Forrasztási alakzatok azonnali és pontos mérése
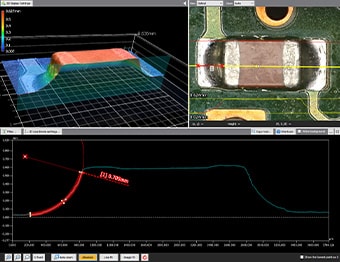
A távközlési és elektronikus vezérlők használata az autókban folyamatosan nő. Az okostelefonok, táblagépek, okosórák és más, ehhez hasonló hordozható eszközök egyre kisebb méretűvé és kompaktabbá válnak, így ezen eszközök összeszerelésének minősége és minőségbiztosítása egyre előrehaladottabb és fontosabb lesz.
Ez az oldal a NYÁK szerelési minőségével szorosan összefüggő forrasztószalagokkal és szerelési folyamatokkal kapcsolatos alapvető ismereteket mutatja be. Ezenkívül a forrasztás alaki és szerelési hibáinak kiküszöbölésére szolgáló ellenintézkedéseket, továbbá az alakmérési és -kiértékelési problémákat, valamint ezen problémák megoldásait is leírja.
- Forrasztószalagok
- Felületszereléses technológiai (SMT) folyamat, forrasztószalag-alakzatok, szerelési hibák és ellenintézkedések
- A hagyományos forrasztási alakzat mérés során felmerülő problémák
- A forrasztási alakzatok mérése során felmerülő problémák megoldása
- Összegzés
Forrasztószalagok
A NYÁK-ok esetében a forrasztószalag azt a részt jelöli, ahol a forraszanyagot a NYÁK-ra szerelt alkatrészek körül alkalmazzák. A forrasztás minőségét a forrasztószalag alakja alapján értékelik.
Megfelelő forrasz alakzat
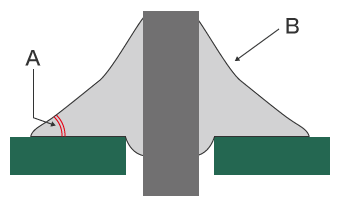
- A
- Szög: 15° és 45° között
- B
- Sima, ívelt homorú forma, fényes (A domború formát forrasztási foltnak nevezik, és szerelési hibákat okozhat.)
Az laphoz csatlakozó részen ellenőrizni és értékelni kell az olvadt és megszilárdult forrasztási alakzatot. Az alakzatnak sima homorúnak kell lennie, mint a Fuji lejtői. Amint az alábbi ábrán látható, a kisebb θ érintkezési szög (nagyobb nedvesíthetőség) jobb feltételeket jelez.
Ha azonban a melegítés nem elegendő, vagy ha túl sok a forraszanyag, akkor az vízcseppszerűen domború alakban megszilárdul. Ezt nevezik forrasztási foltnak, és ez a kötési szilárdság csökkenését vagy kapcsolódási hibát okozhat.
θ érintkezési szög és nedvesíthetőség
A nedvesíthetőséget a szilárd tárgy felülete és a rácsepegtetett folyadék (például megolvadt forraszanyag) közötti θ érintkezési szög értékében fejezzük ki. A kisebb A szög az ábrán (érintkezési szög θ) nagyobb nedvesíthetőséget jelent, ami azt jelzi, hogy a folyadék megfelelően került a szilárd tárgy felületére. A nagyobb szög kisebb nedvesíthetőséget jelent, mivel a szilárd tárgyfelület taszította a folyadékot.
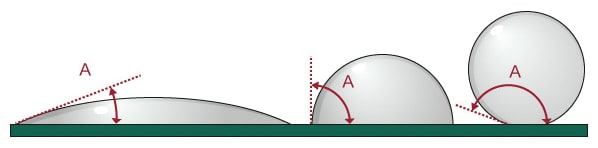
Felületszereléses technológiai (SMT) folyamat, forrasztószalag-alakzatok, szerelési hibák és ellenintézkedések
Ez a szakasz a felületszereléses technológia (SMT) általános folyamatát, a felületszereléshez felhasznált forraszanyag mennyiségét, a forrasztószalag alakját és a szerelési hibákat ismerteti.
