAD-Daten durchgeführt werden. Eine Methode zur Simulation und Beurteilung des Verhaltens eines sich verformenden Objekts ist die FEM (Finite-Elemente-Methode).
FEM (Finite-Elemente-Methode)
Die Finite-Elemente-Methode (FEM) ist eine Simulationsanalysemethode, bei der eine komplexe Form in Formelemente unterteilt wird, bis sie zu einem Aggregat einfacher Formen wird, und dann die Belastung und Verformung für jedes einfache Formelement ermittelt wird. Durch das Stapeln der einzelnen einfachen Formen, um die gesamte Originalstruktur nachzubilden, können Belastung und Verformung für jede Stelle des gesamten Messobjekts vorhergesagt werden. Durch die Verwendung von CAD-Daten des Prüfobjekts in einer Computersoftware ist es möglich, Simulationsanalysen für Faktoren wie Steifigkeit, Festigkeit, Vibrationsbeständigkeit, plastische Verformung, Bruch und Wärmeverformung durchzuführen.
Elemente werden nach ihrer Form klassifiziert (siehe unten).
0-dimensionales Element (Skalar) |
![]() |
||
---|---|---|---|
1-dimensionales Element (Balken) |
![]() |
||
2-dimensionales Element (Dreieck- und Viereckelement) |
![]() |
![]() |
|
3-dimensionales Element (räumliche Form) |
![]() |
![]() |
![]() |
- 0-dimensionales Element (Skalar): Ein Punkt, der keine Form hat.
- 1-dimensionales Element (Balken): Eine Linie, die verwendet wird, um eine Form wie einen Stab, eine Säule oder einen Balken darzustellen.
- 2-dimensionales Element (Dreieck- und Viereckelement): Eine Ebene, die verwendet wird, um dünne Bleche und ähnliche Messobjekte darzustellen.
- 3-dimensionales Element (räumliche Form): Es gibt drei Arten von räumlichen Elementen. In der Reihenfolge von links nach rechts sind dies das pyramidenförmige Tetra-Element, das dreieckige stabförmige Penta-Element und das kubische Hexa-Element. Die Verwendung einer größeren Anzahl von Hexa-Elementen kann die Analysegenauigkeit für dicke Objekte erhöhen, allerdings ist der Schwierigkeitsgrad hoch und es wird viel Rechenzeit benötigt. Andererseits haben die Fortschritte in der Technologie zur automatischen Erstellung eines 3D-Elementnetzes unter Verwendung von Tetra-Elementen die Berechnungszeiten verkürzt, und diese Methode ist geeignet, wenn Zeitersparnis Vorrang vor Genauigkeit hat.
Hauptmerkmale und Ablauf der Simulationsanalyse
Da kleinere Abmessungen die Anzahl der benötigten Formen reduzieren, ist die für die Analyse benötigte Zeit kürzer. Wenn die Größe der Abmessungen zunimmt, wird zwar mehr Zeit benötigt, aber es können präzisere Daten gewonnen werden. Im normalen Ablauf der Verformungssimulation einer 3D-Leiterplatte werden zunächst die Konstruktionsdaten der Leiterplatte in ein Netz unterteilt. Obwohl fast alle Konstruktionsdaten der Leiterplatte in 2D vorliegen, erfordert manche Software eine Konvertierung in das CAD-Format. Für jedes Element des Netzes wird eine Belastung erzeugt, indem die Temperatur virtuell erhöht wird, wie es im Temperaturprofil des Reflow-Prozesses vorgeschrieben ist, und die simulierten Daten werden erfasst.
Anforderungen für den Leiterplatten-Erhitzungstest und die eigentliche Messung/Beurteilung
Nach der Simulation müssen Sie die Leiterplatte in einen tatsächlichen Reflow-Ofen stellen, um zu überprüfen, ob sie sich unter dem vorgeschlagenen Temperaturprofil genauso verhält wie in der Simulation.
