Törési felületek értékelése Charpy-féle ütővizsgálatokból
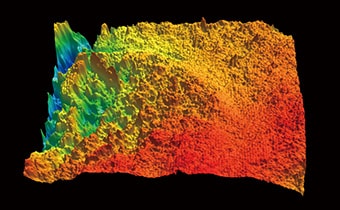
Az ütési tesztek olyan anyagvizsgálatok, amelyeket az anyagok keménységének és ridegségének meghatározására végeznek, amikor ütésnek vannak kitéve. Az ütési tesztek közé tartozik a Charpy-féle ingás ütővizsgálat, az Izod-féle ütőszilárdsági vizsgálat, a szakítószilárdsági teszt, a leeső golyós (súlyos) ütésvizsgálat, a Du Pont-féle ütésvizsgálat és a szúrással szembeni ellenállás vizsgálat. Az ipari területeken alkalmazott tesztek a Charpy-féle ütővizsgálat és az Izod-féle ütőszilárdsági vizsgálat.
A Charpy-féle ütővizsgálat azon anyagok esetében különösen fontos, amelyeket erős ütésnek vagy nagy nyomásnak kitett alkatrészekben használnak, például az atomerőművek energiatermelő egységeiben és csővezetékeiben.
Ez az oldal a Charpy-féle ütővizsgálattal és a próbadarabokkal kapcsolatos alapvető ismereteket, valamint a vizsgálati eredmények értékelését írja le. Emellett bemutatja a vizsgálati eredmények kiértékelésével és a hagyományos mérési módszerekkel kapcsolatos problémákat, valamint megoldást kínál azokra.
- Charpy-féle ütővizsgálat
- Charpy-féle ütővizsgálat-értékelések
- A Charpy-féle ütővizsgálatban használt próbadarabok
- A hagyományos törésfelület-mérés során felmerülő problémák
- Törésfelület-mérési megoldások
- Összegzés: Töredezett felületek mennyiségi mérése
Charpy-féle ütővizsgálat
A Charpy-féle ütővizsgálat során a próbadarabra ütési terhelést fejtenek ki egy inga kalapáccsal, hogy eltörjön. Az ütési érték a próbadarab eltörésekor mérhető energiából származik, és a próbadarab anyagának keménységének és ridegségének értékelésére szolgál.
Ha a kalapács nagy szögben lendül a próbadarab törése után, az azt jelzi, hogy a próbadarab nem tudta elnyelni az ütést. Ha a kalapács alacsony szögben lendül, az azt jelzi, hogy a próbadarab többet nyelt el az ütésből.
A nagyobb ütést elnyelő próbadarab-anyag az ütési szilárdság szempontjából jobbnak tekinthető. Ha a kalapács lengésszöge elő van írva, akkor ha a kalapács mért lengési szöge nagyobb, mint az előírt szög, akkor az anyag nem felel meg a vizsgálatnak.
Charpy-féle ütővizsgálat-értékelések
A Charpy-féle ütővizsgálat azt a szöget méri, amelybe a kalapácsot kezdetben felemelték, és a kalapács tehetetlenségi lengésszögét a próbadarab törése után. A próbadarab törési felülete is értékelésre kerül, mert olyan információkat tartalmaz, amelyek jelzik, hogy a próbadarab hogyan tört el.
Az elnyelt energia értékelése a Charpy-féle ütővizsgálat során
A Charpy-féle ütővizsgálatot az elnyelt energia mennyiségének meghatározására használják, vagyis azt az energiát, amelyet a próbadarab törésére fordítottak. Ez az energia abból a szögből számítható, amelybe a kalapácsot eredetileg felemelték, és abból a szögből, amelybe a kalapács a szemközti oldalon fellendül a próbadarab törése után. Az alábbiakban egy Charpy-féle ütőmű sematikus nézete látható, valamint az elnyelt energia és a Charpy-féle ütőszilárdság kiszámításához használt képletek.
