A hőkezelés utáni deformációmérés problémáinak megoldása
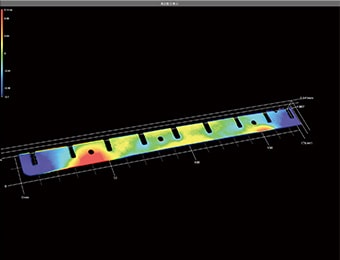
Általánosságban elmondható, hogy a hőkezelés olyan folyamat, amely hőt alkalmaz az anyagokon vagy termékeken. A hőkezelés magában foglalja a fémanyagok melegítéssel történő feldolgozását, valamint az élelmiszerek és egyéb termékek hősterilizálását. Ez a szakasz a fém hőkezelési folyamatokból származó deformációját vizsgálja. Míg a hőkezelésből adódó deformációk lehetnek egyszerűek, például összenyomódás vagy vetemedés a négyzet keresztmetszetű gerendák és rudak esetében, addig az összetett alakzatú termékeknél háromdimenziós deformáció léphet fel. Ezen alakzatok mérésére fejlett technológiákra van szükség.
Ez az oldal a vas- és acélanyagok esetében, a szerkezetük szabályozására és tulajdonságaik javítására alkalmazott hőkezelések okozta deformációkkal kapcsolatos alapvető ismereteket magyarázza el. Kitér a deformációmérés során felmerülő problémákra, és néhány lehetséges megoldást is javasol.
- Fémek hőkezelése
- Példák a hőkezelés által okozott deformációra (fázisátalakulás miatt bekövetkező térfogatváltozás)
- A hőkezelés által okozott deformációs problémák megelőzését célzó intézkedések
- A hőkezelés utáni hagyományos deformációmérés problémái
- A hőkezelés utáni deformációmérés problémáinak megoldása
- Összegzés: Drasztikus javulás a hőkezelés utáni deformációmérés terén
Fémek hőkezelése
A fémek hőkezelése egy olyan feldolgozási technika, amely felmelegíti és lehűti a fémet annak érdekében, hogy az alakzat megváltoztatása nélkül módosítsa tulajdonságait. A módosítandó tulajdonságok közé tartozik a szilárdság, keménység, tartósság, ütésállóság, kopásállóság, korrózióállóság, a megmunkálási tulajdonságok és a hidegen történő megmunkálhatóság.
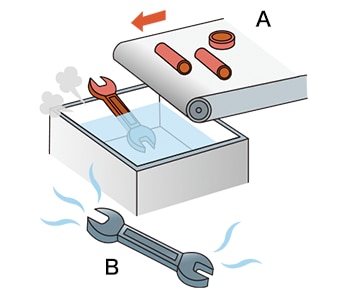
- A
- Fűtés (amíg a fém vörössé nem válik)
- B
- Hűtés (amíg a felmelegített fém megfeketedik)
Példák a hőkezelés által okozott deformációra (fázisátalakulás miatt bekövetkező térfogatváltozás)
Számos hőkezelési módszer létezik, ideértve a kioltást, az edzést, a lágyítást és a normalizálást. Ezen folyamatok során a fázisátalakulás néven ismert jelenség megy végbe.
A fázisátalakulás egy olyan folyamat, amely a hőkezelés során megy végbe, amikor a fém szilárd halmazállapotából folyékonnyá, majd folyékonyból szilárd halmazállapotúvá változik. Ez azért következik be, mert a fém aktuális formája (szerkezete) megváltozik, amikor kristályrácsa a hőmérséklet hatására megváltozik. Amikor a fázisátalakulás során a szerkezet megváltozik, a térfogat is megváltozik, ami deformációt okoz.
Például, amikor egy eutektoid acélt, ami egy körülbelül 0,8% szenet tartalmazó acél, szobahőmérsékletről felmelegítenek, hogy ausztenit szerkezetet hozzanak létre, majd lehűtik, akkor az a szerkezetváltozás miatt deformálódik. A fázisátalakulás utáni szerkezet a hűtési módtól függően változik, ezért a hűtési mód is befolyásolja az alakváltozás mértékét.