Es hängt zwar von der Größe ab, aber wenn eine Leiterplatte mit der Finite-Elemente-Methode in 3-dimensionale Elemente unterteilt wird, kann die Anzahl der Elemente etwa 50.000 erreichen. Das bedeutet, dass ohne eine präzise Messung der gesamten Oberflächenform der Leiterplatte keine korrekten Prüfergebnisse erzielt werden können, egal wie detailliert die Simulationsanalyse ist. Die eigentliche Messung ist ein sehr wichtiger Prozess, um sicherzustellen, dass alle Punkte, die in der Konstruktionsphase verbessert werden müssen, identifiziert werden.
Nachfolgend erläutern wir die Herausforderungen bei der Messung mit handelsüblichen Messsystemen und stellen das neueste Messsystem vor, das die Beurteilung anhand von Vergleichen mit hochgenauen Computersimulationen durchführen kann.
Schwierigkeiten bei der Messung und Beurteilung von verformten Leiterplatten
Mit handelsüblichen Messsystemen ist es schwierig, die gesamte Leiterplattenform präzise zu messen. Daher ist es auch schwierig, die Form des Messobjekts und die Veränderungen, die sie erfährt, zu quantifizieren, selbst wenn fortschrittliche Simulationen und Experimente durchgeführt werden. Einige der Herausforderungen, auf die Anwender bei der Verwendung gängiger Messsysteme stoßen können, werden im Folgenden beschrieben.
Schwierigkeiten bei der Messung – Profilmesssystem
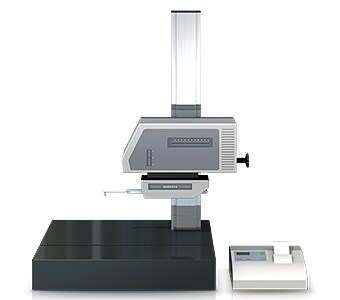
Ein Profilmesssystem misst und erfasst das Profil eines Messobjekts, indem es dessen Oberfläche mit einem Taststift nachfährt.
In den letzten Jahren wurden Profilmesssysteme entwickelt, die mit einem Laser anstelle eines Taststifts komplexe Formen messen, indem sie das Profil berührungslos verfolgen. Einige Modelle sind sogar in der Lage, Messungen sowohl der Ober- als auch der Unterseite durchzuführen.
Profilmesssysteme stehen bei der Messung von Leiterplattenverformungen vor den folgenden Herausforderungen:
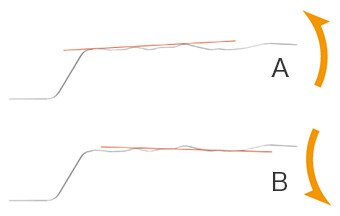
- A
- Neigung nach oben
- B
- Neigung nach unten
- Da das Messobjekt durch Abtasten entlang von Linien gemessen wird, ist es schwierig, die Verformung über eine große Fläche zu messen und zu bewerten.
- Es ist nicht möglich, die gesamte Oberflächenform des Messobjekts zu erkennen.
- Es ist schwierig, um die auf der Oberfläche montierten Komponenten herum zu messen.
- Das Festlegen einer Bezugsebene mit Hilfe von Linien ist schwierig, weshalb es zu Fehlern bei der Messung kommen kann (siehe Abbildung).
Schwierigkeiten bei der Messung – 3D-Koordinatenmessgerät
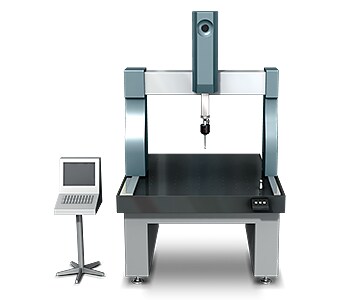
Bei der Messung von Leiterplattenverformungen mit einem 3D-Koordinatenmessgerät muss die Tastspitze in der Regel mindestens vier Ecken der Messobjektoberfläche berühren.