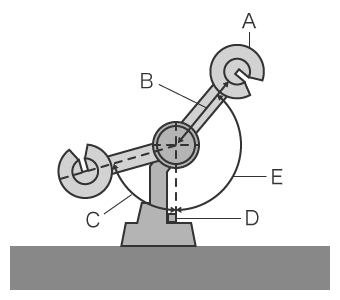
- A
- Kalapács
- B
- A kalapács forgási középpontja és a kalapács súlypontja közötti távolság (R)
- C
- Az a szög, amelybe a kalapács a próbadarab törése után elfordul (θβ)
- D
- Próbadarab (b: szélesség, h: vastagság)
- E
- Az a szög, amelybe a kalapácsot felemelik (θα)
<Képlet>
E = WR(cosθβ − cosθα) − L
a = E/bh
- E
- Elnyelt energia (J)
- a
- Charpy-féle ütőérték (kg-cm/cm2)
- W
- Kalapács súlya (N)
- R
- A kalapács forgástengelyének középpontja és a kalapács súlypontja közötti távolság (m)
- θβ
- Az a szög, amelybe a kalapács a próbadarab törése után elfordul (°)
- θα
- A kalapács emelési szöge (°)
- b
- Próbadarab szélessége (cm)
- h
- Próbadarab vastagsága (cm)
- L
- Súrlódás okozta energiaveszteség
A Charpy-féle ütővizsgálatban használt próbadarabok
A Charpy-féle ütővizsgálat során a következő próbadarabok használatosak. A próbadarabot ugyanabból az anyagból vágják ki, amelyet a termékben ténylegesen használnak.
Tesztmódszer | Próbadarab |
---|---|
Fémes anyagok Charpy-féle ütővizsgálati módszere | Charpy-féle ütővizsgálati próbadarab (V-bevágás, U-bevágás) |
Szénszállal erősített műanyagok Charpy-féle ütővizsgálati módszere | Próbadarab lap menti ütéshez Próbadarab él menti ütéshez |
Üvegszállal erősített műanyagok Charpy-féle ütővizsgálati módszere | Charpy-féle ütővizsgálati próbadarab |
Műanyagok – Charpy-féle ütési tulajdonságok meghatározása | Charpy-féle ütővizsgálati próbadarab |
Minden próbadarabnak van egy bemélyedése, amelyet bevágásnak neveznek, és amelyet a feszültség koncentrálására alakítanak ki. Kétféle bevágás létezik: V-bevágás és U-bevágás. Az él menti ütéshez használt próbadarabok eltérnek a lap menti ütéshez használtaktól. Az él menti ütést a próbadarab keskeny felületére, míg a lap menti ütést a próbadarab nagy felületére mérik. Az alábbi ábrák a próbadarabot és az ütés irányát mutatják, amikor a próbadarabot él menti ütés éri.
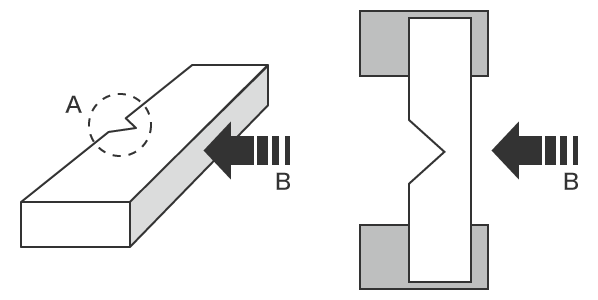
- A
- Bevágás
- B
- Ütés iránya (él menti módszer)
A törésfelület értékelése a Charpy-féle ütővizsgálat során
A Charpy-féle ütővizsgálat során eltört próbadarab törési felülete a hőmérséklettől függően eltérő törési jellemzőket mutat. A törésfelület megjelenésének a hőmérséklet-változásból eredő változását képlékeny-rideg átmenetnek nevezzük. A törésfelületeket rideg törésfelületek vagy képlékeny törésfelületek közé osztályozzuk. A rideg törésfelületek fényes ezüstfehér felületek. A képlékeny törésfelületek sötétszürke színűek, nagy alakváltozások és felületi egyenetlenségek jellemzik. A rideg törésfelület százalékos arányát a teljes törésfelülethez viszonyítva rideg törési százaléknak nevezzük. Ezzel szemben azt a százalékot, amelyet úgy kapunk meg, hogy a törésfelület 100%-ából kivonjuk a rideg törési százalékot, képlékeny törési százaléknak nevezzük.
Például, amikor egy anyagot alacsony hőmérsékleten tesztelnek, a próbadarab szinte mindig eltörik, miközben többnyire megőrzi eredeti négyzet alakú keresztmetszetét. A törésfelületen rideg törés látható, ami azt jelzi, hogy az elnyelt energia kicsi. Ha ugyanazt az anyagot magas hőmérsékleten tesztelik, képlékeny törésfelület képződik, és a rideg törési százalék alacsonyabb. Az elnyelt energia mennyisége is nő.