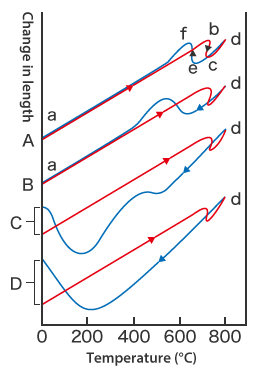
Ez a grafikon a különböző hűtési módszerekből adódó alakváltozások különbségeit mutatja.
Az A esetében a fém a melegítés hatására kitágul (a → b), és a fázisátalakulás miatti méretváltozások körülbelül 750 °C-on láthatók melegítés közben (b → c) és körülbelül 730 °C-on hűtés közben (e → f).
A C esetben (olajhűtés) és D esetben (vízhűtés) a hűtés után egyértelmű hosszváltozás tapasztalható.
- A: Kemencehűtés (lassú hűtés)
- A fém hevítés után a kemencében marad, és a kemencében hűl le. Ez a módszer a fémet körülbelül 30 °C-os óránkénti sebességgel hűti. A fázisátalakulás utáni szerkezet perlit.
- B: Léghűtés
- A fémet melegítés után eltávolítják a kemencéből, és szobahőmérsékleten lehűtik. A fázisátalakulás utáni szerkezet szorbit.
- C: Olajhűtés
- A felhevített fémet olajban lehűtik. A fémet általában olajban hűtik le körülbelül 60-80 °C-ra. A fázisátalakulás utáni szerkezetben az ausztenit szerkezet egy része trusztittá alakul.
- D: Vízhűtés
- A fémet körülbelül 40 °C-os vízben hűtik. A fázisátalakulás utáni szerkezet martenzit.
A hőkezelés által okozott deformációs problémák megelőzését célzó intézkedések
Az előző részben ismertetett fázisátalakuláson túlmenően a hőkezelés okozta deformációs problémák egyéb okai közé tartozik a helytelen vagy egyenetlen felületforma vagy felmelegedés/lehűlés. Ez a rész ezeket a deformációs problémákat, azok okait és a megelőzésükre vonatkozó intézkedéseket ismerteti.
Kioltási repedések
Ez egy olyan probléma, amelynél anyagrepedések lépnek fel. Az oltást követő napon vagy azt követően fordulhat elő, miután az anyag körülbelül 200 °C-ra vagy az alá hűlt.
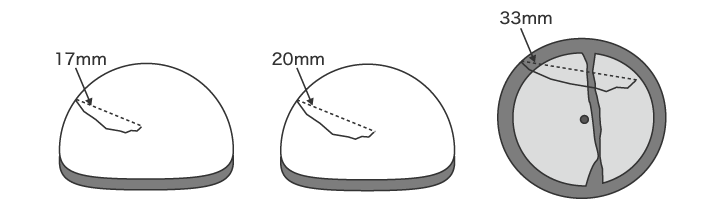
- Okok:
- A lehetséges okok közé tartozik az egyenetlen fűtés vagy hűtés miatt bekövetkező térfogat-növekedés okozta alakhibák, a nem megfelelő edzés közvetlenül az kioltás után, valamint a túl magas kioltási hőmérséklet.
- Ellenintézkedések:
-
- Ellenőrizze a termék alakját és felületi jellemzőit.
- Ne hűtse a kioltott anyagokat körülbelül 200°C-ra vagy az alá.
- A kioltás után azonnal el kell végezni az anyagok edzését.
- Csökkentse a kioltási hőmérsékletet.