Példa a felületszereléses technológia (SMT) folyamatára
Az alábbiakban az FA (Factory Automation - gyári automatizálás) felületszereléses technológiájának (SMT) általános folyamatait soroljuk fel.
- • Forrasztópaszta-nyomásos eljárás (krémes forraszanyag)
- Nagy pontosságú fémmaszk (lemez- vagy szitamaszk) felhasználásával a krémes forraszanyagot (forrasztópasztát) szitanyomással hordják fel gumibetéttel, így a pasztát csak a NYÁK szükséges helyeire hordják fel. Prototípus-készítés vagy kis mennyiségű gyártás során olyan tintasugaras nyomtató használható, amelyhez nem szükséges maszk.
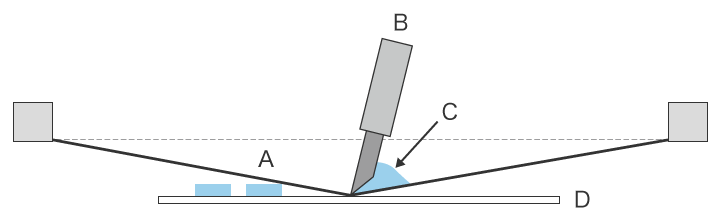
- A
- Fém maszk
- B
- Gumibetét
- C
- Forrasztópaszta (krémes forraszanyag)
- D
- NYÁK
- • Chipragasztási folyamat
- Ez a folyamat kötést alkalmaz a chip alkatrészek NYÁK-ra történő felszereléséhez. Elsősorban az ömlesztéses forrasztási eljárásban használják az alkatrészek rögzítésére, így azok nem esnek le az alkatrészek felszerelésekor. Az elektromosan vezető ragasztók használata lehetővé teszi az alkatrészek rögzítését és a folytonosság biztosítását.
- • Chipszerelési folyamat
- A csévére tekercselt szerelési elemeket tartalmazó kazetta az összeszerelőn van elhelyezve. Az összeszerelő a programnak megfelelően automatikusan elhelyezi a szerelési elemeket a NYÁK-on a megadott pozíciókban.
- • Újraömlesztéses eljárás
- A forrasztópaszta vagy chipragasztó felhordása és a szerelési elemek elhelyezése után a NYÁK-ot az újraömlesztő kemencébe szállítják és felmelegítik. Ez a melegítés megolvasztja a forrasztópasztát, így az megnedvesedik és szétterül a szerelési elemeken és a NYÁK szerelőlapján. Ezután lehűl és megszilárdul a teljes forrasztásig. Ugyanakkor ez a melegítés a chipragasztót is kikeményíti, hogy a ragasztott alkatrészek a helyükre kerüljenek.
- Mivel a forraszanyag olvadási hőmérséklete és a chipragasztó kikeményedési hőmérséklete eltérő, a folyamaton belül be kell állítani a fűtési hőmérsékletet és a hűtési sebességet. Az újraömlesztéses eljárás során óvatosan kell eljárni a NYÁK vetemedési kockázata miatt, amit a hő okoz.
Forrasztószalag-alakzatok, szerelési hibák és ellenintézkedések
A forrasztószalaghoz megfelelő mennyiségű forraszanyagot kell felhordani olyan formában, hogy az lefedje az alkatrész kapocselektródáját és a szerelőlapot.