A fent leírtak szerint, a hőmérséklet és az elnyelt energia közötti összefüggés, valamint a keménység változása a Charpy-féle ütővizsgálat során a törési felületek felületén és érdességén látható. Ez a teszt ezért nagyon fontos ezeknek a tényezőknek a mennyiségi értékeléséhez.
A Charpy-féle ütővizsgálat és az Izod-féle ütőszilárdsági vizsgálat közötti különbségek
A Charpy-féle ütővizsgálat mellett az Izod-féle ütőszilárdsági vizsgálatot is gyakran használják az ipari területeken. Ezt az ütésvizsgálatot gyakran használják műanyagok esetében, mértékegysége a J/m. A két módszer különböző módon rögzíti a próbadarabokat. A Charpy-féle ütővizsgálat során a próbadarabot mindkét végén rögzítik, és az ütést a próbadarab közepére mérik. Az Izod-féle ütőszilárdsági vizsgálat során a próbadarabot az egyik végén rögzítik, és a másik végére mérik az ütést. A Charpy-féle ütővizsgálathoz hasonlóan az ütést kalapáccsal fejtik ki. A próbadarabot eltörő ütési szilárdság az elnyelt energiából számítható ki. A Charpy-féle ütővizsgálathoz hasonlóan, az elnyelt energiát a kalapács felemelési szögének és a kalapácsnak a próbadarab törése utáni tehetetlenség következtében mérhető fellendülési szögének mérésével kell meghatározni. Az Izod-féle ütőszilárdsága és az elnyelt energiája a következő képletekkel számítható ki.
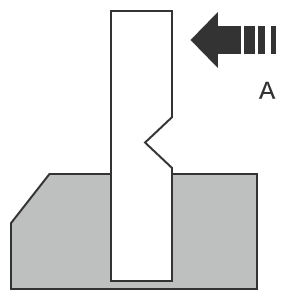
- A
- Ütés iránya
a = E/b
- a
- Ütés erőssége (J/m)
- E
- A töréshez szükséges energia (elnyelt energia) (J)
- b
- A próbadarab szélessége a bevésett oldalon (m)
Az elnyelt energia kiszámításának képlete a következő.
E = WR(cosθβ − cosθα) − L
- E
- Elnyelt energia (J)
- W
- Kalapács súlya (N)
- R
- A kalapács forgástengelyének középpontja és a kalapács súlypontja közötti távolság (m)
- θβ
- Az a szög, amelybe a kalapács a próbadarab törése után elfordul (°)
- θα
- A kalapács emelési szöge (°)
- L
- Súrlódás okozta energiaveszteség
A hagyományos törésfelület-mérés során felmerülő problémák
A hagyományos felületmérés mikroszkóp használatával történik. Ez azonban hosszú mérési idővel jár és felmerül az a probléma, hogy az eredményeket nem lehet számszerűsíteni. Továbbá, a mérési eredmények bizonyos esetekben nem tárolhatók vagy digitalizálhatók, ami rendkívül megnehezíti a törésfelület értékelését.
Mérési nehézségek - Mikroszkóp
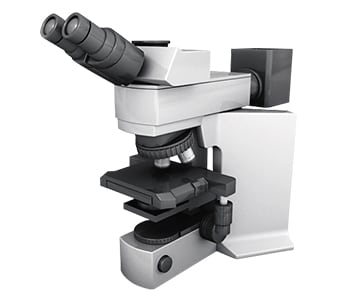
A mikroszkópok információt nyernek a felületről. A tárgyasztal mozgásának mértékéből a barázdaszélesség, a fókuszváltás mértékéből pedig a mélység mérése lehetséges. A mikroszkópok nagyfokú nagyítást is biztosítanak, lehetővé téve a törésfelület részletes megfigyelését.
Ugyanakkor a mérések az emberi szemtől függenek, ami a mérési eredmények operátoronkénti eltérését eredményezi. További gond, hogy mivel a mikroszkópokat eredetileg nem mérésre szánták, előfordulhat, hogy nem lehet számszerűsíteni a mérési eredményeket, vagy a számszerűsített mérési értékek megbízhatósága alacsony lehet.
Törésfelület-mérési megoldások
A hagyományos mikroszkópokkal végzett mérés olyan problémákat vet fel, mint a mérési eredmények eltérése és az, hogy a mérési eredményeket nem lehet számszerűsíteni. Ezen mérési problémák megoldására fejlesztette ki a KEYENCE a 3D optikai profilmérő VR sorozatát.