Köszörülési repedések
Ez a probléma azt jelenti, hogy az acélanyag megrepedezik, amikor hőkezelést követően megköszörülik. Kétféle köszörülési repedés létezik: 1-es típusú köszörülési repedések, amelyek akkor keletkeznek, ha a vágással, polírozással vagy más módszerrel megmunkált felület hőmérséklete eléri a körülbelül 100 °C-ot, és a 2-es típusú köszörülési repedések, amelyek akkor keletkeznek, amikor a vágással, polírozással vagy más módszerrel megmunkált felület hőmérséklete eléri a körülbelül 300 °C-ot.
-
1. típusú köszörülési repedés
-
2. típusú köszörülési repedés
- Okok:
- A maradék ausztenit kitágul, amikor martenzitté alakul. A tágulás okozta feszültség az anyag megrepedését okozza. Ez a deformáció akkor is előfordulhat, ha a vágással, polírozással vagy más módszerrel megmunkált felület hőmérséklete megközelítőleg eléri a 650-850 °C-ot.
- Ellenintézkedések:
-
- Végezze el a megfelelő edzést.
- Csökkentse a köszörülési súrlódásból származó hőt.
Kioltási deformáció
A hőkezelés által okozott acéldeformációnak két típusa van: az oltás vagy edzés során bekövetkező hőtágulás vagy összehúzódás által okozott hődeformáció, valamint a fázisátalakulás által okozott térfogatváltozás.
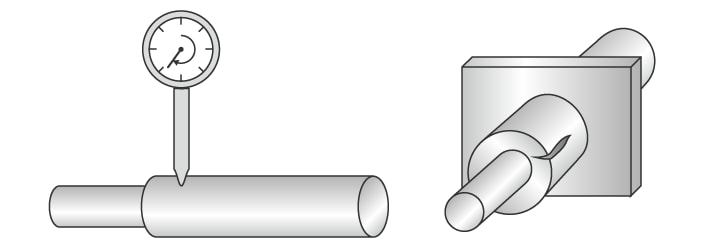
- Okok:
- Ez a deformáció egyenetlen melegítés vagy hűtés, gyors felmelegedés vagy hűtés, vagy egyenetlen vastagságú alkatrészek eredményeként következik be. Ha egy anyagnak összetett alakzata van, akkor az anyag hőmérsékletének egyenetlen eloszlása is okozhat ilyen deformációt.
- Ellenintézkedések:
-
- Ellenőrizze az alakzatot, hogy a terméket egyenletesen lehessen melegíteni és hűteni.
- Csökkentse a fűtési és hűtési sebességet.
A hőkezelés utáni hagyományos deformációmérés problémái
Rendkívül fontos ellenőrizni, hogy a hőkezelés utáni méretek és alakzatok a tűréshatáron belül vannak-e. Különösen az összetett alakzatú termékek igényelnek nagy pontosságú, kvantitatív 3D alakméréseket.
A hagyományos hőkezelés utáni alakváltozás-mérés profilmérő rendszereket vagy koordinátamérő gépeket használ. A hagyományos koordináta mérőgéppel vagy profilmérő rendszerrel végzett méréseknél azonban számos probléma vetődik fel. Ide tartozik az, hogy a pontos mérésekhez nagyfokú nehézség szükséges, valamint, hogy a mért értékek eltérnek.
A profilmérő rendszerrel történő deformációmérés során felmerülő problémák
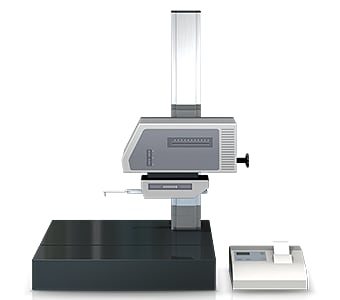
A céltárgy profilját egy profilmérő rendszer méri és rögzíti úgy, hogy a felületét egy érintőceruzával követi végig. Az elmúlt években olyan profilmérő rendszereket fejlesztettek ki, amelyek érintőceruza helyett lézert használnak az összetett alakzatok mérésére a profil érintésmentes követésével. Egyes modellek képesek a felső és az alsó felület mérésére is.
A profilmérő rendszer esetében azonban pontos mérési vonalakat kell használni a mérési pontokhoz.