Bei einer Platte zum Beispiel werden üblicherweise sechs bis acht Punkte gemessen. Wenn die Messfläche groß ist, kann die Genauigkeit der Messung verbessert werden, indem die Anzahl der Messpunkte erhöht wird, um mehr Messdaten zu sammeln.
3D-Koordinatenmessgeräte stehen bei der Messung von Leiterplattenverformungen vor den folgenden Herausforderungen:
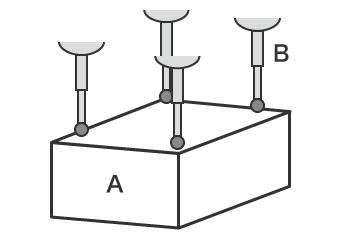
- A
- Messobjekt
- B
- Messtaster
- Da die Messung durch Kontakt an einer begrenzten Anzahl von Punkten erfolgen muss, ist es schwierig, die gesamte Form des Messobjekts zu erkennen.
- Die Messung von mehr Punkten, um mehr Messdaten zu erhalten, erfordert viel Zeit. Dennoch ist es nicht möglich, die detaillierte Form des gesamten Messobjekts und die Positionen von Oberflächenunregelmäßigkeiten zu erkennen.
Lösungen zur Messung von verformten Leiterplatten
Handelsübliche Messsysteme messen Formen nur anhand von Linien oder Punkten und können die gesamte Form einer verformten Leiterplatte nicht identifizieren. Außerdem ist es schwierig, für jede Oberflächenunregelmäßigkeit auf dem gesamten Messobjekt die Höchst- und Tiefstwerte zu ermitteln oder schnell quantitative Vergleiche anzustellen.
Um diese Messherausforderungen zu lösen, hat KEYENCE das 3D-Profilometer der Modellreihe VR entwickelt.
Die Modellreihe VR erfasst präzise die 3D-Form der gesamten Oberfläche, ohne das Messobjekt zu berühren. Die Modellreihe VR erfordert keine speziellen Vorrichtungen oder subjektive Entscheidungen, sodass unabhängig vom Anwender genaue Messungen durchgeführt werden können.
Vorteil 1: Datenerfassung über die gesamte Oberfläche in einer Sekunde
Die Modellreihe VR kann mit einer einzigen berührungslosen Messung in nur einer Sekunde die Oberflächendaten erfassen. Die maximalen und minimalen Oberflächenunregelmäßigkeiten (Höhe, Tiefe) in der erfassten 3D-Form können in einer Farbkarte angezeigt werden, um verformte Stellen auf dem gesamten Messobjekt zu visualisieren.
Da die Daten über die gesamte Oberfläche erfasst werden, können an jeder beliebigen Stelle Profillinien gezeichnet werden, um die Höhenänderungen zu visualisieren und zu quantifizieren.
Die Messdaten können auch überlagert und mit CAD-Daten oder Scandaten von der Leiterplatte vor dem Erhitzen verglichen werden, sodass die Verformungen vollständig erkannt werden können.
Dies führt zu einer erheblichen Reduzierung des Zeitaufwands und einer Verbesserung der Arbeitseffizienz sowie zu genauen Messungen, Vergleichen und Beurteilungen.
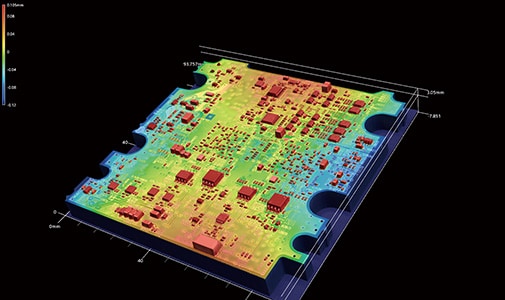
Vorteil 2: Einfache Messung
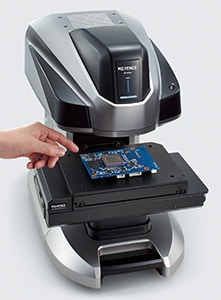
Die Messung von 3D-Formen kann ganz einfach durchgeführt werden, indem Sie das Messobjekt auf den Objekttisch legen und eine Taste betätigen.