Például egy általánosan használt többrétegű chipkondenzátor összeszerelésekor, ha a forraszanyag mennyisége megfelelő, a szalag befelé enyhén görbülő lejtős vonalakat képez a jobb és a bal kapocselektródákon. Ha túl sok forraszanyagot alkalmazunk, az a korábban leírtak szerint forrasztási foltot képez. Ha túl kevés a forraszanyag, akkor nem lehet megfelelő alakú és térfogatú forrasztási csíkot elérni. Mindkét esetben csökken a kötési szilárdság, és szerelési vagy kapcsolódási hibák léphetnek fel.
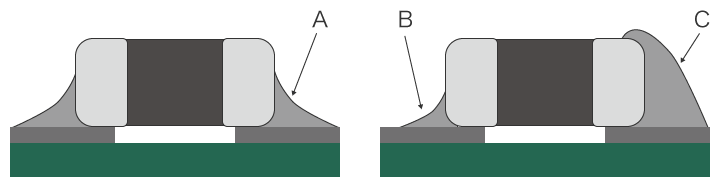
- A
- Megfelelő forraszanyag-mennyiség és forrasztási alakzat (a feltételeknek mindkét elektródán azonosaknak kell lenniük.)
- B
- Nem elegendő mennyiségű forraszanyag és forrasztási alakzat hiba
- C
- Túl sok forraszanyag és forrasztási alakzat hiba
Az újraömlesztéses eljárás során a megolvadt forraszanyag felületi feszültséget hoz létre a kapocselektródáknál. Ha különbség van a két kapcson lévő forraszanyag mennyisége között vagy a változik a fűtési hőmérséklet, akkor felületi feszültség különbség lép fel a két kapocsnál, és a „Manhattan jelenségként” ismert problémát okozza. Az elnevezés onnan ered, hogy az álló chip egy magas épületre hasonlít. „Sírkő-jelenségnek” is nevezik, mert egy sírkőre hasonlít.
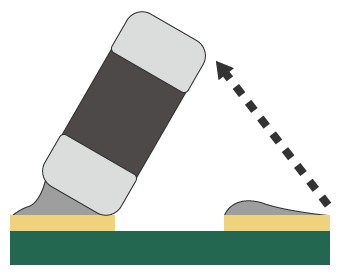
A hibaelhárítási intézkedések kidolgozásakor a forraszanyag mennyisége és minősége mellett fontos figyelembe venni a folyamat körülményeit, beleértve a újraömlesztő kemence előmelegítését és a hőmérséklet-emelkedési profil optimalizálását.
A NYÁK tervezését megelőző szakaszban olyan tényezőket is figyelembe kell venni, mint például a lap alakja és a hővel szembeni ellenintézkedések, amelyek lehetővé teszik a megfelelő forrasztás egyszerű kialakítását. Egyes esetekben a forrasztópaszta (krémforrasz) nyomtatásához használt fémmaszk javítása segíthet a forrasztási pontosság javításában.
A hagyományos forrasztási alakzat mérés során felmerülő problémák
Az alábbiakban a hagyományos profilmérő rendszerekkel végzett forrasztásmérés és -kiértékelés során felmerülő problémákat magyarázzuk el.
A forrasztási alakzatok kontakt típusú profilozó rendszerekkel történő alakmérése során felmerülő problémák
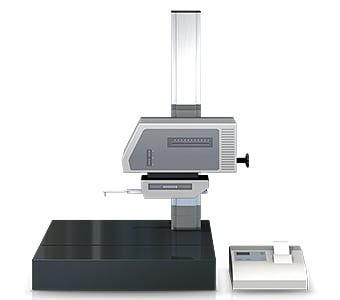
A céltárgy profilját egy profilmérő rendszer méri és rögzíti úgy, hogy a felületét egy érintőceruzával követi végig.
A céltárgy elhelyezése és szintezése, valamint egyéb előkészítése kulcsfontosságú a mérési teljesítmény szempontjából, amelyhez egy speciális operátornak haladó szintű beállítási és mérési munkálatokat kell elvégeznie. Ez sok időt és munkát igényel.