A VR sorozat pontosan rögzíti a teljes célfelület 3D alakját anélkül, hogy érintkezne a céltárggyal. A 3D alakzatot is méri úgy, hogy 3D szkennelést végez a tárgyasztalon, mindössze egy másodperc alatt. Képes azonnali és mennyiségi mérés elvégzésére, hiba nélkül a mérési eredményekben. Ez a szakasz a VR sorozat néhány specifikus előnyét mutatja be.
1. előny: A mennyiségi kiértékelés akár egy másodperc alatt is elvégezhető.
Lehetőség van a fém törésfelület felületének és térfogatának, valamint a keresztmetszeti terület és a felület arányának mérésére. Mivel egyetlen méréssel akár egy másodperc alatt is nagy terület mérhető, ez lehetővé teszi a mérési minták számának nagymértékű növelését. A hagyományos mikroszkópokkal és mérőműszerekkel mindez nehézkes a méréshez szükséges hosszú idő miatt.
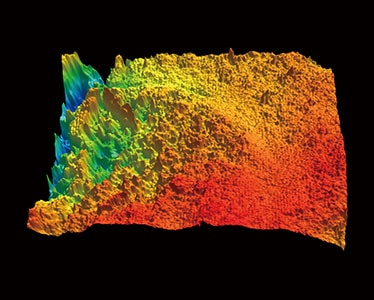
A VR sorozat a maximális és minimális pontokat is képes mérni egy széles területen, ami korábban sok időt és erőfeszítést igényelt. Valamennyi mérési eredmény digitalizálásra kerül, jelentősen csökkentve az adatok későbbi összehasonlításához és elemzéséhez szükséges munkát.
2. előny: A mérőrendszer támogatja a nyomonkövethetőséget.
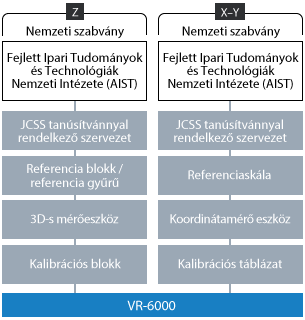
A VR sorozat egy érintésmentes 3D mérőműszer, amely biztosítja a nemzeti szabványok szerinti nyomonkövethetőséget. A mérési pontosság mind a pontosság, mind a megismételhetőség tekintetében garantált, így olyan rendkívül megbízható mérési eredményekkel szolgál, amelyekben megbízhat. A kalibrációs tanúsítványokat alapfelszereltségként a főegységgel és a kalibrációs táblával együtt megküldjük.
A fent leírtak alapján, a VR sorozat egy olyan mérőrendszer, amely teljes nyomonkövethetőséget biztosít, és lehetővé teszi mérőrendszerként történő használatát.
Az alapfelszereltséghez tartozik egy kalibrációs mérőműszer is, amely egy vizsgálati jelentést és egy kalibrálási tanúsítványt is tartalmaz. A mérőműszer a JCSS tanúsító laboratóriumai által használt referenciaskálához kapcsolódik. Ennek eredményeként a felhasználók könnyen elvégezhetik a kalibrálást a helyszínen.
Összegzés: Töredezett felületek mennyiségi mérése
A hagyományos műszerek csak megfigyelésre képesek, az eredmények számszerűsítése nehézkes, időigényes és pontatlan. A VR sorozat lehetővé teszi a mérések gyors elvégzését, és számszerűsített eredményeket ad. Ez lehetővé teszi a törési felületek Charpy-féle ütővizsgálat során történő értékelését, nagyobb pontossággal és hatékonysággal. A rendszer természetesen az Izod-féle ütőszilárdsági vizsgálat során is használható a törési felületek értékelésére.
- A törési felület területe, térfogata és érdessége számszerűsíthető.
- Nincs mérési eltérés a különböző operátorok között.
- A mérés egyszerűen elvégezhető a céltárgy tárgyasztalra helyezésével és egyetlen gomb megnyomásával, pozicionálás vagy egyéb előkészítés nélkül. Így nincs szükség speciális operátor kijelölésére a mérési munkákhoz.
- A 3D alakzatok könnyen, nagy sebességgel, nagy pontossággal mérhetők. Ez lehetővé teszi nagyszámú céltárgy rövid idő alatt történő mérését, elősegítve a minőség javítását.
Ez a rendszer lehetővé teszi a korábbi 3D alakzatadatokkal való összehasonlítást, valamint az egyszerű adatelemzést, például az érdességeloszlást. Hatékonyan használható a legkülönfélébb célokra, ideértve a hőmérséklet-változásokból eredő törésfelületi jellemzők trendelemzését és a törési feltételek ellenőrzését.