Ez a következő problémákat veti fel.
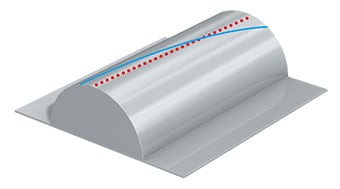
- A mérési munka sok időt igényel, ideértve a minta ülékre rögzítéséhez és vízszintbe állításához szükséges időt. Emellett a profilmérő rendszerek használatához kapcsolódó ismeretek és készségek is szükségesek a céltárgy pontos szintbe állításához.
- A profilmérő-rendszer érintőceruzája felfelé és lefelé egy íven mozog, melynek középpontja az érintőceruza karjának forgástengelye, az érintőceruza hegye pedig az X-tengely irányába mozog. Ez hibát okoz az X-tengely adataiban.
- A kívánt vonal végigkövetése az érintőceruzával rendkívül nehéz munka, és már az érintőceruza enyhe elmozdulása is hibát okoz a mért értékekben.
- Nehéz továbbá a céltárgyak számának növelése, mert pontosan meg kell határozni a mérési helyeket.
- A céltárgynak csak egy része mérhető, a teljes felület értékelése nem lehetséges.
A koordináta mérőgéppel történő deformációmérés során felmerülő problémák
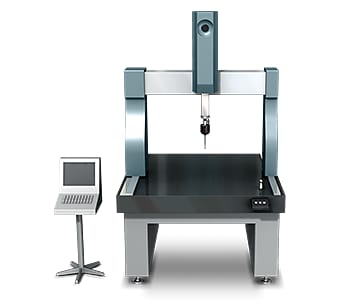
A tipikus koordinátamérő gépek szondát használnak a felület pásztázására vagy lekövetésére, és több pontot gyűjtenek össze egy meghatározott magasságban.
Ez a mérési módszer a következő problémákat veti fel.
- A szonda megfelelő mozgásának biztosítása rendkívül nehéz feladat, különösen egy henger vagy íves felület vagy egy kör közepén áthaladó egyenes vonalak esetében. Ha egy lekerekítés vagy legömbölyítés középponti szöge széles, akkor mivel a teljes kört egy rövid ív alapján számítják ki, még egy kis mérési hiba is jelentős gondokat okozhat. A mérési pontok ilyen jellegű eltérései a mért értékek enyhe eltérését eredményezhetik.
- Kisebb 3D alakzat mérésekor előfordulhat, hogy a szonda nem tudja megérinteni a mérési pozíciókat. Mivel a mérési pontosság arányos a mért pontok vagy vonalak számával, nagyszámú pontot vagy vonalat kell megmérni.
Ezért a koordináta mérőgéppel történő mérés jelentős problémákat vet fel, többek között azt, hogy nem minden munkahelyi operátor tud pontosan alakzatokat mérni, hogy vannak egyáltalán nem mérhető részek, valamint hogy korlátozott a hely a gép beszerelésére.
A hőkezelés utáni deformációmérés problémáinak megoldása
Ezek a mérőműszerek egy tárgy vagy szondahegy pozicionálása esetén problémákba ütközhetnek, és nehezen képesek általános mérési adatokat biztosítani a 3D felületre vonatkozóan, mivel egyszerűen pontokkal vagy vonalakkal mérnek. Ezen problémák megoldására fejlesztette ki a KEYENCE a 3D optikai profilmérő VR sorozatát.
A VR sorozat mindössze egy másodperc alatt pontosan rögzíti a teljes célfelület 3D alakját anélkül, hogy érintkezne a céltárggyal. Képes a teljes 3D felület azonnali és pontos számszerűsítésére mérési hibák nélkül. Ez a szakasz a VR sorozat néhány specifikus előnyét mutatja be.