Mivel a 3D alakú forrasztás mérése vonalak segítségével történik, nem lehet a teljes alakzatot beazonosítani, így a kis méretű és sűrű NYÁK-ok mérése nehézkes lehet.
A forrasztási alakzatok mérése során felmerülő problémák megoldása
Eddig a forrasztás alakját 2-dimenziós ábrákkal magyaráztuk, a tényleges forrasztási alakzat azonban 3-dimenziós. A behelyezéses szerelésnél és a felületi szerelésnél számos forrasztási alakzat hiba léphet fel.
Emiatt a forrasztás alakjának mérésénél és megjelenésének vizsgálatánál a forrasztás pontos kiértékelése csak olyan precíziós mérőeszközzel lehetséges, amely képes mérni a 3D alakzatot (beleértve a felületet, magasságot, térfogatot és dőlést). Mivel a hagyományos mérőeszközök mérési vonalakra korlátozódnak, nehéz pontosan meghatározni a forrasztás alakját.
Ezen mérési problémák megoldására fejlesztette ki a KEYENCE a 3D optikai profilmérő VR sorozatát. Ez az eszköz pontosan rögzíti a teljes célfelület 3D alakját anélkül, hogy érintkezne a céltárggyal.
Ennél a rendszernél nincs szükség a céltárgy elhelyezésére. A felhasználók akár egy másodperc alatt is pontos és megismételhető méréseket végezhetnek, csupán a tárgyasztalra kell helyezniük a mintadarabot, és meg kell nyomniuk egy gombot. Ez lehetővé teszi a 3D profilok és 2D keresztmetszeti alakzatok pontos mérését, és bármely felhasználó számára lehetővé teszi, hogy a mérési eredmények változása nélkül, gyorsan és egyszerűen végezzen kvantitatív méréseket és értékeléseket. Ez a szakasz a VR sorozat néhány specifikus előnyét mutatja be.
1. előny: A teljes felület 3D alakja akár egy másodperc alatt is rögzíthető.
Mivel az alakzat illeszkedését a forrasztási alakzatmérő egy vonalon méri, a profilmérő rendszer pedig szintén egy vonal mentén érintőceruzával méri a hegesztési felületet, nehéz pontosan megmérni a hegesztés teljes alakját.
A VR sorozattal a felhasználó beszkennelheti a céltárgy 3D felületi alakját, hogy azonnal, akár egy másodperc alatt elvégezze az érintésmentes mérést.
Mivel lehetőség van az alacsony és nagy nagyítás közötti váltásra, nagy pontosságú méréseket nemcsak a teljes összeszerelt NYÁK-on, hanem az egyes alkatrészek esetében a forrasztás részletes alakzatán is lehet végezni.
A magassági színtérkép lehetővé teszi a forrasztás vagy az elektronikus alkatrész alakjának megjelenítését, ezzel gyorsan beazonosíthatók a rendellenes helyek és azok részletes értékei.
Az alkatrész beszkennelése után a mérési adatok tárolásra kerülnek, és a keresztmetszet profilmérése bármely vonalon, bármikor elvégezhető a múltbeli adatok felhasználásával. Ezek az adatok könnyen megoszthatók, lehetővé téve olyan feladatok zökkenőmentes elvégzését, mint a hiba okának azonosítása, a hibák kiújulásának megelőzésére szolgáló ellenintézkedések megfogalmazása, vagy összehasonlítások és trendelemzések elvégzése.
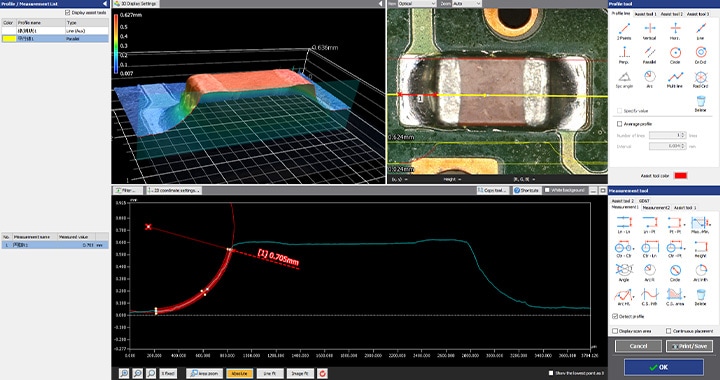
2. előny: A forrasztás alakja azonnal mérhető előzetes beállítás vagy pozicionálás nélkül.