Durch Umschalten zwischen den Kameras mit geringer und starker Vergrößerung kann eine genaue Messung der gesamten Leiterplatte oder detaillierter Stellen mit einem einzigen System durchgeführt werden, selbst bei kleinen Leiterplatten.
Die Modellreihe VR verfügt über die neue „Smart Measurement“-Funktion, die die Größe und Oberflächenbeschaffenheit der Leiterplatte erkennt und den Scanbereich und die Bedingungen automatisch so konfiguriert, dass die gesamte Leiterplattenoberfläche erfasst wird.
Eine Vielzahl von integrierten Hilfswerkzeugen ermöglicht es selbst unerfahrenen Anwendern, genaue und reproduzierbare Messungen durchzuführen. So lässt sich die Anzahl der gemessenen Proben leicht erhöhen und eine Trendanalyse durchführen, nicht nur für Verifizierungstests und die Bewertung von Konstruktionen und Simulationen, sondern auch für Messungen und Prüfungen während der Serienproduktion.
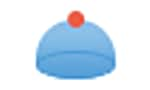
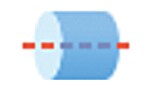
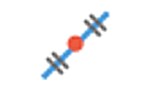
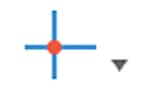
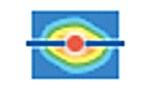

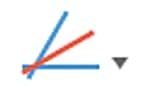
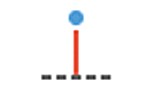
Zusammenfassung: Erhebliche Verbesserung und höhere Effizienz bei der Messung von verformten Leiterplatten
Die Modellreihe VR kann 3D-Messobjekte präzise und mit hoher Geschwindigkeit messen, ohne das Messobjekt zu berühren. Neben der Messung der 3D-Abmessungen der gesamten Leiterplatte können so auch bisher schwierige Arbeiten wie die Messung der Formen kleinster Höhen- und Oberflächenunregelmäßigkeiten und der Vergleich mehrerer Datensätze schnell erledigt werden.
Die Modellreihe VR löst viele Herausforderungen, die bei gängigen Messsystemen auftreten können.
- Höhenunterschiede über das gesamte Messobjekt können in der Farbkarte visualisiert werden.
- Vergleichen Sie mühelos mehrere Messdatensätze und wenden Sie Bedingungen auf mehrere Datensätze gleichzeitig an, um die Arbeitseffizienz erheblich zu verbessern.
- Sobald ein Scan abgeschlossen ist, können Sie jederzeit eine Profilmessung an einer beliebigen Stelle des Messobjekts und einen Vergleich mehrerer Datensätze durchführen.
- Es sind weder Positionierung noch andere Vorbereitungen erforderlich: Die Messung kann einfach durch Auflegen des Messobjekts auf den Objekttisch und Betätigen einer Taste durchgeführt werden. Damit muss für die Messung kein Fachpersonal mehr herangezogen werden.
- Da 3D-Formen mit hoher Geschwindigkeit und Genauigkeit gemessen werden können, ist die Messung einer großen Anzahl von Proben in kurzer Zeit möglich. Dies ist nützlich für Qualitätsverbesserungen.
Neben Forschung und Entwicklung, Design und Tests kann das System in einer Vielzahl von Situationen an Arbeitsplätzen bei der Verarbeitung von elektronischen Produkten effektiv eingesetzt werden, z. B. bei Stichprobenprüfungen nach Beginn der Massenproduktion und bei der Ursachenanalyse, wenn Fehler auftreten.