1. előny: Nagy számú pontot képes megméri, akár egy másodperc alatt is
A VR sorozat mindössze egy másodperc alatt beolvassa a felszíni adatokat (800 000 pont) a 3D céltárgy alakjához, így drasztikusan csökkenti a nagyszámú pont méréséhez szükséges időt. Azonnal és pontosan megméri a maximális és minimális egyenetlenségeket a teljes célfelületen, lehetővé téve a céltárgy összes helyének gyors kiértékelését az előre beállított tűrések alapján.
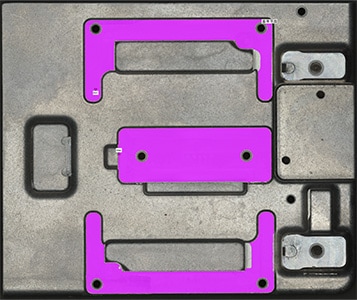
A munkadarab szkennelése után a profilja (keresztmetszete) a korábbi mérési helyektől eltérő helyeken is mérhető. Ez szükségtelenné teszi ugyanazt a céltárgyat újra beállítani és megmérni.
2. előny: A mérési adatok összehasonlíthatók referenciaadatokkal
A VR sorozat nem csak hatékony adatgyűjtésre képes. A mérési adatok egy listában jeleníthetők meg, és az összes adatra egyidejűleg ugyanaz az elemzési tartalom alkalmazható.
Több célalakzat hőkezelés előtti és utáni mérésével gyorsan ellenőrizhető a kapott adatok különbsége, valamint a rossz termékek eltérésének mértéke a referenciatermékhez képest. Ez lehetővé teszi a hőkezelés okozta alakváltozások egyszerű kvantitatív elemzését és értékelését.
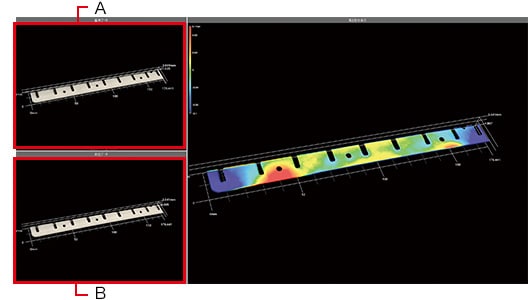
- A
- Referencia adat
- B
- Mérési adatok
A VR sorozat gyorsan képes bonyolult alakzatú céltárgyakat mérni, ami korábban sok időt és munkát igényelt volna. Nemcsak az adatok gyors rögzítése, hanem az összes mérési eredmény digitalizálása is megtörténik, ami jelentősen csökkenti az adatok összehasonlításához és elemzéséhez szükséges munkát.
Összegzés: Drasztikus javulás a hőkezelés utáni deformációmérés terén
Korábban a hőkezelés okozta deformáció mérése sok időt vett igénybe, ami korlátozta a mérhető minták számát. Egyes esetekben a mérés egyáltalán nem volt lehetséges az alkatrész összetett alakzata miatt. A VR sorozat azonban képes gyorsan megmérni és számszerűsíteni a deformációt ezeknél az alakzatoknál. Ennek eredményeként a VR sorozat nagyobb pontossággal és hatékonysággal tudja értékelni a termékminőséget.
- Jelentősen csökkenti az összetett alakzatok mérésére fordított időt a teljes felület adatainak egyidejű rögzítésével.
- Több mérési adathalmaz rögzítésével és összehasonlításával az alakváltozások különböző eltérései könnyen azonosíthatók és elemezhetők.
- Valódi kvantitatív mérés lehetséges, kiküszöbölve az eredmények emberi hibából eredő ingadozását.
- Egyszerűen helyezze a céltárgyat a tárgyasztalra, és nyomja meg a gombot a pontos adatok rögzítéséhez, így nincs szükség speciális operátorokra, mivel nincs szükség pozicionálásra vagy egyéb előkészítésre.
- Több céltárgyat rövid idő alatt, nagy sebességű szkenneléssel pontosan mér.
A VR sorozat képes összehasonlítani az adatokat a korábbi szkennelésekkel és CAD modellekkel, valamint elemezni az érdességet is.