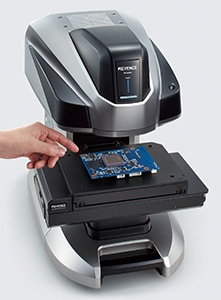
A VR sorozat lehetővé teszi a mérés azonnali elindítását anélkül, hogy a céltárgyat ülékre kellene rögzíteni, szigorú pozicionálást kellene vagy a mérőrendszeren bármilyen más nehézkes előzetes beállítást kellene elvégezni, vagy azt bonyolult lenne működtetni.
A 3D alakmérés egyszerűen elvégezhető a céltárgy tárgyasztalra helyezésével és egy gomb megnyomásával. Mivel a céltárgy jellemzőinek adatai alapján lehetséges az automatikus helyzetbeállítás, nincs szükség szigorú pozicionálásra. Ez lehetővé teszi az emberi tényezők okozta eltérések nélküli mennyiségi mérések elvégzését. Tapasztalati szinttől függetlenül bármely felhasználó pontos és megismételhető méréseket végezhet, növelve az adott idő alatt mérhető minták számát.
Ezenkívül, ez a sorozat az iparág első intelligens mérési funkcióját használja, amely automatikusan konfigurálja a mérési tartományt és mozgatja a tárgyasztalt. Ez kiküszöböli a mérési hossz, a Z-tartomány és az egyéb haladó beállítások elvégzéséhez szükséges munkát.
Összegzés
A forrasztószalag-alakzatokon kívül a VR sorozat azonnal és pontosan meg tudja mérni az adott tárgy teljes 3D felületét, lehetővé téve a felhasználók számára, hogy érintésmentes, nagy sebességű 3D szkenneléssel a teljes NYÁK-ra megjelenítse a szerelési feltételeket.
- A mérés akár egy másodperc alatt is elvégezhető. A színtérképen beazonosítható az egyes felületek forrasztószalagja (magassága), és a kívánt keresztmetszet profilmérésével részletes adatok nyerhetők ki.
- A nagyítás váltásával lehetőség nyílik a kis és kényes szerelésű alkatrészek teljes alakjának vagy részletes részeinek nagy pontosságú és érintésmentes mérésére.
- Nincs szükség pozícionálásra. Nincs szükség tapasztalatra vagy ismeretekre. Csak helyezze a céltárgyat a tárgyasztalra, és a mérés elvégzéséhez nyomja meg a gombot.
- A céltárgy a kívánt módon ábrázolható a 3D alakzat-színtérképének, a céltárgy képének és a profiladatoknak a kombinációjával. A vizuálisan könnyen érthető adatok megosztása lehetővé teszi a zökkenőmentes koordinálást és az ellenintézkedések megtételét minden egyes folyamat esetében.
- Rövid idő alatt nagyobb számú minta mérhető. Egyszerűen elvégezhető több mérési adathalmaz mennyiségi összehasonlítása és elemzése.
Ez lehetővé teszi több mérési adathalmaz egymás melletti összehasonlítását, valamint adatelemzést úgy, hogy a beállításokat az összes adatkészletre egyszerre alkalmazza. A VR sorozat segítségével rögzített 3D-s alakadatok megosztásával jelentősen csökkenthető a szükséges idő, és javítható a teljes folyamat hatékonysága, beleértve a mérést, a hibaelemzést és a hibaelhárítási intézkedéseket is.